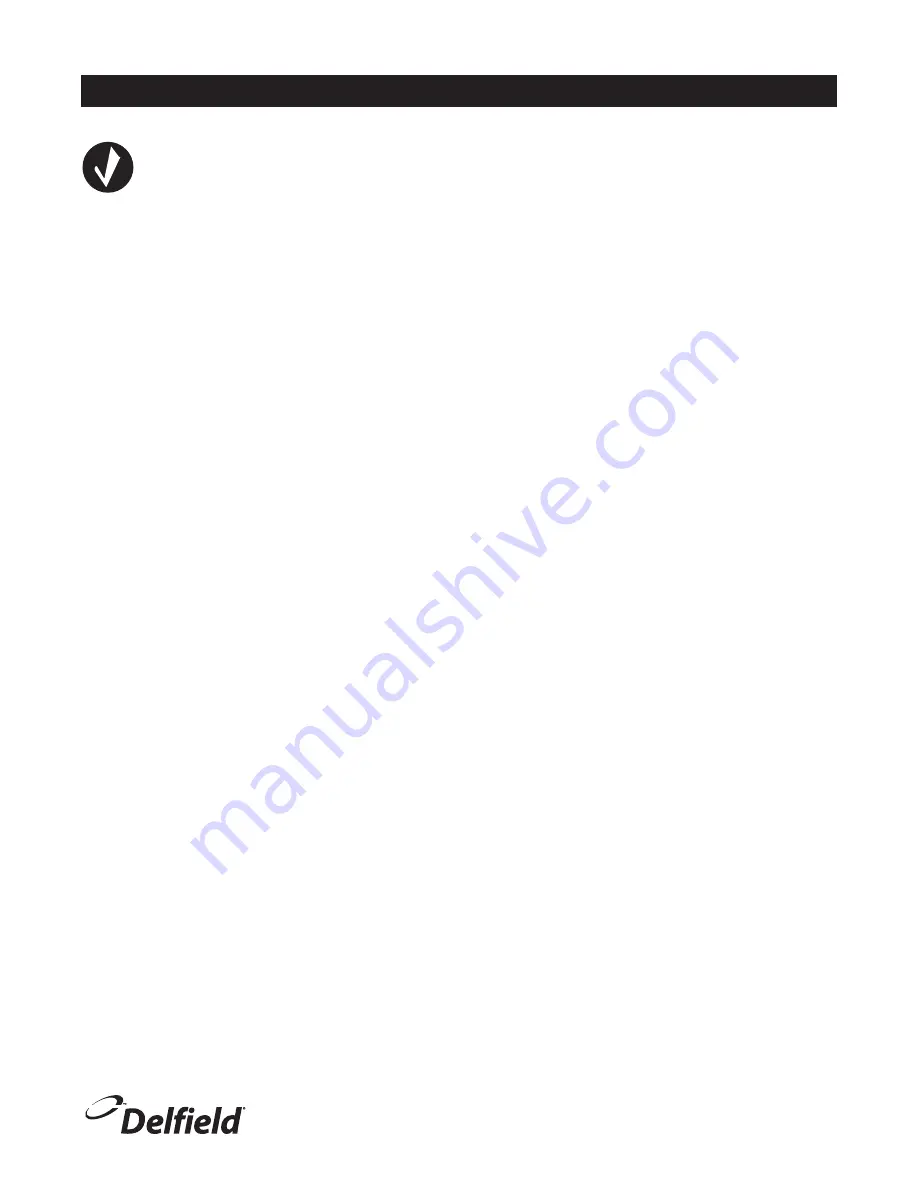
Concepts Installation Manual
5
For customer service, call (800) 733-8829, (800) 773-8821, Fax (989) 773-3210, www.delfield.com
Tools And Supplies Required
The following tools are either required or will make the installation
easier:
1) A scissor jack to lift and hold heavy units off the floor so that legs can be
adjusted, allowing the proper leveling of the units.
2) A level is needed to assist in the leveling of each unit from front to back and
left to right. A 2’ (61cm) level is a must; a 4’ (122cm) level is also desirable.
3) Two 6’ (183cm) pipe clamps are useful in pulling equipment tightly together
while fasteners are installed. This results in a better spline.
4) Vise grips will hold backsplash bars together as they are being bolted together.
5) A steel hammer and a block of wood can be used to make minor alterations of
the stainless steel along the seam between two units, in order to perfect the
seam. This is used after the units are splined.
6) A rubber mallet.
7) A socket set.
8) Phillips, hex head and straight blade screwdrivers.
9) 7/16” (1.1cm), 9/16” (1.4cm) and 1/2” (1.3cm) open end wrenches.
10) Silicone sealant; Dow Corning #732 is ideal.
11) Drill motor.
12) Electrical test meter.
13) 5/16 nut driver to remove shipping braces.
14) Adjustable wrench for leg adjustments.