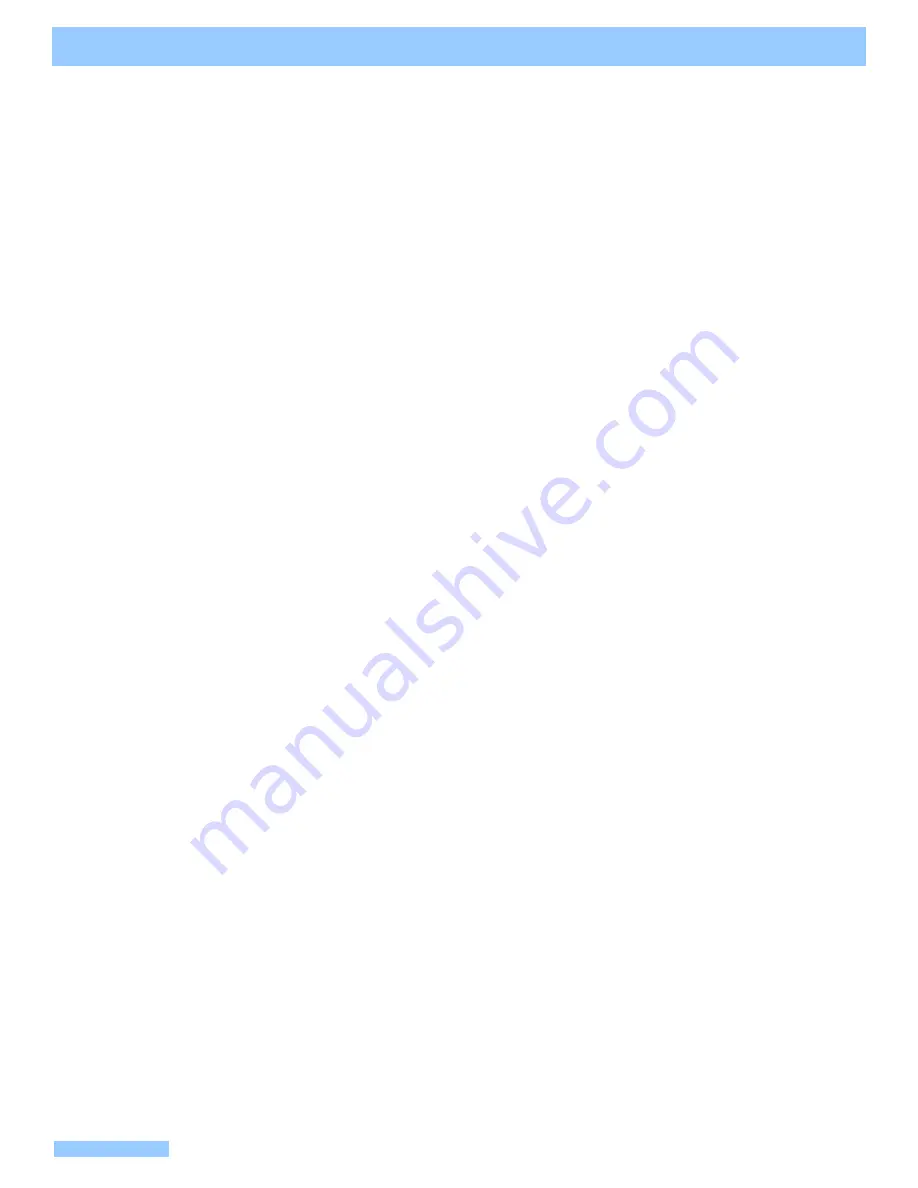
SECTION II – INSTALLATION
MOUNTING
This motor is designed to operate in any position. The mounting hub and two bolt mounting
flange are in full conformance with SAE standard. The motor shaft must be in alignment
with the shaft of the driven load and should be checked with a dial indicator. The mounting
pad or adaptor into which the fluid motor pilots must be concentric with the motor shaft
within 0.010 TIR to prevent bearing failure. This concentricity is particularly important if the
fluid if rigidly connected to the driven load without a flexible coupling.
PIPING
Connect inlet and outlet lines to the port block of the motor. It is recommended that the
case leakage line be connected to the top of the motor, but it may be connected to the
bottom or to the port block between the inlet and outlet ports. The case leakage line must
be of sufficient size to prevent back pressure in excess of 75 PSI and returned to the
reservoir below the surface of the oil as far from the supply suction a possible. All fluid
lines, whether pipe, tubing or hose must be adequate size and strength to assure free flow
through the motor. An undersize inlet line will prevent the motor from reaching full speed
and torque. An undersize outlet line will create back pressure in the motor from reaching
full speed and toque. An undersize outlet line will create back pressure in the motor and
cause improper operation. Flexible hose lines are recommended. If rigid piping is used,
the workmanship must be accurate to eliminate strain on the motor port block or to the
fluid connections. Sharp bends in the lines must be eliminated wherever possible. All
system piping must be cleaned with solvent or equivalent before installing motor. Make
sure the entire hydraulic system is free of dirt, lint, scale and other foreign material.
CAUTION: Do not use galvanized pipe. Galvanized coating can flake off with
continued use.
SERVICE INFORMATION
These hydraulic products are designed to give lone dependable service when properly
applied and their systems properly maintained. These general instructions apply to typical
systems. Specific instructions for particular equipment can be developed from them.
START UP PROCEDURE FOR
1. Read and understand the instruction manual. Identify components and their function.
NEW INSTALLATION
2. Visually inspect components and lines for possible damage.
3. Check reservoir for cleanliness and drain and clean as required.
4. Check fluid level and fill as required with filtered fluid at least as clean as that
recommended. Fill motor case as necessary.
5. Check alignment of drive.
6. Check oil cooler and activate it, if included in circuit. Check fluid temperature.
7. Reduce pressure settings of relief valve. Make sure accurate pressure readings can be
made at appropriate places.
8. If solenoids in system, check for actuation.
9. Start pump drive. Make sure pump and motor fill properly.
10. Bleed system of air. Recheck fluid level.
11. Cycle unloaded machine at low pressure and observe actuation (at low speed if
possible).
12. Increase pressure settings gradually steps. Check for leaks in all lines, especially in
pump and motor inlet lines.
13. Make correct pressure adjustments.
14. Gradually increase speed. Be alert for trouble as indicated by changes in sounds,
system shocks and air in fluid.
15. Equipment is operational.
FLUID
It is recommended that a hydraulic fluid be used as specified in Denison Bulletin 1107.
MAINTENANCE
This motor is self lubricating and preventive maintenance is limed to keeping the system
fluid clean by changing filters frequently. Fluid cleanliness level per NAS 1638, Class 8
above 15 micron or Class 9 under 15 micron must be maintained. This usually can be
accomplished by effective use of 10 micron filters. Do not allow dirt to accumulate on the
motor especially around the shaft seal. Keep all fittings and screws tight. Do not operate
the motor at pressures and speeds in excess of the recommended limit. If the motor does
not operate properly, check the Trouble Shooting Chart before attempting to overhaul the
unit. Overhaul is relatively simple and may be accomplished by referring to the procedures
in Section III.
4
Summary of Contents for Goldcup 6
Page 9: ...SECTION IV ASSEMBLY TOOL DRAWINGS 8...
Page 14: ...SECTION V ASSEMBLY PROCEDURES 13...
Page 21: ...SECTION V ASSEMBLY PROCEDURES 20...
Page 24: ......