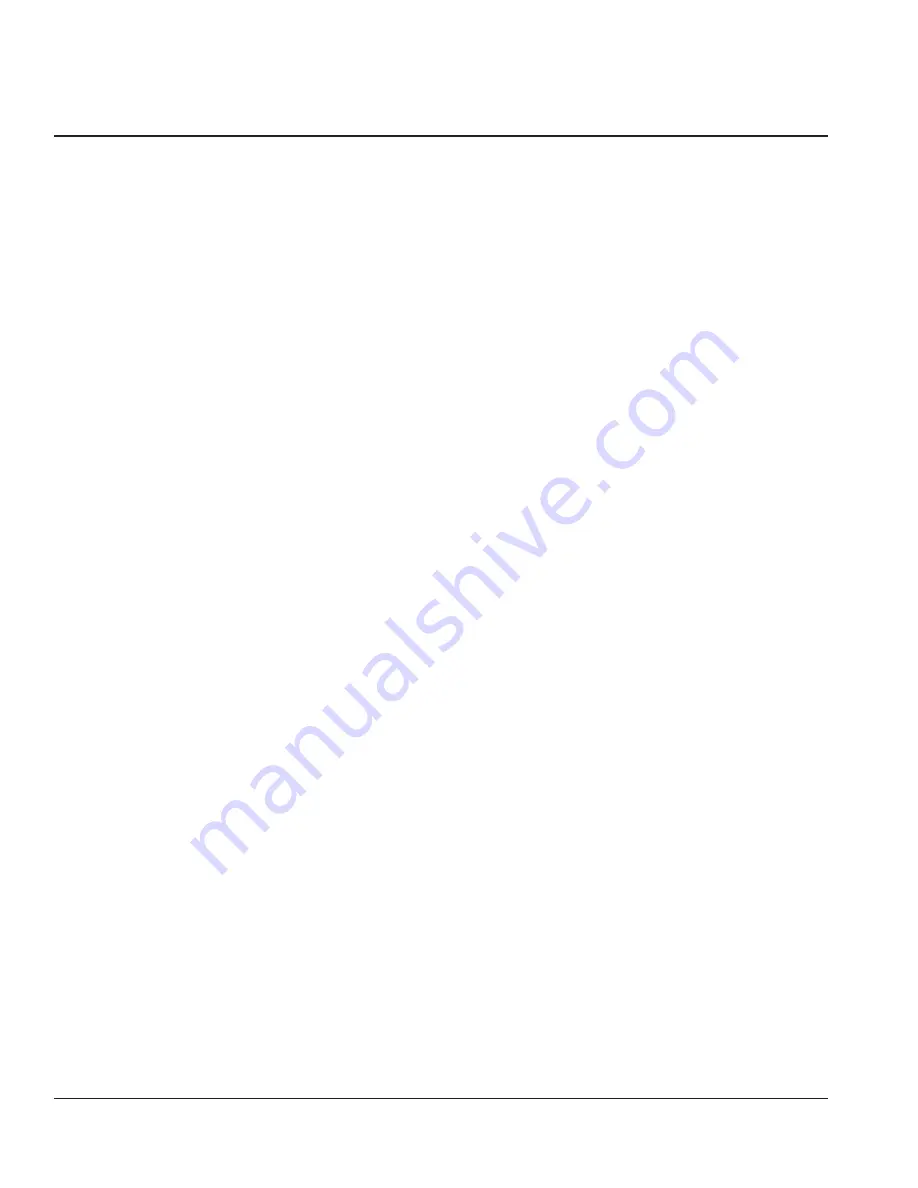
4
Part Number: 9291000 06/22
Section 1
General Information
Model Numbers ..................................................................................................................6
Serial Number Location .....................................................................................................6
Warranty Information ........................................................................................................6
Regulatory Certifications ..................................................................................................6
Section 2
Specifications
General Specifications .......................................................................................................7
Dimensions .........................................................................................................................8
Maximum Load .................................................................................................................10
Section 3
Installation
Location ............................................................................................................................12
Leveling .............................................................................................................................13
Stabilizing .........................................................................................................................13
Leg & Caster Installation ..................................................................................................13
Air Flow .............................................................................................................................13
Installation Procedure .....................................................................................................13
Section 4
Operation
Display Layout ..................................................................................................................19
On/OFF ..............................................................................................................................20
Compressor Preheating ...................................................................................................20
Date and Time ...................................................................................................................20
Blast Chilling Cycles .........................................................................................................20
General Operation Principles .......................................................................................................... 20
Chilling Time ......................................................................................................................................... 20
Temerature Chilling ............................................................................................................................ 20
Chilling and Storage Status Symbols ........................................................................................... 20
Chilling Phases ..................................................................................................................................... 20
Selecting and Starting the Positive Chilling Cycle .................................................................. 21
Selecting and Starting the Negative Chilling Cycle ................................................................ 21
Defrost Mode ...................................................................................................................22
Drying with Machine at Standstill ..................................................................................22
Door Opening ...................................................................................................................22
Ozonator (Optional) .........................................................................................................23
Ice-Cream Cycle ................................................................................................................23
Thawing Cycle ...................................................................................................................23
Chilling Program Storage ................................................................................................23
Chilling Program Execution .............................................................................................24
Maintenance
Schedule ...........................................................................................................................26
Exterior Cleaning..............................................................................................................26
Ordinary Maintenance .....................................................................................................26
Operations Only for Authorized Installer .......................................................................26
Table of Contents
Summary of Contents for CV10E
Page 3: ...THIS PAGE INTENTIONALLY LEFT BLANK Part Number 9291000 06 22 3 ...
Page 11: ...THIS PAGE INTENTIONALLY LEFT BLANK Section 2 Specifications Part Number 929100 06 22 11 ...
Page 17: ...Section 3 Installation Part Number 9291000 06 22 17 THIS PAGE INTENTIONALLY LEFT BLANK ...
Page 25: ...Section 4 Operation Part Number 9291000 06 22 25 THIS PAGE INTENTIONALLY LEFT BLANK ...
Page 39: ...Section 6 Trouble shooting Part Number 9291000 06 22 39 ...