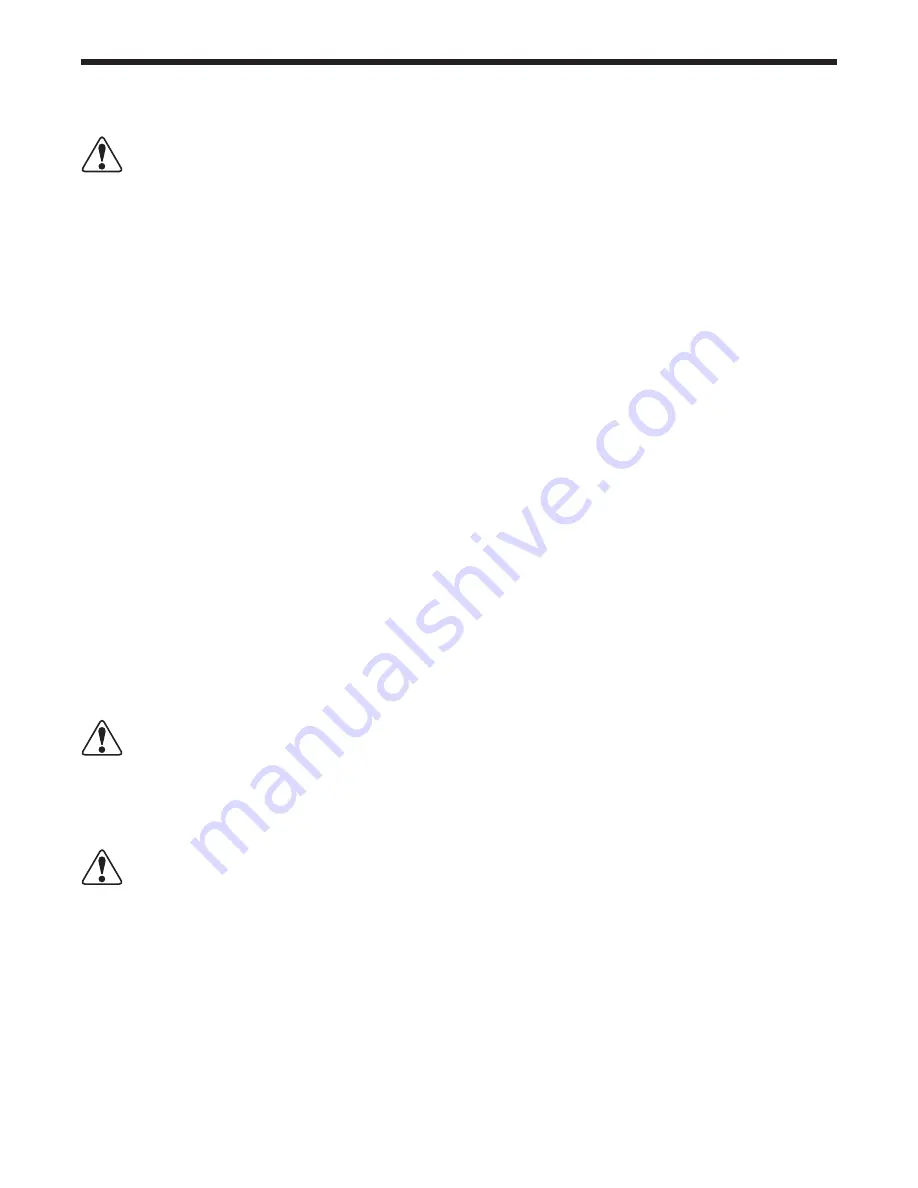
2
Delfield
IMPORTANT WARNINGS AND SAFETY INFORMATION
WARNING
ANY REFRIGERATION SERVICE PROCEDURES DESCRIBED IN THIS MANUAL MUST BE PERFORMED
BY A CERTIFIED EPA TECHNICIAN.
Read this manual thoroughly before installing, operating, or performing maintenance on the equipment.
FAILURE TO FOLLOW INSTRUCTIONS IN THIS MANUAL CAN CAUSE PROPERTY DAMAGE, INJURY OR DEATH.
•
Do not store or use gasoline or other flammable vapors or liquids in the vicinity of this or any other appliance.
•
Unless all covers and access panels are in place and properly secured, do not operate this equipment.
•
Damp or wet hands may stick to cold surfaces.
•
Allow heated equipment to cool down before attempting to clean or service.
•
Read and understand instruction manuals and labels. Learn all applications and restrictions for the
service performed.
•
Do not remove ground prong from service equipment cords.
•
Use extension cords rated for the intended service and as short in length as possible.
•
Use refrigerant hoses SAE J196-1992 approved with a shutoff device within 12 inches of the ends.
•
Make sure recovery tanks are DOT approved for use with the type of refrigerant being serviced.
•
Service units only in well ventilated areas using mechanical ventilation systems.
•
Follow all accessory advisories and instructions.
•
Do not operate any unit with defective or damaged parts.
WARNING
Serious injury or death can occur from inhaling high concentrations of refrigerant vapors. These vapors also
reduce oxygen levels in confined areas. Contact with liquid can cause frostbite. All containers, equipment and
hoses are under high pressure. Do not puncture or damage these components.
CAUTION
Observe the following:
• Keep the equipment area free and clear of combustible material.
• Maintain adequate clearance for air openings.
• Operate equipment only on the type of electricity indicated on the data plate.
• Unplug the unit before making any repairs.
• Handle all refrigerant hoses, recovery tanks, lines and other vessels as containers under pressure at all times.
• Retain this manual for future reference.