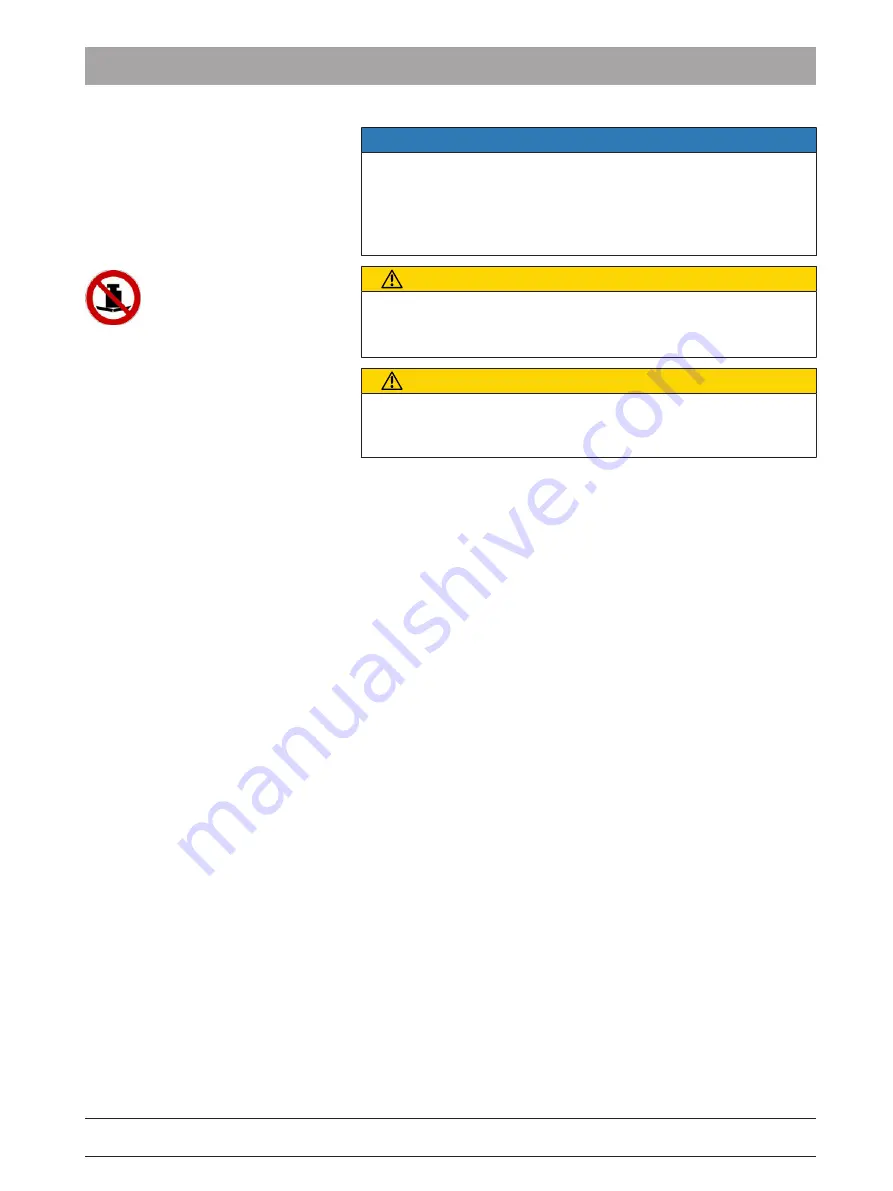
Dentsply Sirona
Operating Instructions CEREC Primemill
5 Installation and startup
5.3 Installation site
67 19 681 D3439
D3439.201.01.01.02 09.2019
19
NOTE
Installation in a cabinet
If the unit is installed in a cabinet, you must provide for adequate heat
exchange.
The ambient temperature surrounding the unit must be between 5 °C
(41 °F) and 40 °C (104 °F).
CAUTION
Risk of injury and damage to the unit
The unit can be tilted when the drawer is extended.
➢ Install the unit so that the front does not project beyond the base.
CAUTION
Risk of injury and damage to the unit
Avoid tilting the unit. Do not lean against the pulled-out drawer and do
not apply a vertical load of more than 5 kg onto the pulled-out drawer.