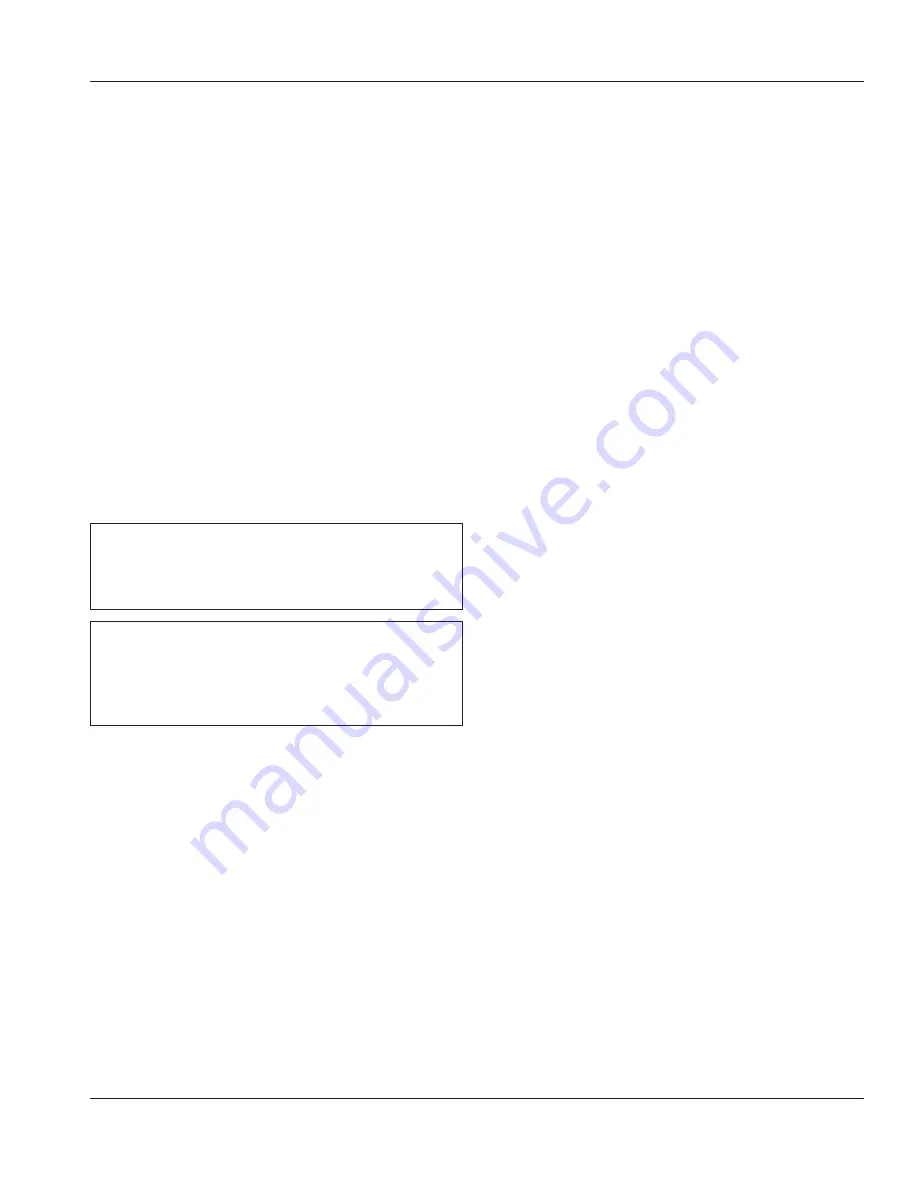
Section 5
Maintenance
Part Number: 9291544 07/20 23
INTERIOR CLEANING
The interior can be cleaned using soap and warm water. If
this isn’t sufficient, try ammonia and water or a nonabrasive
liquid cleaner.
Door gaskets require regular cleaning to prevent mold
and mildew build up and also to retain the elasticity of the
gasket. Clean them with water and mild soap (not citrus
based). Avoid full strength cleaning products on gaskets as
this can cause them to become brittle and crack. Never use
sharp tools or knives to scrape or clean the gasket. Gaskets
can be easily replaced and do not require the use of tools
or an authorized service person. The gaskets are Dart style
and can be pulled out of the groove in the door. Place
gasket in warm water to make the material more pliable for
installation. Dry and press into place.
Preventing Blower Coil Corrosion
To help prevent corrosion of the blower coil, store all acidic
items, such as pickles and tomatoes, in seal-able containers.
Immediately wipe up all spills.
EXTERIOR CLEANING
n
Warning
When cleaning the unit, care should be taken to avoid
the front power switch and the rear power cord. Keep
water and/or cleaning solutions away from these parts.
,
Caution
Never use an acid based cleaning solution! Many food
products have an acidic content, which can deteriorate
the finish. Be sure to clean the stainless steel surfaces of
ALL food products.
Clean the area around the unit as often as necessary to
maintain cleanliness and efficient operation.
Wipe casters with a damp cloth to prevent corrosion.
Wipe surfaces with a damp cloth rinsed in water to remove
dust and dirt from the unit. Always rub with the “grain” of
the stainless steel to avoid marring the finish. If a greasy
residue persists, use a damp cloth rinsed in a mild dish soap
and water solution. Wipe dry with a clean, soft cloth.
Never use steel wool or abrasive pads for cleaning. Never
use chlorinated, citrus based or abrasive cleaners.
Stainless steel has a clear coating that is stain resistant and
easy to clean. Products containing abrasives will damage
the coating and scratch the panels. Daily cleaning may be
followed by an application of stainless steel cleaner which
will eliminate water spotting and fingerprints. Early signs of
stainless steel breakdown are small pits and cracks. If this
has begun, clean thoroughly and start to apply stainless
steel cleaners in attempt to restore the steel.
Fiberglass can be polished to eliminate water spotting,
fingerprints and bring out the color of the fiberglass. To
maintain the rich, brilliant color of the fiberglass and to
remove shallow surface scratches, wax twice a year. This can
be done in the same manner in which a car is waxed.
Counter Protector Glass & Hardware Cleaning
Routine cleaning can be done with soap and water. Extreme
stains or grease should be cleaned with a nonabrasive
cleaner and plastic scrub pad. Polish the chrome when
necessary with a soft cotton cloth.
Defrosting
Refrigerated cold pans should be defrosted daily. Never
use sharp objects or tools to clean or scrape ice/frost build
up from the refrigerated cold pans. A puncture to the pan
could cause irreparable damage to the refrigeration system.
Units with a Eutectic Fluid Cold Pan require the same
precautions. The fluid is NOT refillable and loss of fluid due
to a puncture would cause irreparable damage.
CLEANING THE CONDENSER COIL
In order to maintain proper refrigeration performance, the
condenser fins must be cleaned of dust, dirt and grease
regularly. It is recommended that this be done monthly. If
conditions are such that the condenser is totally blocked
in a month, the frequency of cleaning should be increased.
Clean the condenser with a vacuum cleaner or stiff brush. If
extremely dirty, a commercially available condenser cleaner
may be required.
Failure to maintain a clean condenser coil can initially cause
high temperatures and excessive run times. Continuous
operation with a dirty or clogged condenser coil can
result in compressor failure. Neglecting the condenser coil
cleaning procedures will void any warranties associated
with the compressor and cost to replace the compressor.
DRAIN MAINTENANCE
Each refrigerated unit has a drain located inside the unit
that removes the condensation from the evaporator coil
and routes it to an external condensate evaporator pan.
Each drain can become loose or disconnected during
normal use. If you notice water accumulation under the
unit, be sure the drain tube is connected to the evaporator
drain pan and the end of the drain tube is in the condensate
evaporator. The leveling of the unit is important as the units
are designed to drain properly when level. Be sure all drain
lines are free of obstructions.
Summary of Contents for Shelleyglas KFW-1-NU
Page 3: ...Table of Contents continued Part Number 9291544 07 20 3 THIS PAGE INTENTIONALLY LEFT BLANK...
Page 16: ...Installation Section 3 16 Part Number 9291544 07 20 THIS PAGE INTENTIONALLY LEFT BLANK...
Page 21: ...Section 4 Operation Part Number 9291544 07 20 21 THIS PAGE INTENTIONALLY LEFT BLANK...