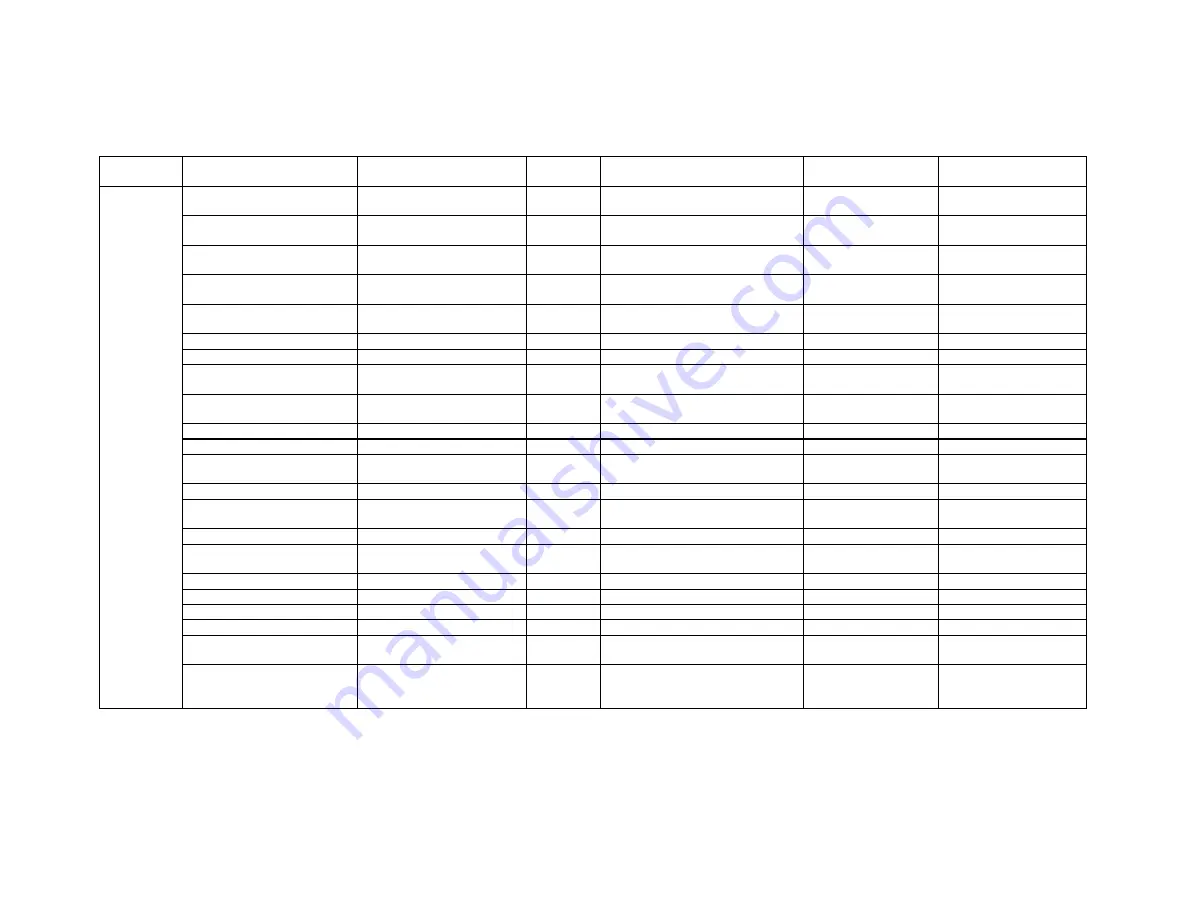
Prepared by: TED
Rev. #: 13
Approved by: MCR
33
15May2006
© W.S. Darley & Co.
1200569.doc
Engine Maintenance:
HONDA GX200 ENGINE MAINTENANCE REQUIREMENTS
SYSTEM ID
ACTION
INTERVAL
MNT LVL
SPARES REQUIRED/DWG NO.
TOOLS/SE
REQUIRED
PMS NUMBER
Engine/Fuel
System
Inspect fuel tank
Upon receipt, and each time
unit is operated
Unit
Fuel tank, p/n 4217707
Replace fuel tank assembly
Upon failure
Unit
Tank, Fuel, Assembly, p/n KE00109
(See dwg. #DGM1108)
Replace fuel tank
Upon failure
Unit
Tank, Fuel, 2.5 gal. plastic, p/n
4217707 (See dwg. #DGM1108)
Replace fuel tank mount bracket
Upon failure
Depot
Bracket, fuel tank mount, p/n 4025803
(See dwg. # DGM1108)
7/16” Open end wrench
½” Open end wrench
Replace poly tie down
Upon failure
Unit
Tie down, poly, p/n 4427100 (See
dwg. # DGM1108)
Replace fuel cap
Upon failure
Unit
Cap, Fuel Tank, p/n 4217712
Replace fuel gage
Upon failure
Unit
p/n 4217713
Check oil level
Prior to each use
Unit
4 stroke SAE 10W-30 detergent oil
(.63 U.S. qts.)
Change oil
First 20 hrs and 100 hrs/6 mos
thereafter
Unit
4 stroke SAE 10W-30 detergent oil
(.63 U.S. qts.)
10mm Socket
Check air filter
After every use.
Unit
n/a
Replace air filter
Every 300 hrs of ops
Unit
Air filter, Honda p/n 17210-ZE1-505
Replace fuel filter
Every 300 hrs. of ops
Unit
Fuel filter, Honda p/n 16910-ZE8-015
Fuel Filter, Darley p/n 4207201
Check fuel line
Quarterly
Unit
n/a
Replace fuel line
Upon failure
Unit
Hose, .25 x 1.75 fuel, p/n 4402325
(See dwg. #DGM1109)
Pliers
Check high speed adjustment
Yearly Unit
n/a
Hand
Tachometer
Clean sediment cup
Every 100 hrs., or 6 mos., or
during every oil change
Unit n/a
10mm
Socket
High flash-point solvent
Clean fuel tank
Yearly or every 300 hrs.
Unit
n/a
Check spark plug
Every 100 hrs. or 6 mos.
Unit
n/a
13/16" Deep socket
Replace plug
Upon failure
Unit
NGK #BPR6ES or equivalent
13/16" Deep socket
Check/readjust valve clearance
Every 300 hrs. or 1 yr.
Unit
n/a
Clean carburetor
As necessary
Unit
n/a
10mm Socket
High flash-point solvent
Remove corrosion
As needed
Unit
n/a
Silicone grease,
High flash point solvent,
paint, etc.