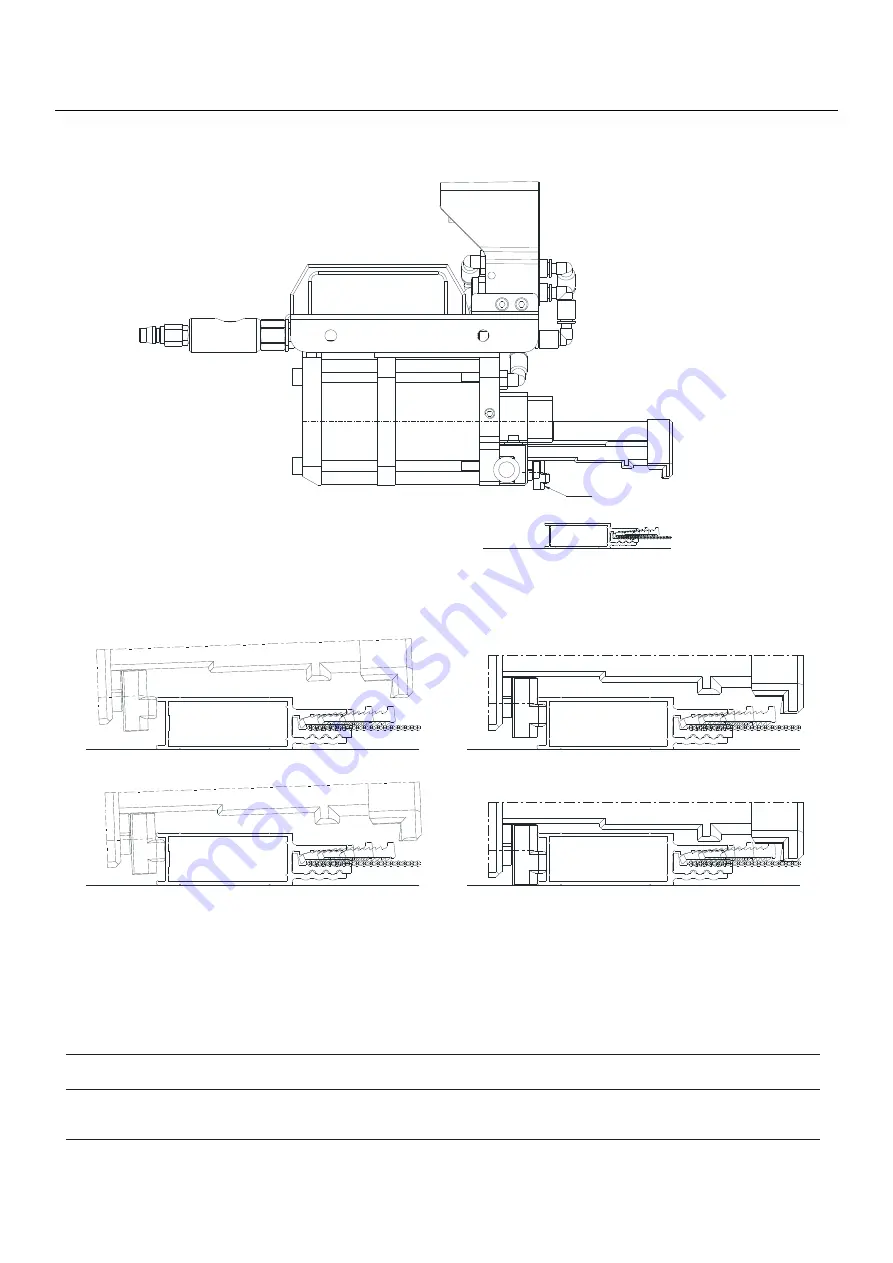
DARLEY
SCREENGUARD STAINLESS STEEL MESH SECURITY SYSTEM
25
Code ZOX14861
Use and maintenance manual
Page 14 of 24
Correct die for frame inserted
PHASE 1:
Mount the profile support according to the profile to be worked.
Set the frame on a plane surface, with the wedges upward.
Insert the punching machine from above on the frame.
Pull the knob toward the outside.
Work to be executed on AU01001.
-
-
-
-