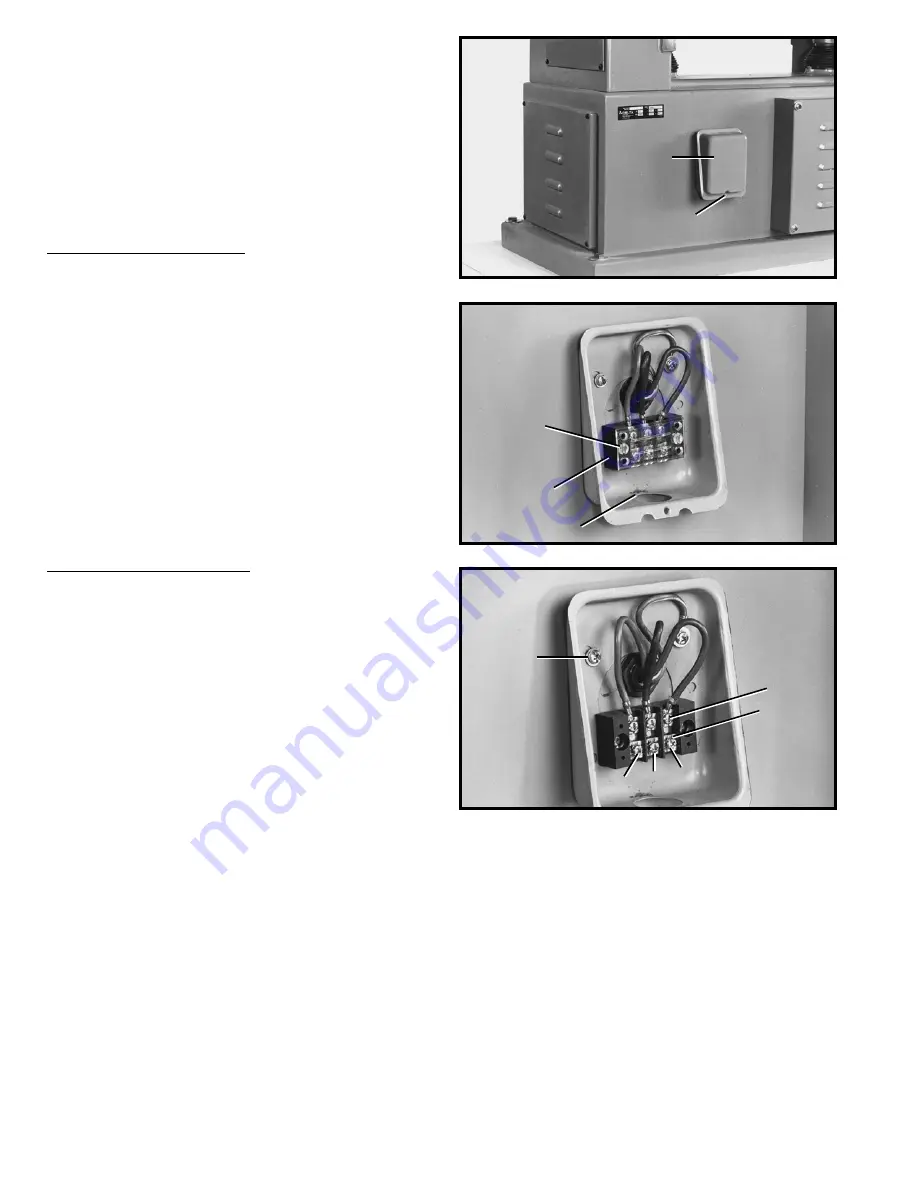
10
To bring power to this machine:
Loosen screw (A) Fig. 10, and remove cover (B) from
terminal box located at the rear of the machine. Bring the
power line up through the hole (C) Fig. 11, in terminal
box.
NOTE:
Strain relief and power cord clamp are not
supplied with the machine. Remove plastic shield (D) Fig.
11, from terminal strip (E).
Fig. 12
Fig. 11
Fig. 10
THREE PHASE OPERATION
If the planer is wired for three phase operation, connect
the three power lines to terminals (F), (G) and (K) Fig. 12,
and the green ground wire to ground terminal (H).
IMPORTANT: FOR THREE PHASE MACHINES ONLY.
After applying power to the machine, jog the power on
and off to check if the cutterhead is rotating correctly. If
the cutterhead is not rotating correctly, interchange any
two of the three power lines connected to terminals (F),
(G) and (K) Fig. 12.
NOTE:
The three phase motor is also capable of being
wired for 440 volt operation, but this connection must be
done by a qualified electrician and conform to the National
Electric Code and all local codes and ordinances.
SINGLE PHASE OPERATION
If the machine is wired for single phase operation, there
will be two power lines connected to the top terminals (L)
Fig. 12. Connect the two incoming power lines to the
corresponding bottom terminals (M) and connect the
green ground wire to ground terminal (H).
B
A
D
E
C
G
F
K
H
M
L
ELECTRICAL CONNECTIONS