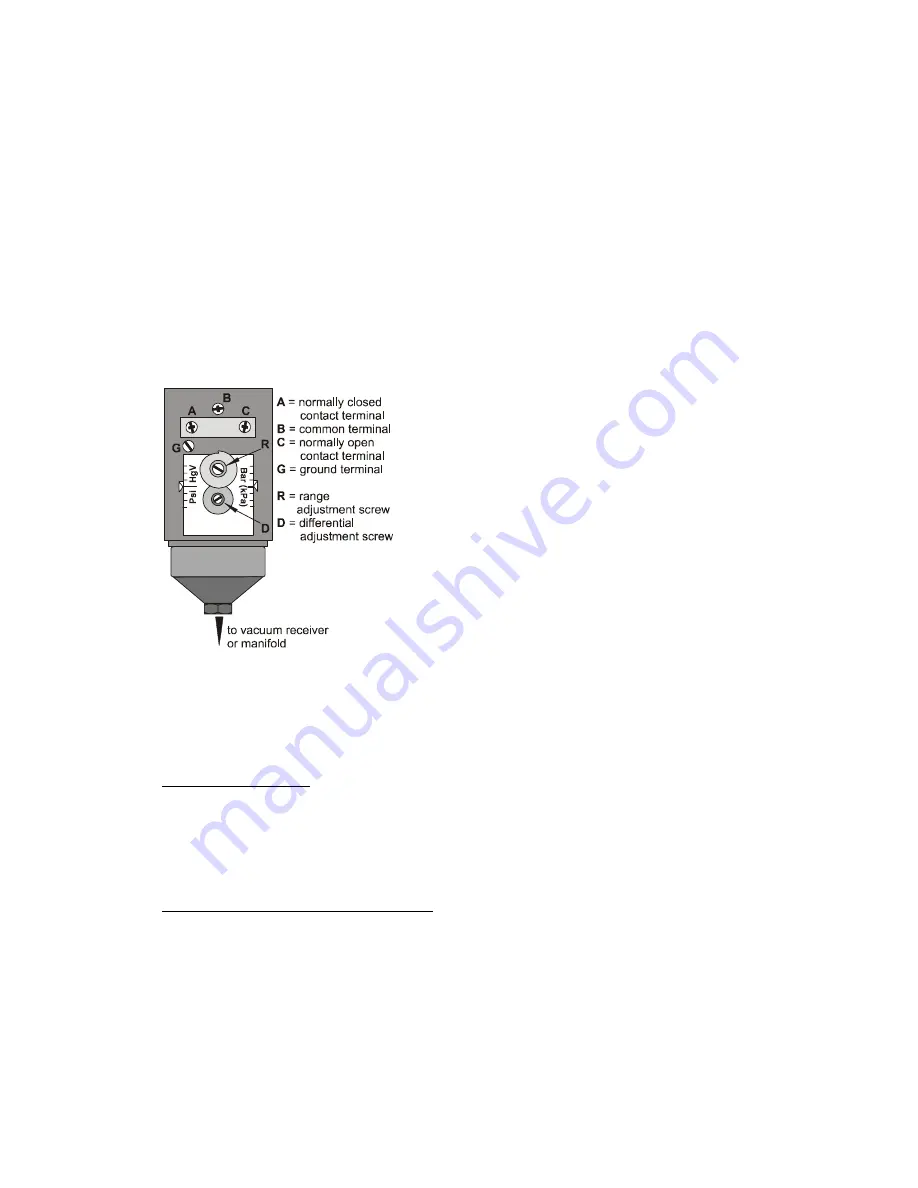
♦
Vibration Isolators (optional):
are used to eliminate vibrations, noise and shock transmission from
machinery to the floor. Floor-mount type vibration isolators are used for
Vmax
vacuum pump systems.
The vibration isolators have a steel top plate, threaded insert and steel base, both totally imbedded in
an oil-resistant neoprene. The isolators bolt onto a tank or base-frame with one bolt and have two
mounting bolts to mount to the foundation or floor.
♦
System Isolation Valve (optional):
may be installed on the vacuum receiver tank or vacuum pump
manifold. Usually the valve is used to isolate the vacuum system from the piping network.
♦
Inlet Filter (optional):
An inlet filter may be installed on the
Vmax
oil-sealed vacuum pump systems
to prevent carry-over of particles into the pump.
♦
Vacuum Relief Valve (optional):
This valve may be installed on the pump suction manifold or on the
receiver. The vacuum relief valve is used to protect the vacuum pump from closed suction which can
damage the pump.
♦
Vacuum Switch (optional):
is used to automatically switch the vacuum pump ON and OFF, based on
demand. This switch is standard on all multiplex systems.
Switches are factory preset for your application and it is NOT RECOMMENDED to adjust the
vacuum switch.
Each switch is labeled as LEAD or LAG and is marked with the corresponding PUMP
ON and PUMP OFF points.
If the vacuum switch must be adjusted, please follow these instructions:
1. To increase the point at which the vacuum pump turns
ON, turn the RANGE ADJUSTMENT SCREW (R) counter-
clockwise. See the range scale on switch for
approximation. Use vacuum gauge to observe actual
PUMP ON and PUMP OFF point.
2. To increase the differential, which is the difference between
the PUMP ON and PUMP OFF point, turn the
DIFFERENTIAL ADJUSTMENT SCREW (D) counter-
clockwise. To obtain the correct PUMP OFF point observe
the physical opening of the contact switch as compared to
the vacuum gauge reading. The vacuum pump will not stop
running, because all systems are equipped with “10 minute
mimum run” timers.
3. Remember you will need to vary the vacuum level in the
receiver or manifold to see a change in the vacuum level,
and to adjust the switches.
♦
Microprocessing Controller (optional):
system may be equipped with this very reliable and compact
Controller module for controlling and monitoring basic machinery functions. The following instructions
should help guide the end user to perform simple changes to the Controllers’ pre-programmed
settings. The specific preset areas that may be modified are outlined below.
Set the Internal Clock:
Upon powering the system control panel, the installation technician must ensure that the internal clock
in the Controller has been set to the current military time setting. The Controller is equipped with an
internal capacitor that will hold the time for approximately 80 hrs. If your system has not been installed
within the allotted time frame, the alternation of the automatic mode will not occur and only one of the
pumps will function until the time parameter has been updated. Refer to the following instructions for
access to and changing of the parameters.
Sequence of Operation Automatic Mode:
The switch on the front of the system control panel must be placed in the automatic mode before the
Controller program will initiate. Upon starting the system, all pumps should come on line and run for a
minimum of 10 minutes each. As the demand for the vacuum pumps change, the individual units will
turn off and on as required, each time running for a minimum of 10 minutes after initial start. If all the
individual pumps are not placed in automatic mode simultaneously, there may be a pump that does
not ramp up to speed with the lead pump. This does not mean that there is a problem with your
vacuum system. The reason for this can be the switch settings for lead and lag pumps. When the
system is started and individual units are placed in automatic mode at different times, the demand for
lag pump may not be present due to the time lapse between placing the various pumps in automatic
mode.
Dekker Vacuum Technologies, Inc. – Vmax/13
16