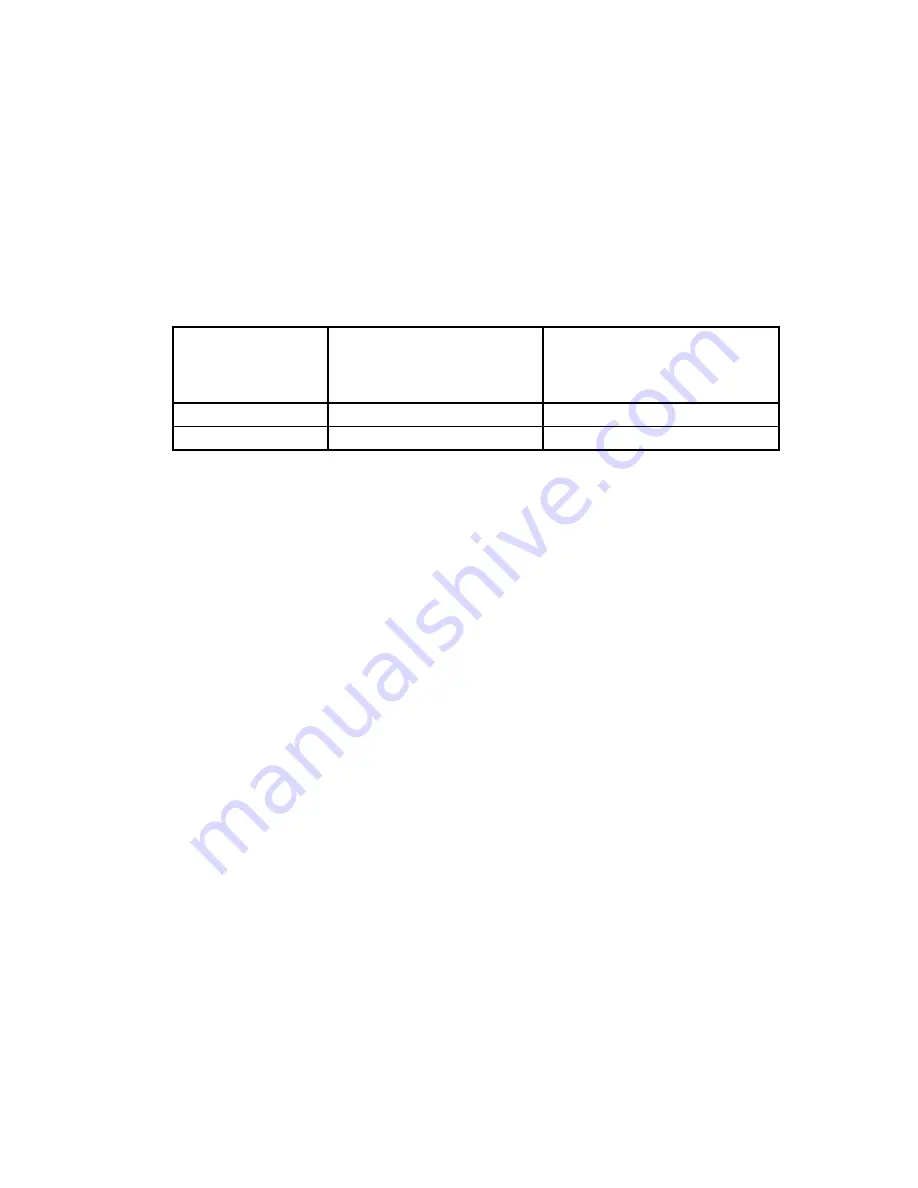
Inlet Filter (if installed)
Check after first 8 hours of operation. Clean or replace inlet filter element every 1000 to 3000 hours
depending on application or if excessive pressure drop is noticed. In some applications it may be
necessary to clean inlet filter more often.
CAUTION: Be careful not to allow accumulated foreign material to fall in the pump suction opening
when removing the filter cartridge. Horizontal filter installation is recommended to prevent this.
Filters must be disposed of properly as they might contain toxic substances carried over from the
process.
Seal Fluid
The system(s) are shipped with our especially formulated
Vmaxol
seal fluid. These fluids are specifically
designed for use in our
Vmax
systems, providing low viscosity, excellent water separating qualities, anti-
foaming and low oxidation. We recommend that our
Vmaxol
sealing fluids be used for obtaining ultimate
performance from your
Vmax
vacuum pump system and to guarantee the extended 3-year warranty period.
Container
Size
Standard
Vmaxol
(10,000 hours of operation)
Synthetic/Food grade
Long-life Vmaxol
(15,000 hours of operation)
5 Gallon Container
5220-0050-000
5220-0050-001
55 Gallon Drum
5220-0550-000
5220-0550-001
Material Safety Data Sheets available upon request
When using
Standard Vmaxo
l it is recommended that the seal fluid be changed every 10,000 hours of
operation or once a year, whichever comes first. When using
Synthetic/Food grade Long-life Vmaxol
,
seal fluid may be changed every 15,000 hours of operation or once a year, whichever comes first. Extreme
operating conditions may require more frequent changes.
To change the fluid, first make sure there is no power to the system and the pump is off. Drain the fluid
reservoir, vacuum pump and heat exchanger using the drain valves. We recommend that the fluid be
changed when the system is at operating temperature.
When charging the system with new fluid, make sure that the pump is filled with oil to the shaft centerline
level.
Do not fill
the pump above the shaft centerline
. Starting the pump with oil level above the shaft
centerline may result in shaft or impeller damage or failure. You can add oil by removing the suction or
discharge flange and pouring oil through pump suction or discharge port.
Fill the reservoir to the FILL LINE on the sight gauge. Open the air bleed valve on the heat exchanger to
remove all air from the system. Run the pump for a few minutes, stop and check fluid level again. If
required, add additional fluid to the reservoir.
Be sure not to overfill.
Check seal fluid level in the reservoir. A high fluid level could mean a build-up of water in the reservoir,
which should be drained. Check every 500 hours.
Devarnishing
The operating life of the unit is greatly enhanced based on the quality of the seal fluid. Oxidized or
darkened seal fluid is a sign of trouble. Plugged filters reduce performance and may damage pump.
Periodic maintenance will offer the best protection for your equipment.
DEKKER offers a specially formulated devarnishing compound
Proclean 39V
for oil-sealed liquidring
pumps and systems. Procedure for using Proclean 39V and MSDS sheet are included with the product.
The compound is available in the following quantities:
Proclean 39V (part no.: 5230-0010-000) – 1 gallon
Proclean 39V (part no.: 5230-0050-000) – 5 gallon
Proclean 39V (part no.: 5230-0055-000) – 55 gallon
NOTE: Varnished pumps are not covered under warranty.
Seal Fluid Strainer
After the first 50 hours of operation, clean the strainer in the seal fluid line. This is done to remove any
debris carried over into the system from the process. Clean and inspect the strainer every 1000-3000
hours depending on application or if excessive oil discharge temperature (above 185°F) is indicated. An
increase in pump discharge oil temperature is an indication of low oil flow and normally is an indication of
Dekker Vacuum Technologies, Inc. – Vmax/13
13