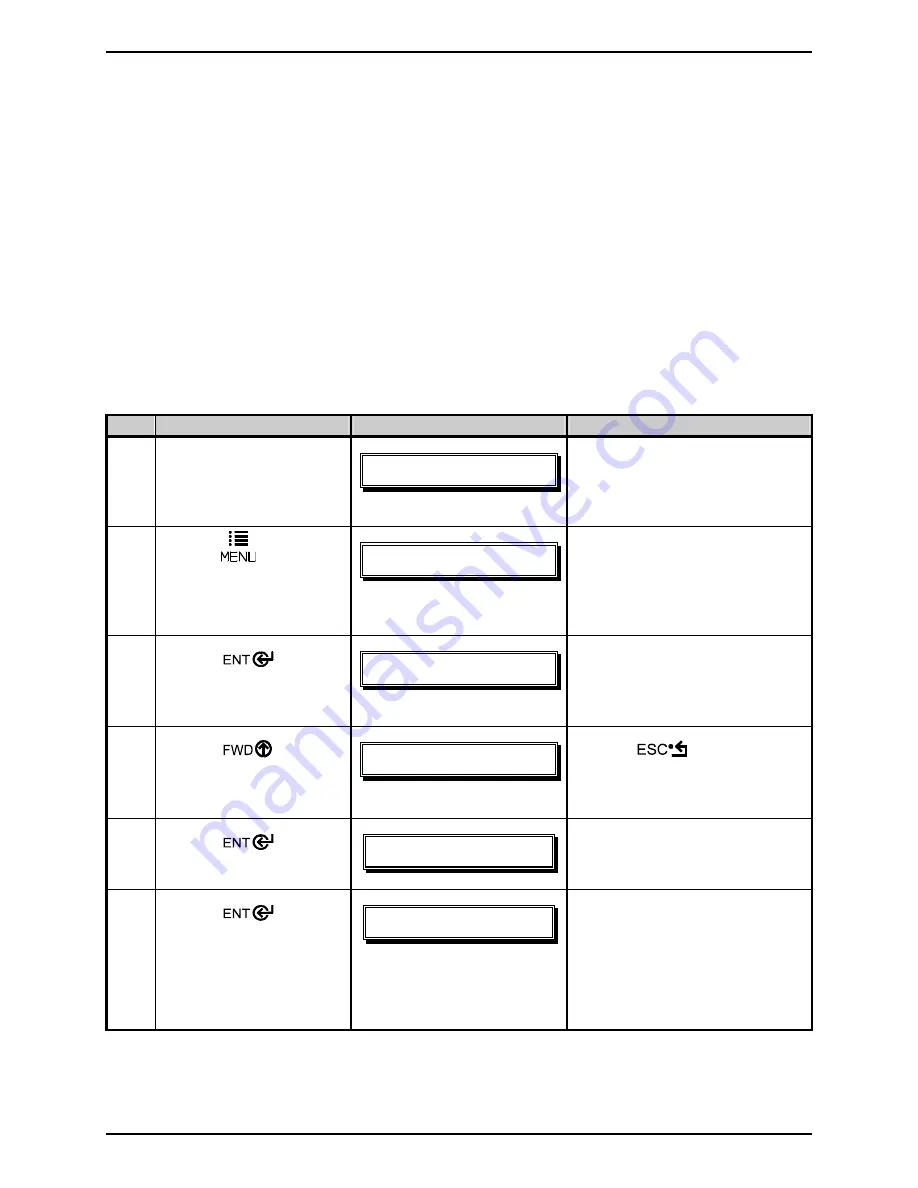
Adjustments and Maintenance
2-10
2.2.2.2 Standard
Calibration
During the Standard Calibration process, the printhead assembly can be raised for visual access to the
media and media sensor. In addition, displayed sensor readings can be used to indicate the best position
over the media. These features are helpful when using small, position-critical TOF notches or marks.
Three readings are required:
•
Empty: No media in the sensor.
•
Gap (or Mark): Only the backing, notch, or reflective mark in the sensor.
•
Paper: The label (with the liner attached) in the sensor.
Make sure media is loaded and that the appropriate Sensor Type has been selected, then perform the
Standard Calibration as follows:
Step
Action
Displayed Message
Comment
1
!
Turn ‘On’ the printer.
!
!!
VODBMJCSBUFE
!
!
Wait for the printer to initialize
(about six seconds) before
proceeding.
2
Press the
Key.
Raise the printhead
assembly.
!
NFOV!NPEF!
NFEJB!TFUUJOHT!
!!
!
!
You are entering Menu Mode.
3
Press the
Key to
enter the Media Settings
menu.
!
NFEJB!TFUUJOHT!
NFEJB!UZQF!
!
!
See the
Operator’s Manual
for the
menu layout.
4
Press the
Key and
scroll to ‘
SENSOR
CALIBRATION
’.
!
NFEJB!TFUUJOHT!
TFOTPS!DBMJCSBUJPO
!
!
!
Press the
Key to abort this
procedure.
5
Press the
Key.
!
TFOTPS!DBMJCSBUJPO!
QFSGPSN!DBMJCSBUJPO
!
!
You are beginning the standard
calibration procedure.
6
Press the
Key.
Remove the media from the
Media Sensor then press any
key.
!!
SFNPWF!MBCFM!TUPDL!
QSFTT!BOZ!LFZ!=zzz?
!
!
This sets the parameter for the
‘empty’ value.
Where ‘yyy’ is a numerical value
representing the current sensor
reading.
Summary of Contents for ?-class series
Page 4: ...ii ...
Page 5: ...i 1 Overview 1 0 Introduction 1 1 1 About this Printer 2 ...
Page 6: ...ii ...
Page 40: ...ii ...
Page 52: ...ii ...
Page 83: ...M 4206 Printer Assemblies 5 1 M 4206 ...
Page 84: ...M 4206 Printer Assemblies 5 2 A Front Covers ...
Page 86: ...M 4206 Printer Assemblies 5 4 B Side Covers 15 3013 01 ...
Page 88: ...M 4206 Printer Assemblies 5 6 C Printer Assembly 1 of 3 53 2153 01 ...
Page 90: ...M 4206 Printer Assemblies 5 8 D Printer Assembly 2 of 3 53 2153 01 ...
Page 92: ...M 4206 Printer Assemblies 5 10 E Printer Assembly 3 of 3 53 2153 01 ...
Page 94: ...M 4206 Printer Assemblies 5 12 F Main Board and Internal Cables 1 3 4 2 6 5 ...
Page 96: ...M 4206 Printer Assemblies 5 14 G Media Supply Hub 15 2763 01 ...
Page 98: ...M 4206 Printer Assemblies 5 16 H Printhead Assembly 15 2850 01 ...
Page 100: ...M 4206 Printer Assemblies 5 18 ...
Page 101: ...M 4208 Printer Assemblies 5 19 M 4208 ...
Page 102: ...M 4208 Printer Assemblies 5 20 A Front Covers ...
Page 104: ...M 4208 Printer Assemblies 5 22 B Side Covers Metal 15 3035 01 ...
Page 106: ...M 4208 Printer Assemblies 5 24 C Printer Assembly 1 of 3 53 2153 02 ...
Page 108: ...M 4208 Printer Assemblies 5 26 D Printer Assembly 2 of 3 53 2153 02 ...
Page 110: ...M 4208 Printer Assemblies 5 28 E Printer Assembly 3 of 3 53 2153 02 ...
Page 112: ...M 4208 Printer Assemblies 5 30 F Main Board and Internal Cables 1 3 4 2 6 5 ...
Page 114: ...M 4208 Printer Assemblies 5 32 G Media Supply Hub 15 2763 01 ...
Page 116: ...M 4208 Printer Assemblies 5 34 H Printhead Assembly 15 2850 01 ...
Page 118: ...M 4208 Printer Assemblies 5 36 ...
Page 119: ...M 4306 Printer Assemblies 5 37 M 4306 ...
Page 120: ...M 4306 Printer Assemblies 5 38 A Front Covers ...
Page 122: ...M 4306 Printer Assemblies 5 40 B Side Covers Metal 15 3035 01 ...
Page 124: ...M 4306 Printer Assemblies 5 42 C Printer Assembly 1 of 3 53 2153 03 ...
Page 126: ...M 4306 Printer Assemblies 5 44 D Printer Assembly 2 of 3 53 2153 03 ...
Page 128: ...M 4306 Printer Assemblies 5 46 E Printer Assembly 3 of 3 53 2153 03 ...
Page 130: ...M 4306 Printer Assemblies 5 48 F Main Board and Internal Cables 1 3 4 2 6 5 ...
Page 132: ...M 4306 Printer Assemblies 5 50 G Media Supply Hub 15 2763 01 ...
Page 134: ...M 4306 Printer Assemblies 5 52 H Printhead Assembly 15 2850 01 ...
Page 136: ......
Page 137: ...Option Assemblies 5 55 Options ...
Page 138: ...Option Assemblies 5 56 A Thermal Transfer CSI 78 2483 01 CSO 78 2483 02 Direct Thermal ...
Page 140: ...Option Assemblies 5 58 B Internal Rewind 78 2484 01 Without Rewind ...
Page 142: ...Option Assemblies 5 60 C Peel and Present 78 2482 01 78 2482 02 ...
Page 144: ...Option Assemblies 5 62 D Cutter 78 2480 01 ...
Page 146: ...Option Assemblies 5 64 E Present Sensor 78 2481 01 ...
Page 148: ...Option Assemblies 5 66 F LAN 78 2584 01 1 2 3 ...