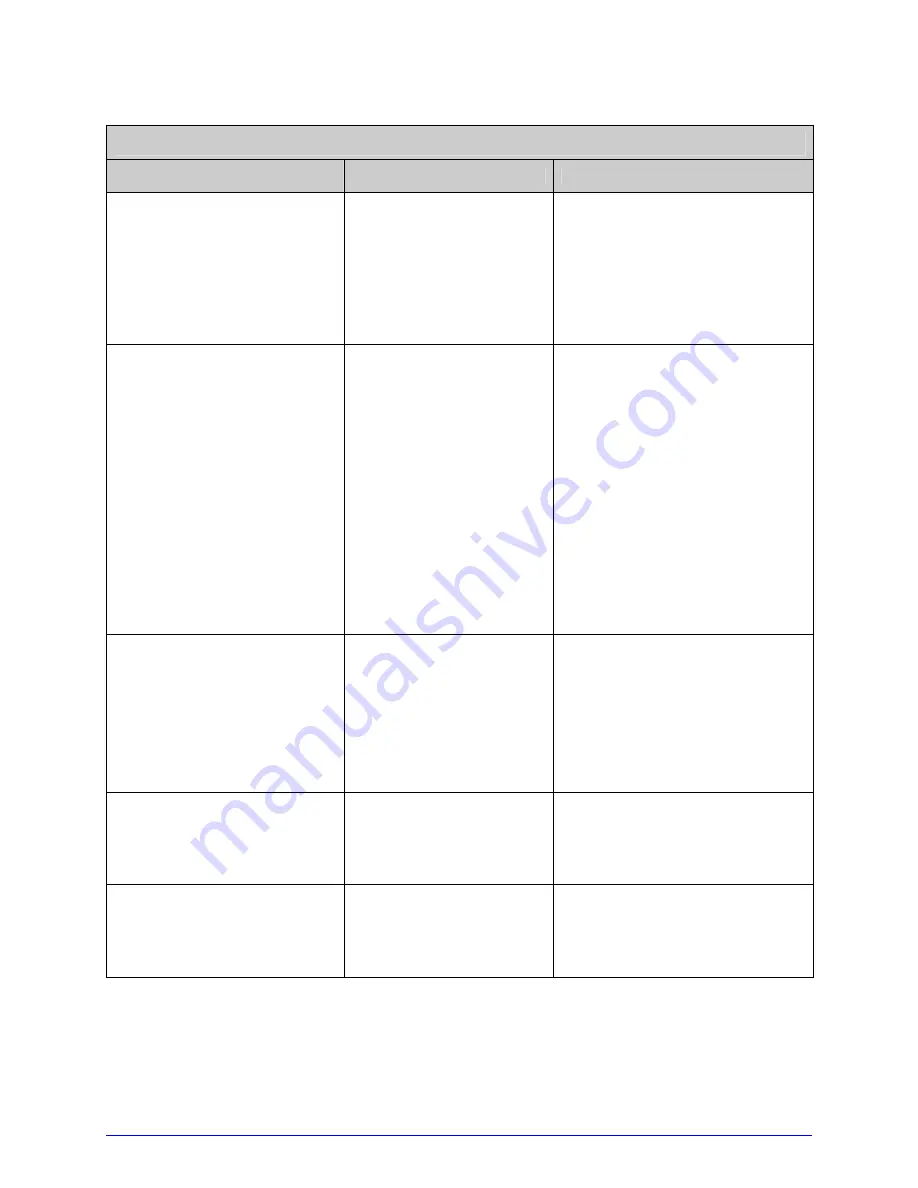
112
H-Class
Fault Messages (continued)
Displayed Message
Description
Possible Solution(s)
HEAD CLEANING FAULT
The scheduled
printhead cleaning has
been exceeded by an
amount equal to three
times the pre-
programmed distance.
Clean the printhead (see
Section 5.6.6).
To change the cleaning setting,
enter ADVANCED MENU /
MEDIA SETTINGS / PRINTHEAD
CLEANING MENU.
OUT OF STOCK
The printer cannot
detect the presence of
media.
Examine the printer for media
then proceed accordingly:
•
If the printer is out of
stock, load media; or,
•
If stock is loaded, ensure
that the Media Sensor is
calibrated (see Section
3.4), properly positioned
(see Section 3.2) and, if
the media has large gaps,
that the Paper Empty
Distance is adjusted (see
Section 4.2.1).
POSITION FAULT
Possible causes of this
fault include a firmware
update, a power failure
or reset during a ribbon,
out of stock or TOF fault,
and an incomplete
calibration process.
Press the FEED Key in an
attempt to identify and then
clear the fault. Perform
calibration (see Section 3.4).
PRINT ENGINE FAULT
A problem within the
print logic has been
detected.
Cycle printer power OFF and
ON. If the fault does not clear,
call for service.
RAM FAULT
A memory failure has
been detected.
Cycle printer power OFF and
ON. If the fault does not clear,
call for service.
Summary of Contents for H-4212X
Page 1: ...Operator s Manual...
Page 2: ......
Page 5: ......
Page 40: ...30 H Class...
Page 84: ...74 H Class...
Page 144: ...134 H Class...
Page 148: ...138 H Class...
Page 156: ...146 H Class...
Page 160: ...150 H Class Network Status page TCP IP Configuration page...
Page 162: ...152 H Class...
Page 163: ...H Class 153 Printer Options Communications and Diagnostics pages...
Page 164: ...154 H Class Network Print Options page...
Page 165: ...H Class 155 Reset Network Parameters page Change Password page...
Page 166: ...156 H Class...
Page 180: ...170 H Class...
Page 186: ...176 H Class...