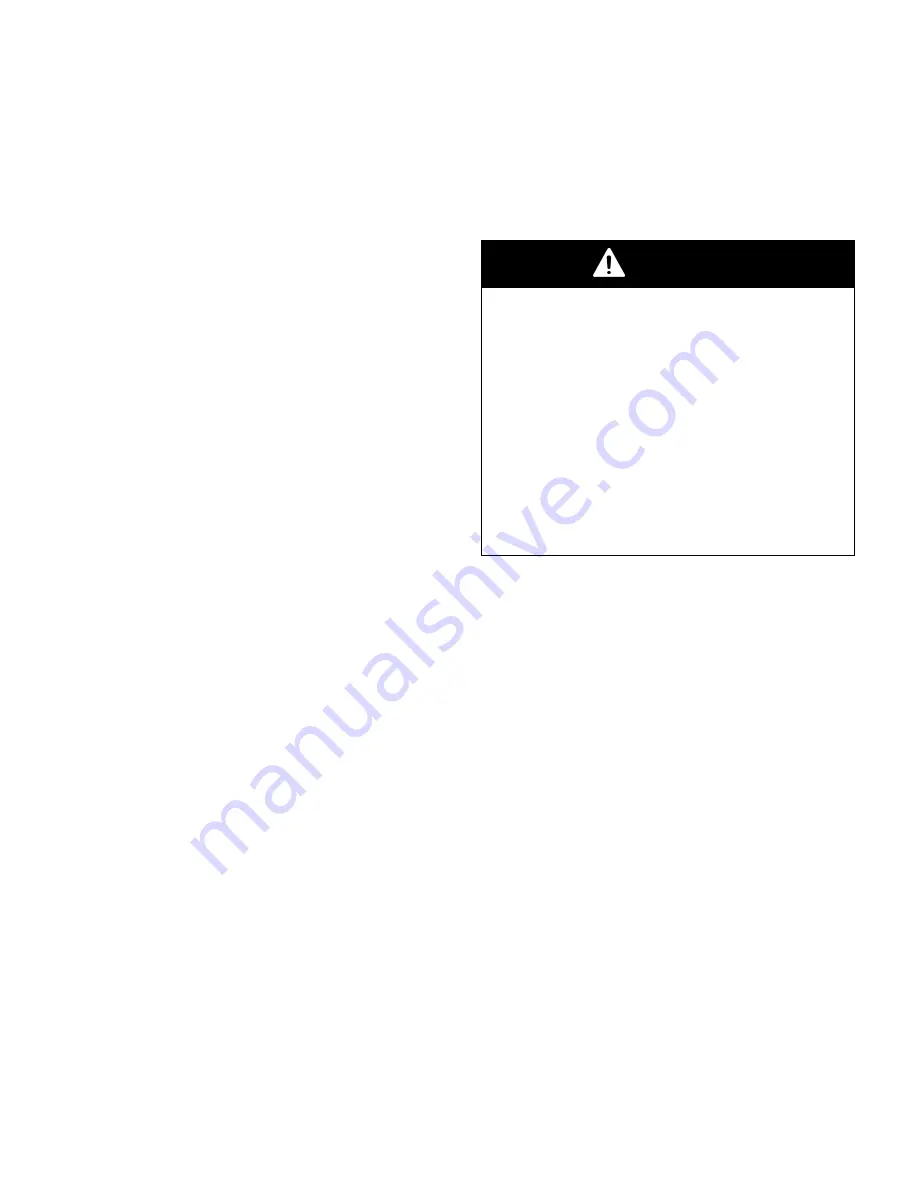
of this signal is five percent less than the expected firing
rate. For example, if the firing rate is 90%, the PWM to
(and from) the valve will be 85% duty cycle. The connec-
tor also provides the 24 VAC signal to energize the main
valve solenoid.
10.6
Connector 15-pins
The 15-pin connector provides connections for a vari-
ety of inputs and outputs to the furnace control. The
flame sense, pressure switches sense and limits sense
(Main Limit, MRLC and HALC) are connected to the I.F.C.
through this connector. Reference the wiring diagram
for the furnace printed in this document or on the in-
side of the furnace blower door for pin assignments for
troubleshooting. Le connecteur à 15 branches fournit
des connexions pour une variété d’entrées et de sor-
ties à la commande de la fournaise. La détection de
la flamme, détection des pressostat et des limites (
Main
Limit, MRLC et HALC
) sont connectés au contrôle à
travers ce connecteur.
Reportez-vous au schéma de
câblage de la fournaise imprimé dans ce document ou à
l’intérieur de la porte du ventilateur de la fournaise pour
connaître les affectations des branches pour le dépan-
nage.
10.7
ECM motor connection
This connector sends and receives messages to and
from the blower motor through a single peer-to-peer net-
work. The blower motor does not communicate on the
same communications buss as the furnace, condenser
and thermostat. Further, a different communications pro-
tocol is used.
For troubleshooting purposes, follow the wiring diagram
supplied in this manual and on the inside of the furnace
blower door.
10.8
COMMUNICATIONS L.E.D.
“RX” (Green) L.E.D.
– This L.E.D. indicates that commu-
nications is being sensed to or from (i.e.: something on
the network is trying to communicate) other components
(e.g. a condenser) on the network. This L.E.D. will blink
randomly any time a message is received by the furnace
control. If no blinking is seen within five minutes, it can
be assumed that there is not valid communications es-
tablished. Check wiring to make sure that all points are
connected properly.
Further, if this L.E.D. is on continuously, it is an indication
that mis-wiring has occurred.
“STAT” (STATUS) (Red)
L.E.D.
– This L.E.D. blinks twice slowly (¼ second ON, ¾
second OFF) upon power-up.
Pressing the learn button for two seconds will cause the
green “RX” L.E.D. to blink rapidly (for a short period) to
indicate an attempt at communications. If the L.E.D. does
not blink, communications cannot be established.
10.9
MEMORY CARD
WARNING
Do not replace the furnace control or memory card
of the furnace with a furnace control or mem-
ory card of another furnace or another compo-
nent (e.g. a memory card from a condenser or
air handler). The wrong furnace control or mem-
ory card may specify parameters which will make
the furnace run at undesired conditions including
(but not limited to) reduced airflow during heat-
ing causing excessive undesired operation of the
main limit control. Further, the memory card is
specific to the model number and BTU input rating
for a specific furnace and this information should
not be transported from one furnace (or compo-
nent) to another.
Furnace shared data is defined as data specific to a given
furnace that is critical for proper furnace operation. More
specifically, it is data which defines the operation of the
furnace and is unique to a given furnace platform and
model. The most critical of these data are the coefficients
that control the blower operation (i.e. define the blower
speed-torque operation). Because of this, each furnace
control is programmed with furnace shared data for that
model furnace only. The furnace shared data from any
given furnace can NOT be transferred to another furnace
for any reason. Doing so can adversely affect opera-
tion of the furnace. Further, if no furnace shared data
is present, the furnace will not operate in any mode and
a fault will be displayed.
10.10
REPLACING FURNACE
CONTROL
In the event that the furnace control must be replaced,
the memory card must be detached from the original fur-
nace control and retained with the furnace. Failure to
save and connect the memory card properly to the re-
placement control may result in no operation or undesired
operation of the furnace.
When replacing the furnace control, be sure to match the
DIP switch settings of the original control on the replace-
ment.
36
Summary of Contents for Chinook C105-M-V
Page 24: ...Figure 10 Typical gas pipe arrangement 23...
Page 27: ...Figure 11 Wiring Diagram 26...
Page 39: ...Figure 14 Wiring Diagram Modulating t stat 38...
Page 53: ...Table 17 CFM 52...
Page 54: ...Figure 15 Dimensional Drawing 53...
Page 55: ...14 PART LIST 54...
Page 56: ...Figure 16 Exploded view 1 55...
Page 57: ...Figure 17 Exploded view 2 56...
Page 59: ...Table 19 Parts list continued 58...
Page 60: ...Table 20 Parts list MS 59...