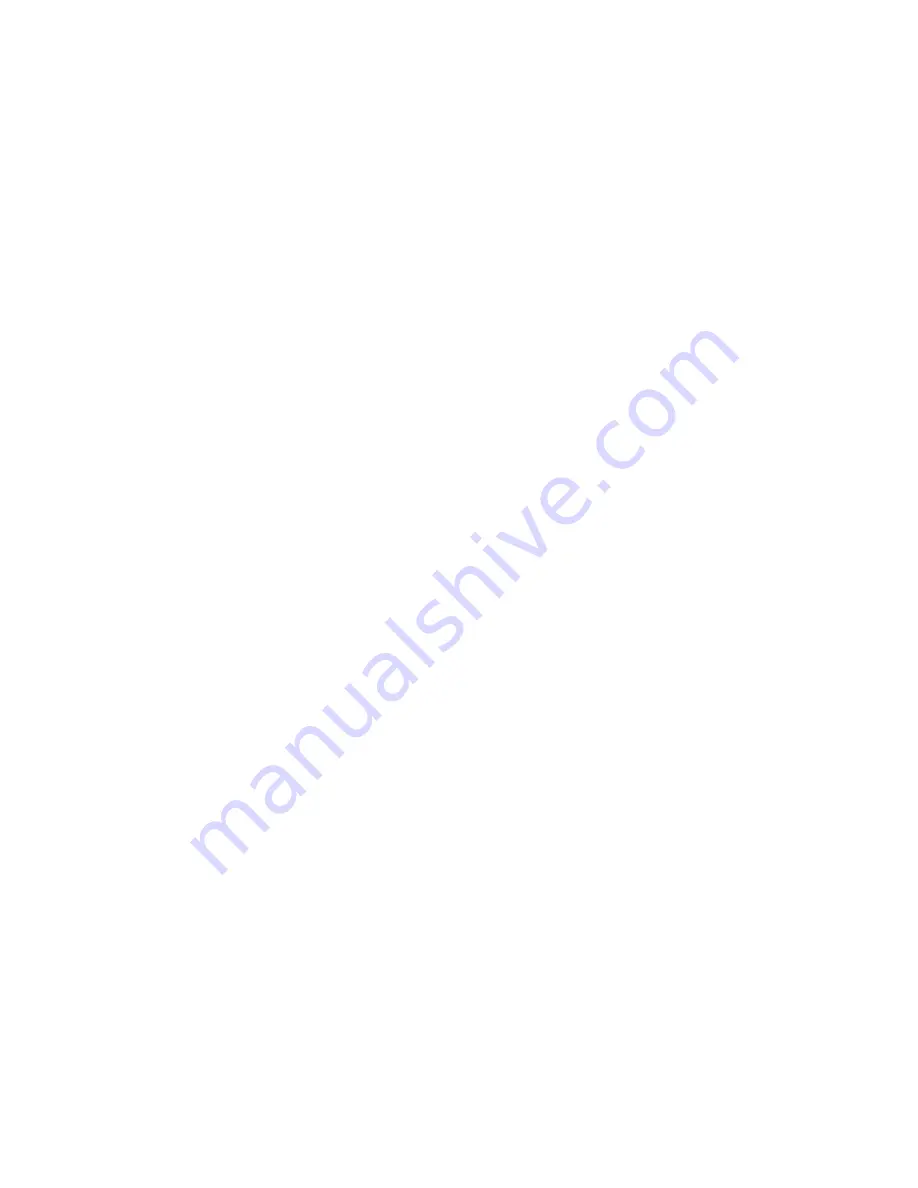
2
Copyright © 2018 by Delta Separations LLC
®
All rights reserved. No portion of this book may be reproduced in any form without
permission from Delta Separations, except as permitted by U.S. copyright law.
For permission contact: [email protected]
Printed in the United States of America
System GEN 2.0; Manual V2, May 2018