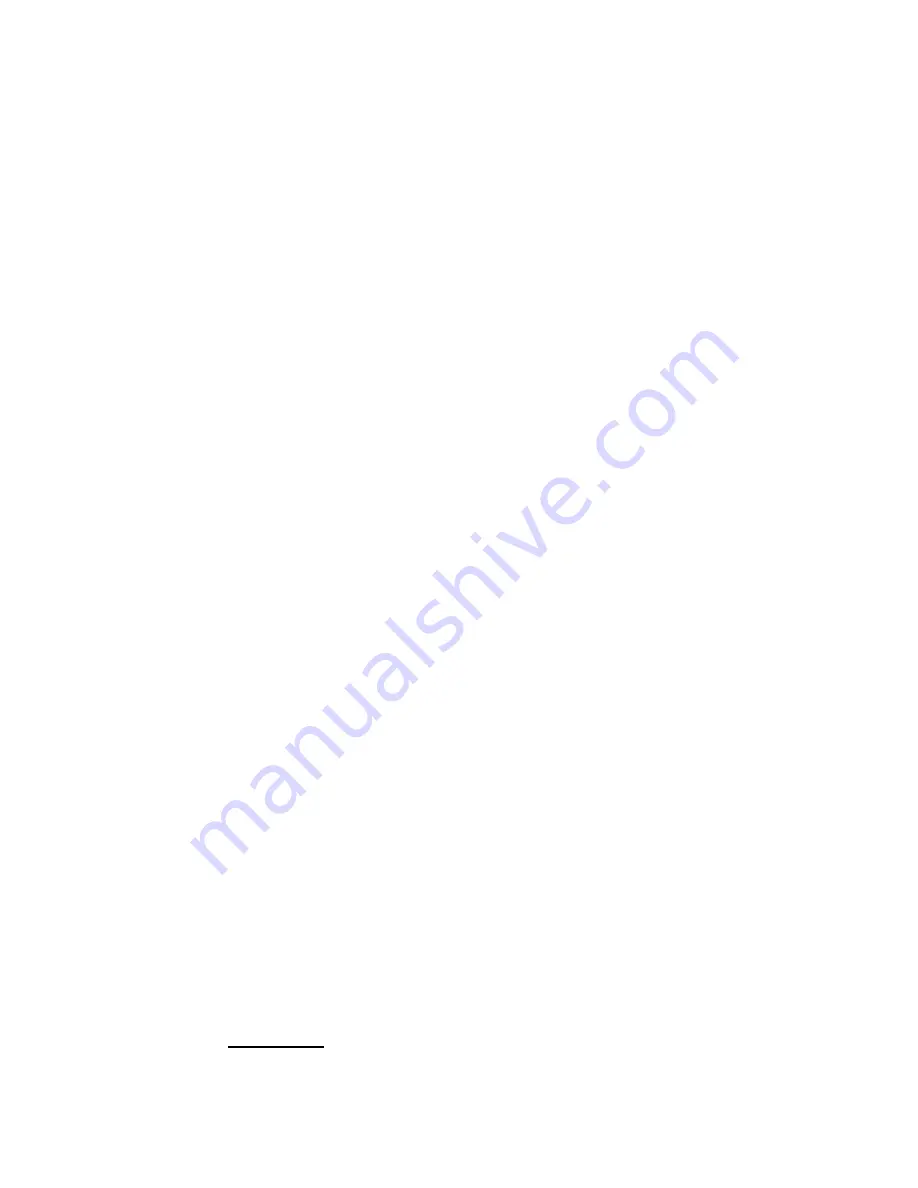
33
The unit stopped working and the screen
displays “Sharpening Interrupted”:
•
This message will appear if the user
presses the “Stop” button during sharpen-
ing. It will also appear if the controller de-
tects a large load on the chuck turning
motor. This is typically caused by dirt or
grit accumulating on the Chuck Body,
Chuck Tube Liner, or the Cam Follower
Assembly. Turn the machine off and per-
form the standard maintenance procedures
listed on pages 31 & 32. Restart the ma-
chine and see if it runs without interrup-
tion. If the controller continues to show
this message, call Darex customer service
for assistance.
The display does not come on when I
plug the unit it:
•
The auto controller receives its power
through the AC plugs in the rear of the
unit. Make sure there is power to the out-
let you are using.
•
Make sure the wiring on the back of the
unit matches that of the user manual
(power comes in to the controller, and
both pigtails are firmly seated between the
controller and the XT unit).
•
Try unplugging and re-plugging these
cords to ensure they are well seated.
•
Finally, make sure the on/off switch on the
XT-3000 machine is powered on. The dis-
play will not come on until you power up
the XT-3000. If unsuccessful, call Darex
customer service for assistance @ 800-
547-0222.
The unit powers up, the display is on, but
pushing the “Start” button to sharpen
nothing happens:
•
There is a cord that connects the sharpen-
ing port to the Auto Controller/Display,
see page 11. Be sure that the 5 pin DIN
connector on this cord is firmly seated into
the connector on the Controller/Display,
paying careful attention to cord/connector
orientation. Important: See information
on page 11. Inspect the cable, coming
from the controller to the sharpening port,
•
The optical switch in the Sharpening Fix-
ture in faulty, call Darex customer service
for assistance.
•
Check the small cable coming from the
sharpening port to the Gear Motor.
•
Finally, remove both covers on the Gear
Motor and Gear located on the Sharpening
Fixture. Verify the Drive Gear is secured to
the Gear Motor.
The unit powers up and runs the sharp-
ening system, but the vacuum does not
come on:
•
The vacuum receptacle for the Auto sharp-
ening system is located on the back of the
Controller/Display housing, see page 14.
Make sure this connector is firmly seated.
•
The connector is fused with two 8A time
delay fuses (1.6A on the 230V interna-
tional model). Make sure these fuses are
intact. If a fuse is found to be blown, then
both fuses should be replaced with the ap-
propriate capacity. You can find the part
numbers for these fuses listed on page 28.
Note: Using fuses not supplied by DAREX is
not recommended and may cause damage
to the Controller/Display.
If the grind motor starts but the Auto
Display is off:
•
The internal relay may be defective. This
can be detected by checking for voltage at
the vacuum output receptacle with an
electrical meter.
Trouble Shooting
Summary of Contents for XT-3000
Page 1: ......
Page 2: ...2...
Page 20: ...20...
Page 25: ...25 Auto Sharpening Fixture...
Page 27: ...27 Geared Chuck Auto...
Page 29: ...29 Controller Display...
Page 30: ...30...
Page 34: ...34...
Page 35: ...35...
Page 36: ...36...