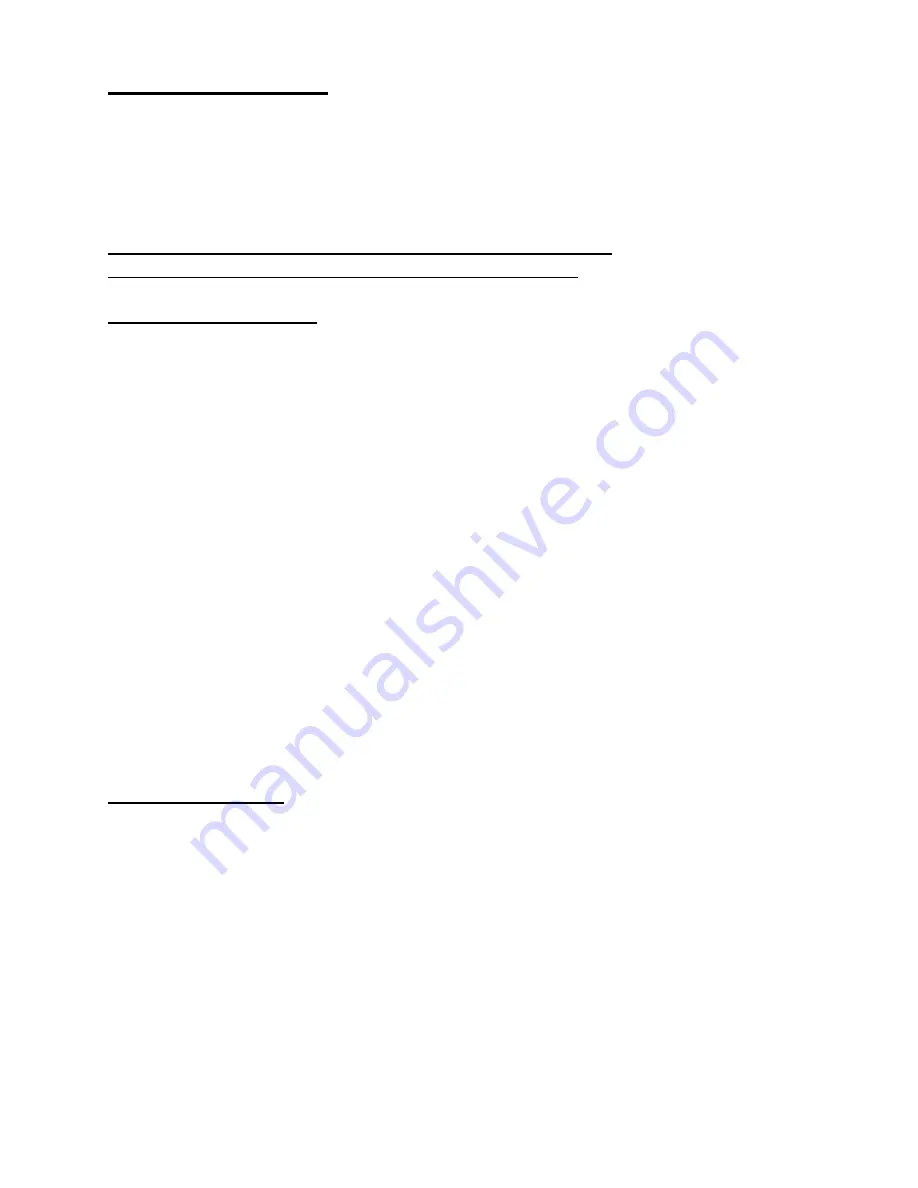
TROUBLE-SHOOTING
Following is a basic trouble-shooting guide. We recommended that you consult your local dealer for
service. Each
Vmax
system is tested and checked at the factory. Always indicate system model and serial
number when calling.
WARNING: Before attempting any repairs, disconnect all power from the system by switching off
the main breaker or disconnect switch. This will prevent the system from automatically starting
from a vacuum switch.
TROUBLE SHOOTING FAQS (Frequently Asked Questions)
VMAX OIL-SEALED LIQUID RING VACUUM PUMP SYSTEMS
START-STOP PROBLEMS:
System will not start in HAND or AUTO position:
(Vmax)
1. Check if the disconnect or circuit breaker is switched on.
2. Check the overload setting on the starter and fuses.
3. Check alarm reset, light should be off.
4. Ensure that the proper voltage is supplied and that the wire size is correct.
5. Check electrical control panel (if installed). Make sure that all wires are tight. Wires may vibrate loose during shipment or
operation.
6. Check low oil level switch (if installed). Add oil to reservoir if needed.
7. Check if the pump has seized by rotating the coupling by hand (
disconnect power first
). If a rubbing noise or
binding is observed, contact authorized dealer.
8. Check the high temperature switch, which should be set for 225
o
F.
9. Check if pump operates against high back-pressure (> 4 psig), if so replace oil separator element.
10. Check vacuum switch (if installed).
System shuts down while running:
(Vmax)
1. Check oil temperature gauge for operating temperature.
2. Check the overload setting on the starter and fuses.
3. Ensure that the proper voltage is supplied and that the wire size is correct.
4. Check for loose electrical connections.
5. Check the vacuum switch setting (if installed).
6. Check low oil level switch (if installed), add oil to reservoir if needed.
7. Check if the pump has seized by rotating the coupling by hand (
disconnect power first
). If a rubbing noise or
binding is observed, contact authorized dealer.
8. Check high temperature switch, which should be set for 225
o
F.
9. Clean oil strainer.
10. Check if pump operates against high back-pressure (> 4 psig), if so replace oil separator element.
11. Check the overload setting on the starter and fuses.
VACUUM PROBLEMS:
System operates, but does not achieve desired vacuum level:
(Vmax)
1. Stop system and disconnect power.
2. Check if the inlet valve is open and inlet filter is clean.
3. Ensure that no lines are open to the atmosphere, causing loss of vacuum.
4. Check for leaks in piping systems, using conventional leak detection methods.
5. Ensure that the oil level is correct and that the pump is primed and filled with oil to the shaft centerline only.
6. Check if the oil isolation valve is open.
7. Check if the oil solenoid valve (if installed) is working.
8. Check the vacuum switch setting (if installed).
9. Check setting of vacuum relief valve (if installed) and adjust as needed.
10. Check if the motor rotation is correct. Rotation should be clockwise (facing pump from motor side) and marked by
an arrow on the motor or pump housing. If incorrect, switch any two of the three main power leads on the
contactor inside the control panel.
Dekker Vacuum Technologies, Inc. – Vmax/13
20