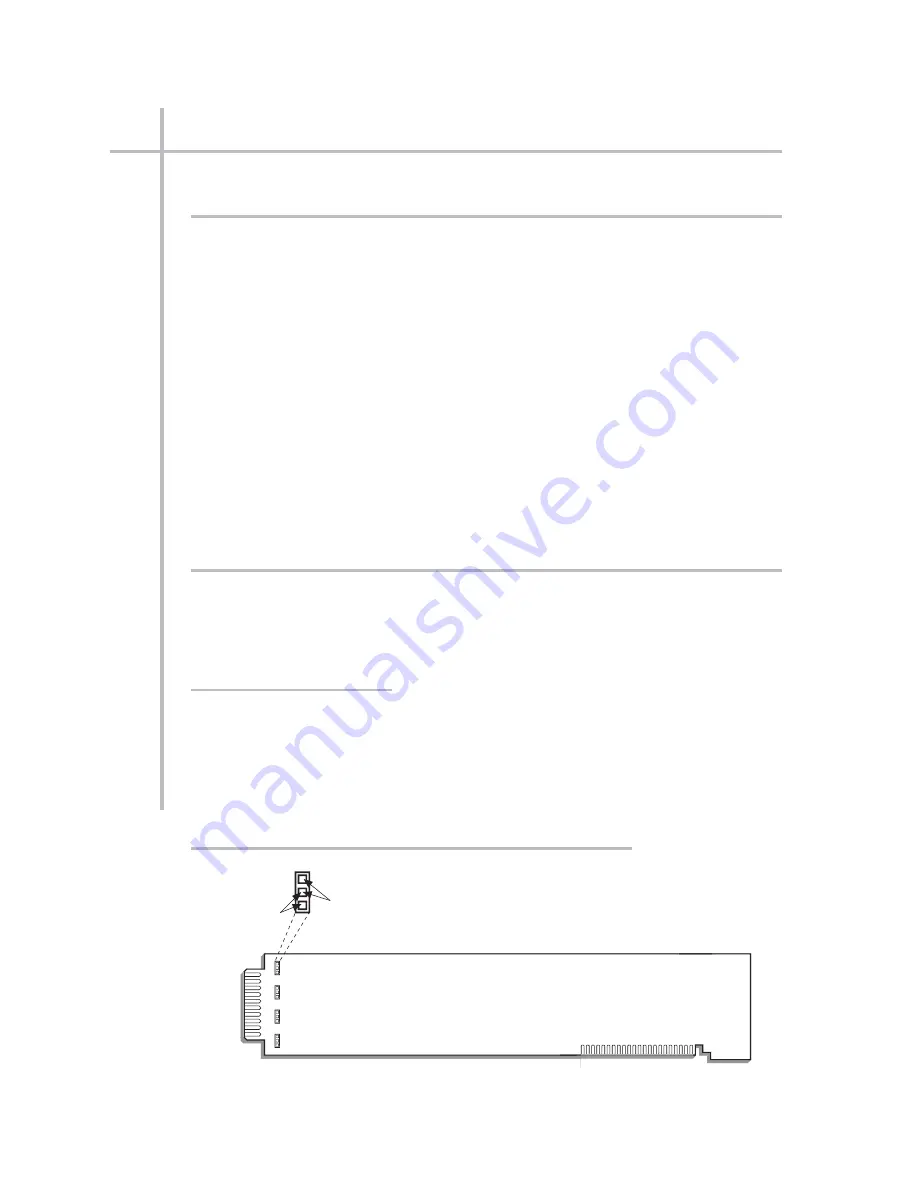
3
S
ETUP AND
/
OR
O
PERATING
C
ONSIDERATIONS
3.a S
ETTING A
10A18-4C C
HANNEL FOR
F
OUR
-W
IRE OR
T
HREE
-W
IRE
RTD C
ABLING
When the Model 10A18-4C is shipped, all four channels are normally set for the four-
wire RTD cabling shown in Fig. 1(a), above, since this mode of cabling normally yields
the highest accuracy. If you wish to use the three-wire cabling shown in Fig. 1(b) for a
given 10A18-4C channel, you should
1.
Remove the 10A18-4C card from its mainframe slot. For “Card Insertion and
Removal,” see Manual Section 1.B. Since the 10A18-4C is “hot-pluggable,” you
need NOT turn off mainframe power before removing the card.
2.
Refer to Fig. 3, below, and locate the four sets of “RTD CABLING” PROGRAMMING
JUMPER PINS, one for each channel, on the top (component) side of the card.
One “minijumper” is provided for each channel, for interconnecting any two adja-
cent jumper pins.
3.
Position the jumper for each active channel as shown in Fig. 3 to set the desired
wiring mode for that channel.
4.
Reinsert the 10A18-4C card into its mainframe slot.
3.b C
ONFIGURATION AND
C
ALIBRATION
For initial configuration of ANALOG INPUT CHANNELS dedicated to a specific Model
10A18-4C card when used in System 10, see the following section, along with the gen-
eral remarks on System 10 “real-channel” configuration in Manual Section 1.G.1 and
elsewhere in the System 10 Guidebook.
C
ALCULATED
C
ALIBRATION
In System 10, the initial configuration and
CALCULATED CALIBRATION
of a 10A18-
4C channel (No. “x”) involve direct entry of the channel’s TYPE CODE, SCALING FAC-
TOR (“m” coefficient), and ZERO OFFSET (“b” term) via the corresponding mnemonic
commands. The values of these parameters that are entered will depend on the RTD
type, range, and desired engineering units (°C or °F), as given in Table 2, below. For
S
ETUP AND
/
OR
O
PERATING
C
ONSIDERATIONS
10A18-4C.
5
Q
UAD
P
LATINUM
L
INEAR
RTD C
ARD
10A18-4C
Side 2
Rear I/O Connector
Channel 1
Connect these pins
for THREE-WIRE
RTD CABLING
Channel 2
Channel 3
Channel 4
Connect these pins
for FOUR-WIRE
RTD CABLING
Fig. 3 10A18-4C “RTD CABLING” Programming Jumper Pins
Summary of Contents for System 10
Page 31: ...GETTING YOUR SYSTEM 10 ON THE AIR SB 2 FOR A SIZED MAINFRAMES...
Page 67: ...GETTING YOUR SYSTEM 10 ON THE AIR SB 2 FOR B SIZED MAINFRAMES...
Page 122: ...THIS PAGE INTENTIONALLY BLANK...
Page 134: ...1 12 THIS PAGE INTENTIONALLY BLANK...
Page 142: ...1 20 THIS PAGE INTENTIONALLY BLANK...
Page 150: ...1 28 THIS PAGE INTENTIONALLY BLANK...
Page 174: ...10A16 4C 6 THIS PAGE INTENTIONALLY BLANK 10A16 4C QUAD PLATINUM RTD CARD...
Page 186: ...10A18 4C 8 THIS PAGE INTENTIONALLY BLANK 10A18 4C QUAD PLATINUM LINEAR RTD CARD...
Page 212: ...10A40 8 THIS PAGE INTENTIONALLY BLANK 10A40 FREQUENCY CARD...
Page 224: ...10A43 4 THIS PAGE INTENTIONALLY BLANK 10A43 DWELL ANGLE CARD...
Page 234: ...10A48 6 THIS PAGE INTENTIONALLY BLANK 10A48 FLOW CARD...
Page 242: ...10A61 2 4 THIS PAGE INTENTIONALLY BLANK 10A61 2 DUAL 4 20 MA CARD...
Page 252: ...10A63 2 6 THIS PAGE INTENTIONALLY BLANK 10A63 2 DUAL DC VOLTAGE CARD...
Page 270: ...10A69 4 6 THIS PAGE INTENTIONALLY BLANK 10A69 4 QUAD AC RMS CARD...
Page 276: ...10A70 2 6 THIS PAGE INTENTIONALLY BLANK 10A70 2 DUAL DC STRAIN GAGE CARD...
Page 288: ...10A72 2C 12 THIS PAGE INTENTIONALLY BLANK 10A72 2C ENHANCED DUAL DC STRAIN GAGE CARD...
Page 320: ...10A74 4C 18 THIS PAGE INTENTIONALLY BLANK 10A74 4C QUAD DC STRAIN GAGE TRACK HOLD CARD...
Page 342: ...10A96 8 THIS PAGE INTENTIONALLY BLANK 10A96 AMPLIFIED ACCELEROMETER VIBRATION CARD...
Page 362: ...AA30 4 12 THIS PAGE INTENTIONALLY BLANK AA30 4 QUAD LVDT CARD...
Page 374: ...AA41 2 4 12 THIS PAGE INTENTIONALLY BLANK AA41 2 AA41 4 DUAL QUAD FREQUENCY CARD...
Page 390: ...AA72 2 4 16 THIS PAGE INTENTIONALLY BLANK AA72 2 AA72 4 DUAL QUAD DC STRAIN GAGE CARD...
Page 394: ...1 32 THIS PAGE INTENTIONALLY BLANK...
Page 404: ...1 42 THIS PAGE INTENTIONALLY BLANK...