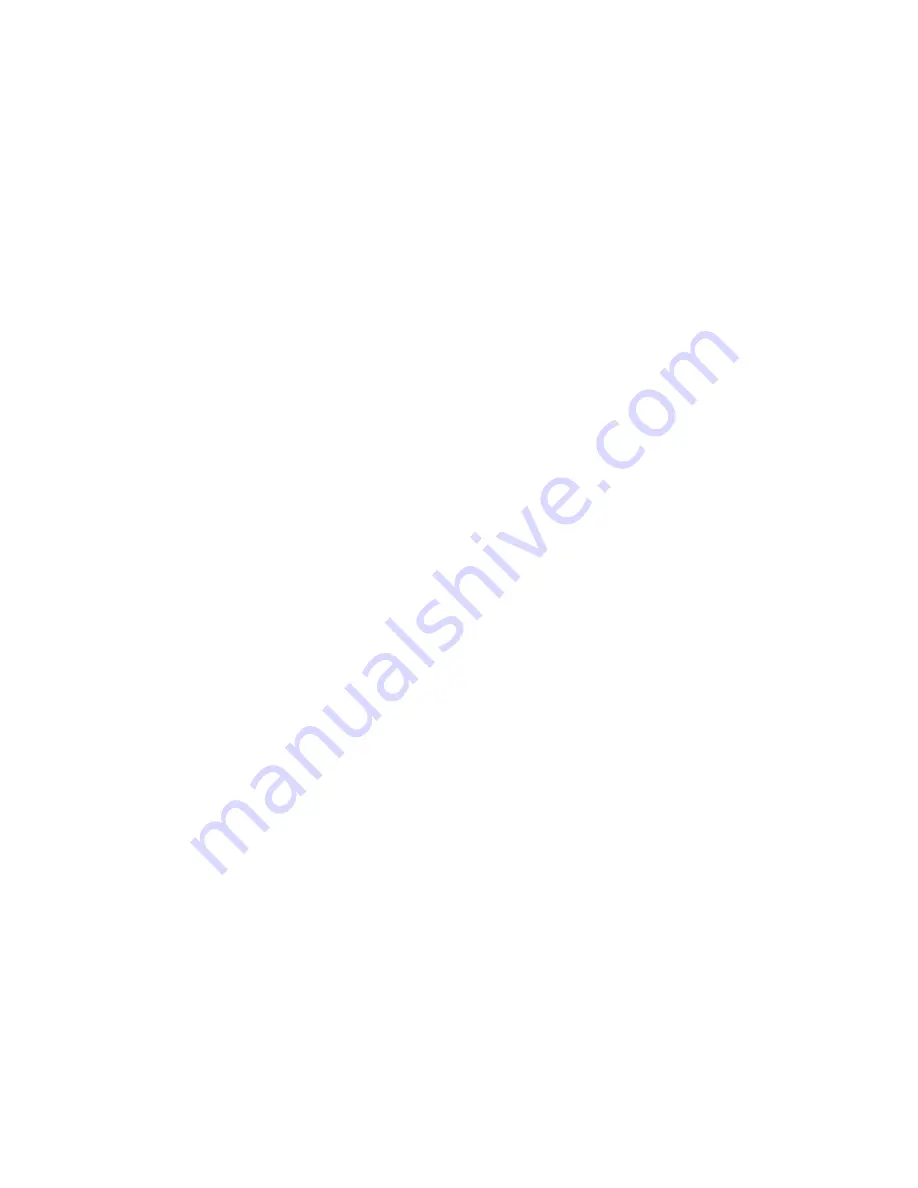
51
9 Shutdown, Storage and Disposal
9.1 Shutdown
After disconnection of the media supply lines, pay attention that no leaks occur that could result in
hazards for persons and/or the environment!
Dispose of process media, cleansing agents and replaced parts in a safe and environmentally friendly
manner! Observe the manufacturers' instructions for hazardous substances!
Observe the following points:
1.
All electrical components must be completely disconnected from the power supply and discharged
before removal.
2.
Disconnect hydraulic and pneumatic equipment completely from the power supply and relieve
pressurised systems!
3.
The removal of springs or parts under mechanical load should be performed with particular care so
that the mechanical energy stored in these parts does not result in injuries.
4.
Batteries and rechargeable batteries that may be used in the installation must be disposed of
separately in accordance with the local waste disposal regulations.
5.
Furthermore, the information on outsourced parts indicated in the annexed suppliers'
documentation must also be observed.
9.2 Storage Conditions
Store the machine in such a way that damage is avoided
.
Store the machine together with all the individual parts, as otherwise important parts might be missing
when the machine is put into operation again
.
Storage
Pay attention to the following points for the storage of the machine
:
Protect parts susceptible to corrosion (bare metal)
Summary of Contents for MDE Series
Page 1: ...INSTALLATION MANUAL MDE SERIES INDEX DRIVES MODELS MDE600M MDE700M MDE900M ...
Page 6: ...5 There are no elementary protection devices at the man machine interface ...
Page 16: ...15 4 4 Design and Components of the Machine Front and Top View A ...
Page 17: ...16 Section and Side View ...
Page 54: ...53 10 ANNEX Declaration of Incorporation ...
Page 55: ...54 NORD DRIVESYSTEMS ...
Page 56: ...55 ...
Page 57: ...56 SEW EURODRIVE ...
Page 58: ...57 TL6615 EXTRACTION TOOL PAGE 1 OF 2 ...