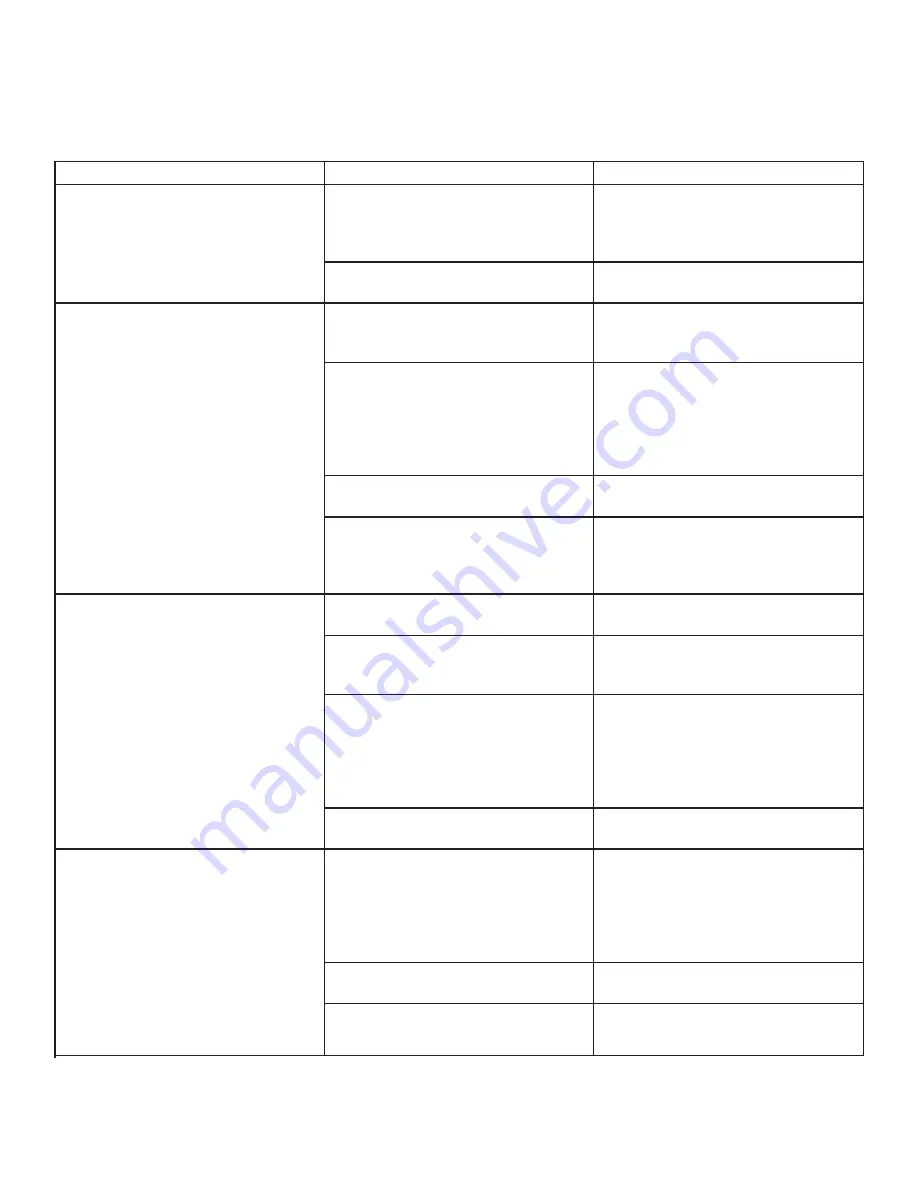
32
PROBLEM
POSSIBLE CAUSE
CORRECTION
Ice cubes are too small (less than 1/2 inch
thick).
7. Leaking drain valve
See “Cleaning Your Ice Maker” section for
cleaning the unit. This will also dissolve
and flush out foreign material in the
drain valve causing it to leak.
8. Room temperature is too cold.
Move to an area where temperature is
above 55 degrees F.
Ice cubes are too big (greater than 3/4
inch thick).
1. Ice slab not releasing.
See “Cleaning Your Ice Maker” section for
cleaning the unit for proper operation
and cube size.
2. Condenser fan air flow is restricted.
Make certain the grill in the front of the
unit is free and open for proper air circu-
lation. Check and clean the condenser
coil by removing the grill in the front of
the unit. Clean the condenser with a
vacuum and brush attachment.
3. Room temperature is too warm.
Move to an area where temperature is
below 90 degrees F.
4. Evaporator thermistor does not have
sufficient contact with evaporator or out-
of-range.
Check to see that the evaporator therm-
istor is secured properly to the evapora-
tor. If secured, check resistance with
Table C in Section 5.2, Thermistors.
Hollow ice slab.
1. Distributor tube is restricted.
See “Cleaning Your Ice Maker” section for
cleaning the unit for proper operation.
2. Build-up of deposits on evaporator
plate.
See “Cleaning Your Ice Maker” section for
cleaning the unit for proper operation
and cube size.
3. Low water level in reservoir.
Make sure that the reservoir drain plug
is installed properly. Check the water
line to the unit to make sure there are no
restrictions or kinks in the line. Check all
filters to make sure they are not restrict-
ed or plugged.
4. Leak in the sealed system.
Check for any leaks. If leak found, repair,
evacuate, and re-charge unit.
Ice is not clear.
1. Low water level in reservoir.
Make sure that the reservoir drain plug
is installed properly. Check the water
line to the unit to make sure there are no
restrictions or kinks in the line. Check all
filters to make sure they are not restrict-
ed or plugged.
2. Softened water supply.
Make certain the water line is not con-
nected to the water softener.
3. Room temperature is too cold.
Move the unit to an area where room
temperature is above 55 degrees F.
TrOuBLESHOOTING GuIdE
Summary of Contents for RF151
Page 1: ...1 ICE MAker Service manual Models RF15I ...
Page 2: ......
Page 28: ...26 Figure 7 1 Ice Maker Wiring Diagram WIRING ...
Page 40: ...38 NOTES ...
Page 41: ...39 NOTES ...
Page 42: ...40 NOTES ...
Page 43: ......