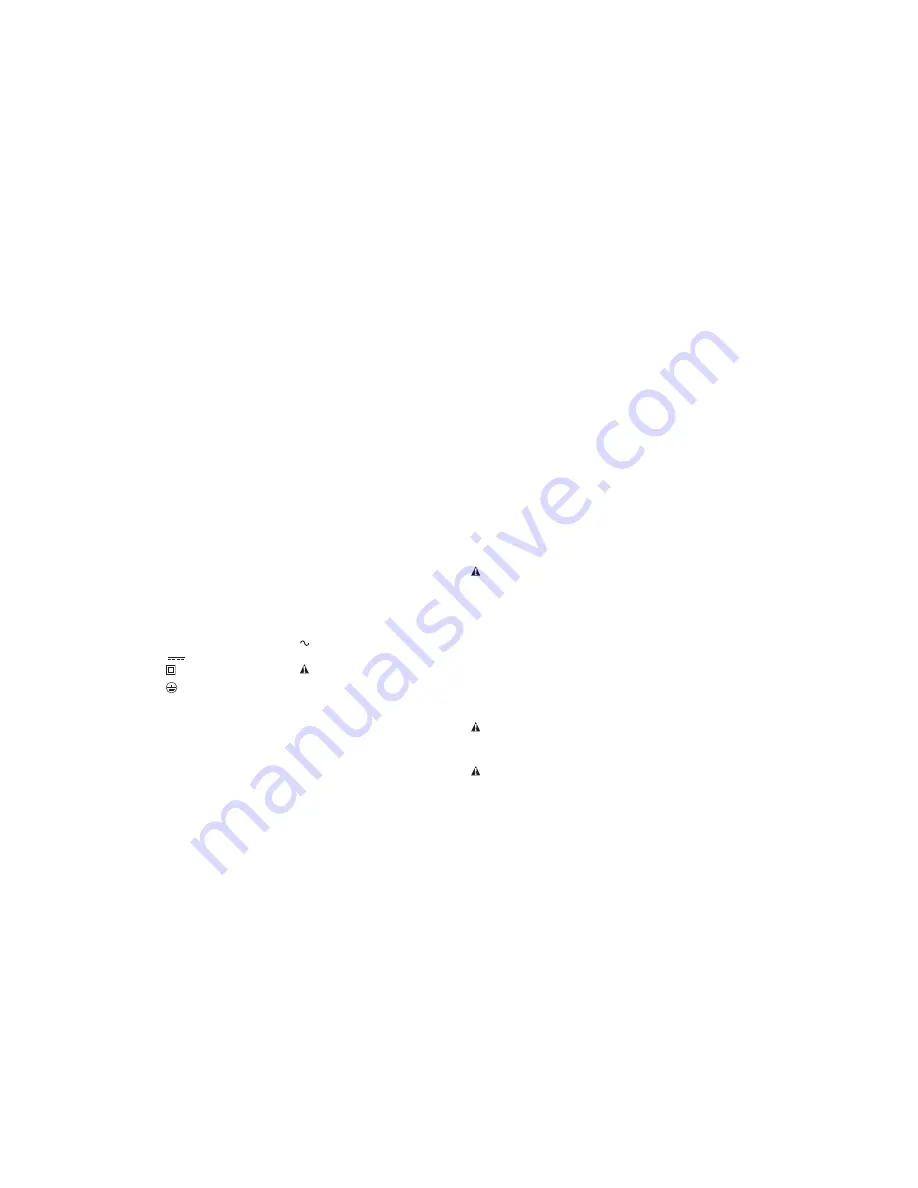
3
• Avoid bouncing the wheel or giving it rough treatment.
If this occurs, stop the
tool and inspect the wheel for cracks or flaws.
•
Direct sparks away from operator, bystanders or flammable materials.
Sparks may be produced while cutting and/or grinding. Sparks may cause
burns or start fires.
• Always use side handle. Tighten the handle securely
. The side handle should
always be used to maintain control of the tool at all times.
•
Never cut into area that may contain electrical wiring or piping.
Serious
injury may result.
• Clean out your tool often, especially after heavy use.
Dust and grit containing
metal particles often accumulate on interior surfaces and could create an elec-
tric shock hazard.
• Do not operate this tool for long periods of time.
Vibration caused by the operat-
ing action of this tool may cause permanent injury to fingers, hands, and arms.
Use gloves to provide extra cushion, take frequent rest periods, and limit daily time
of use.
•
Direct the Dust Ejection System (DES) away from operator and coworkers.
Serious injury may result (Fig. 1, K).
• The label on your tool may include the following symbols. The symbols and
their definitions are as follows:
V ..........volts
A ................amperes
Hz ........hertz
W ................watts
min ......minutes
............alternating current
....direct current
no ..............no load speed
........Class II Construction
..............safety alert symbol
........earthing terminal
…/min ........revolutions per minute
Causes and Operator Prevention of Kickback
• Kickback is a sudden reaction to a pinched, bound or misaligned wheel, wire
brush or flap disc causing an uncontrolled cut-off tool to lift up and out of the
workpiece toward the operator.
• When the wheel is pinched or bound tightly by the workpiece, the wheel stalls and
the motor reaction drives the unit rapidly back toward or away from the operator.
• Kickback is the result of tool misuse and/or incorrect operating procedures or
conditions and can be avoided by taking proper precautions as given below:
•
Maintain a firm grip with both hands on the unit and position your
body and arm to allow you to resist kickback forces.
Kickback forces
can be controlled by the operator, if proper precautions are taken.
•
When wheel is binding, or when interrupting a cut for any reason,
release the trigger and hold the unit motionless in the material until
the wheel comes to a complete stop. Never attempt to remove the
unit from the work or pull the unit backward while the wheel is in
motion or kickback may occur.
Investigate and take corrective actions
to eliminate the cause of wheel binding.
•
When restarting a cut-off tool in the workpiece, check that the wheel
is not engaged into the material.
If wheel is binding, it may walk up or
kickback from the workpiece as the tool is restarted.
•
Support large panels to minimize the risk of wheel pinching and kick-
back.
Large panels tend to sag under their own weight. Support must be
placed under the panel on both sides, near the line of cut and near the
edge of the panel.
WARNING:
Some dust created by power sanding, sawing, grinding, drilling, and
other construction activities contains chemicals known to cause cancer, birth
defects, or other reproductive harm. Some examples of these chemicals are:
• lead from lead-based paints,
• crystalline silica from bricks and cement and other masonry products, and
• arsenic and chromium from chemically-treated lumber (CCA).
Your risk from these exposures varies, depending on how often you do this type of
work. To reduce your exposure to these chemicals: work in a well ventilated area, a
nd work with approved safety equipment, such as those dust masks that are spe-
cially designed to filter out microscopic particles.
•
Avoid prolonged contact with dust from power sanding, sawing, grinding,
drilling, and other construction activities. Wear protective clothing and wash
exposed areas with soap and water.
Allowing dust to get into your mouth, eyes,
or lay on the skin may promote absorption of harmful chemicals.
WARNING:
Use of this tool can generate and/or disburse dust, which may cause
serious and permanent respiratory or other injury. Always use NIOSH/OSHA approved
respiratory protection appropriate for the dust exposure. Direct particles away from
face and body.
CAUTION:
Use extra care when working into a corner because a sudden, sharp
movement of the grinder may be experienced when the wheel or other accessory con-