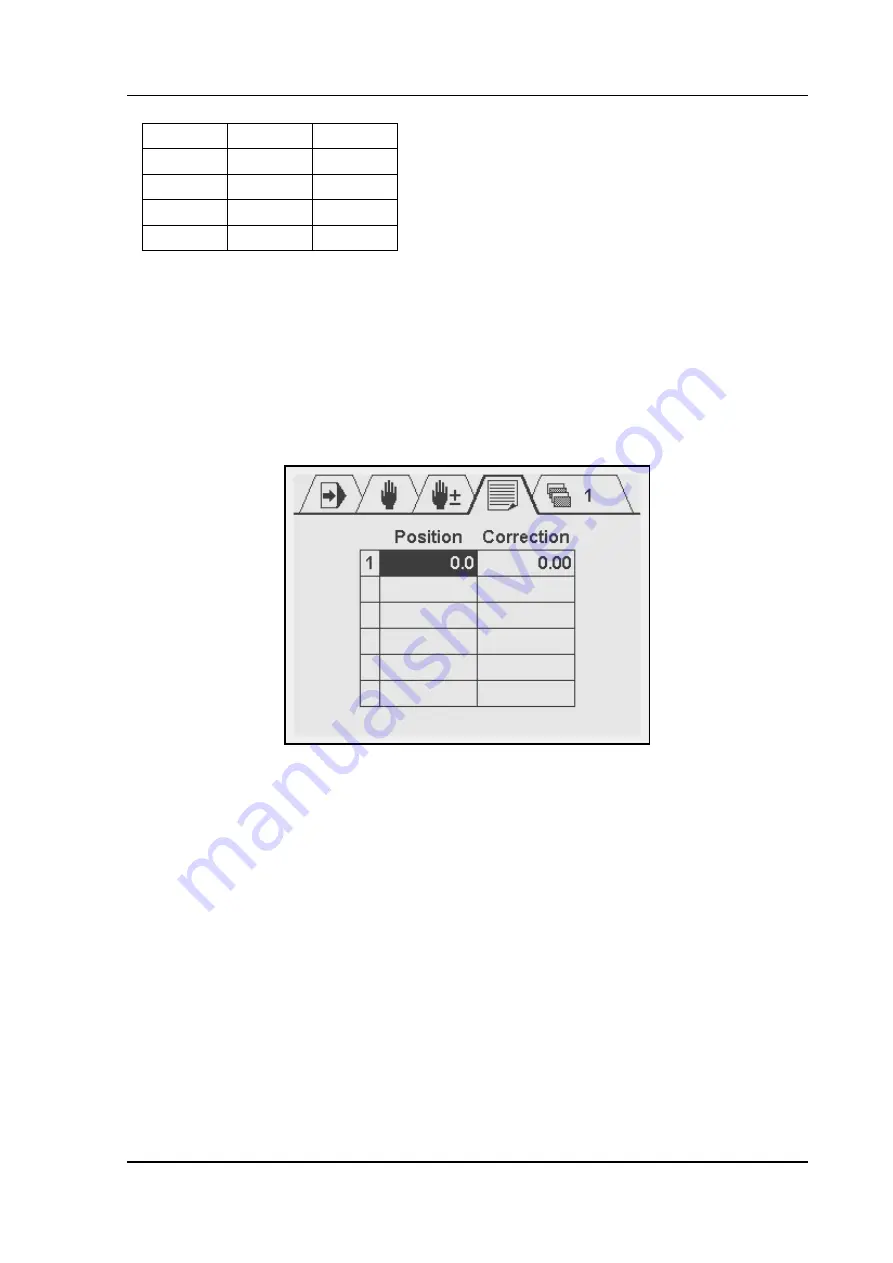
Delem
V0208, 2.7
All measured axis positions and their corresponding corrections can be entered in a table on
the control.
To access the correction table, proceed as follows:
•
enter the machine parameters menu as described in chapter 1,
•
enter the parameters for the backgauge,
•
scroll to parameter 29, ‘Spindle correction table’,
•
press ENTER.
The following screen appears:
Each line consists of the line number, the axis position (Pos) and the necessary correction
(Cor).
The table can be edited as follows:
•
Use the arrow keys to move up, down, left and right.
•
To add a row, go to the first column and press the ENTER key.
•
To delete a row, go to the first column of the previous row and press the Clear key. All
rows after the current row will be deleted!
•
To enter a value, move to the required cell, type the value and press ENTER.
A maximum of 20 corrections can be programmed in the table.
For positions between the programmed positions, a correction computed through linear
interpolation.
Xm
P
Cor
X1
P1
Cor1
X2
P2
Cor2
...
...
...
Xn
Pn
Cor n
Summary of Contents for DAC-360
Page 1: ...Delem Manual version V0208 DAC 360 Installation manual Version 1...
Page 4: ...V0208 0 4 1 3 Test functions 3 3 1 4 Service screens 3 3...
Page 6: ...V0407 0 6...
Page 17: ......
Page 18: ......
Page 76: ...V0208 2 50...
Page 82: ...V0407 3 6...