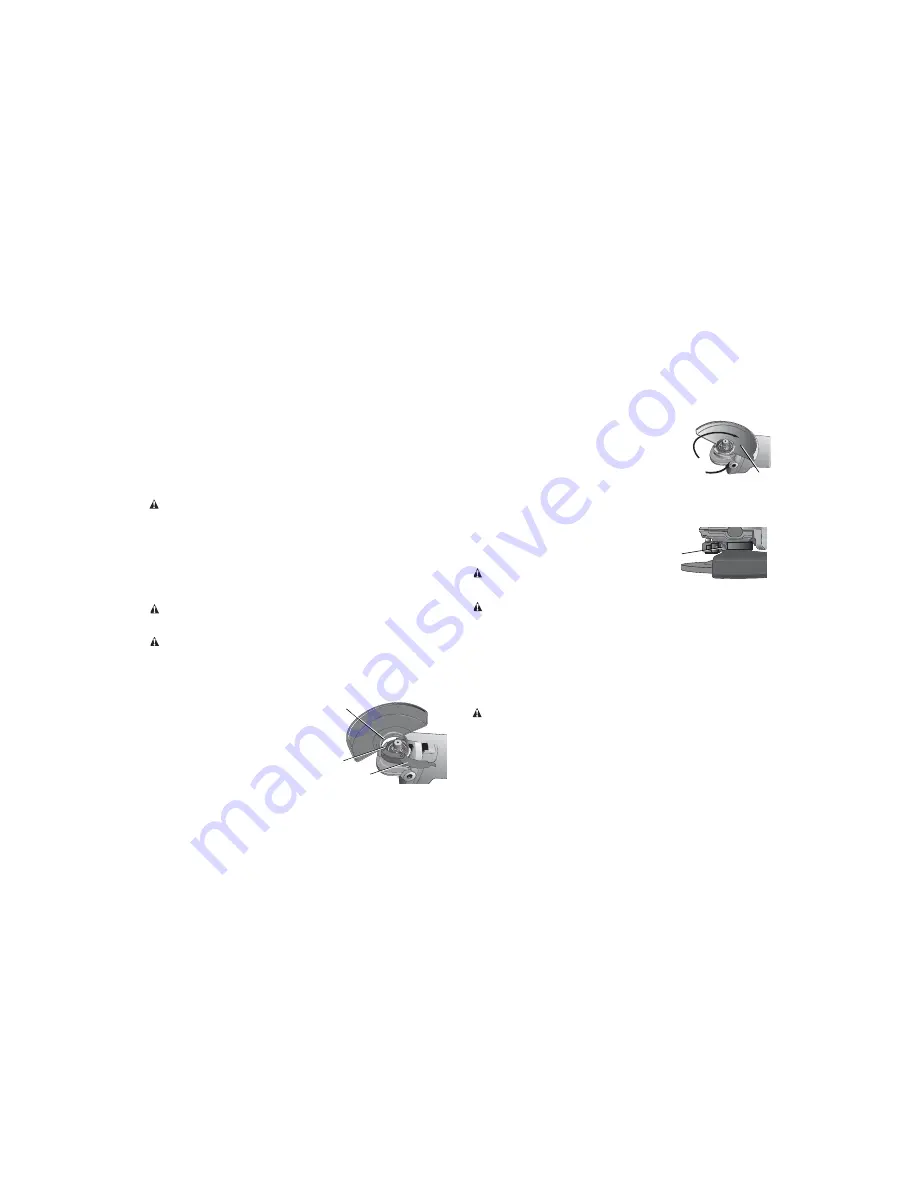
5
2. Push the guard down until the guard lugs engage and rotate freely in the groove
on the gear case hub.
3. With the guard latch open, rotate the guard (I) into
the desired working position. The guard body
should be positioned between the spindle and the
operator to provide maximum operator protection.
4. Close the guard latch to secure the guard on the
gear case. You should not be able to rotate the guard
by hand when the latch is closed. Do not operate the
grinder with a loose guard or the clamp lever in open position.
5. To remove the guard, open the guard latch, rotate the guard so that the arrows
are aligned and pull up on the guard.
NOTE:
The guard is pre-adjusted to the diameter of the
gear case hub at the factory. If, after a period of time,
the guard becomes loose, tighten the adjusting screw
(P) with clamp lever in the closed position.
CAUTION:
Do not tighten the adjusting screw with
the clamp lever in open position. Undetectable damage
to the guard or the mounting hub may result.
CAUTION:
If guard cannot be tightened by adjusting clamp, do not use tool and
take the tool and guard to a service center to repair or replace the guard.
OPERATION
Guards and Flanges
It is important to choose the correct guards and flanges to use with the grinder acces-
sories. See page 6 and this page for the correct accessories.
NOTE
: Edge grinding and cutting can be performed with Type 27 wheels designed
and specified for this purpose.
WARNING:
Accessories must be rated for at least the speed recommended on the
tool warning label. Wheels and other accessories running over rated accessory speed
may burst and cause injury. Every unthreaded accessory must have a 22 mm (7/8")
arbor hole. If it does not, it may have been designed for a circular saw and should not
be used. Use only the accessories shown on pages 6–7. Accessory ratings must be
above listed minimum wheel speed as shown on tool nameplate.
P
I
NOTE:
If the gear case and motor housing become separated by more than 6 mm
(1/4"), the tool must be serviced and re-assembled by a D
E
WALT service center.
Failure to have the tool serviced may cause brush, motor and bearing failure.
3. Re-install screws to attach the gear case to the motor housing. Tighten screws
to 2 nm (18in./lbs.) torque. Overtightening could cause screws to strip.
Accessories
It is important to choose the correct guards, backing pads and flanges to use with
grinder accessories. See pages 6–7 for information on choosing the correct acces-
sories.
WARNING:
Accessories must be rated for at least the speed recommended on the
tool warning label. Wheels and other accessories running over rated accessory speed
may burst and cause injury. Threaded accessories must have a M14x2 hub. Every
unthreaded accessory must have a 22 mm (7/8") arbor hole. If it does not, it may
have been designed for a circular saw and should not be used. Use only the acces-
sories shown on pages 6–7 of this manual. Accessory ratings must be above listed
minimum wheel speed as shown on tool nameplate.
Mounting Guard
MOUNTING AND REMOVING GUARD
CAUTION: Turn off and unplug the tool before making any adjustments or
removing or installing attachments or accessories. Before reconnecting the tool,
depress and release the paddle switch to ensure that the tool is off.
CAUTION: Guards must be used with all grinding wheels, sanding flap discs,
wire brushes, and wire wheels.
The tool may be used without a guard only when
sanding with conventional sanding discs. Some D
E
WALT models are provided with a
guard intended for use with depressed center wheels (Type 27) and hubbed grinding
wheels (Type 27). The same guard is designed for use with sanding flap discs (Type
27 and 29) and wire brushes. Grinding and cutting with wheels other than Type 27
and 29 require different accessory guards not
included with tool. Mounting instructions for
these accessory guards are included in the
accessory package.
1. Open the guard latch (M). Align the lugs
(N) on the guard with the slots (O) on the
gear case.
M
O
N