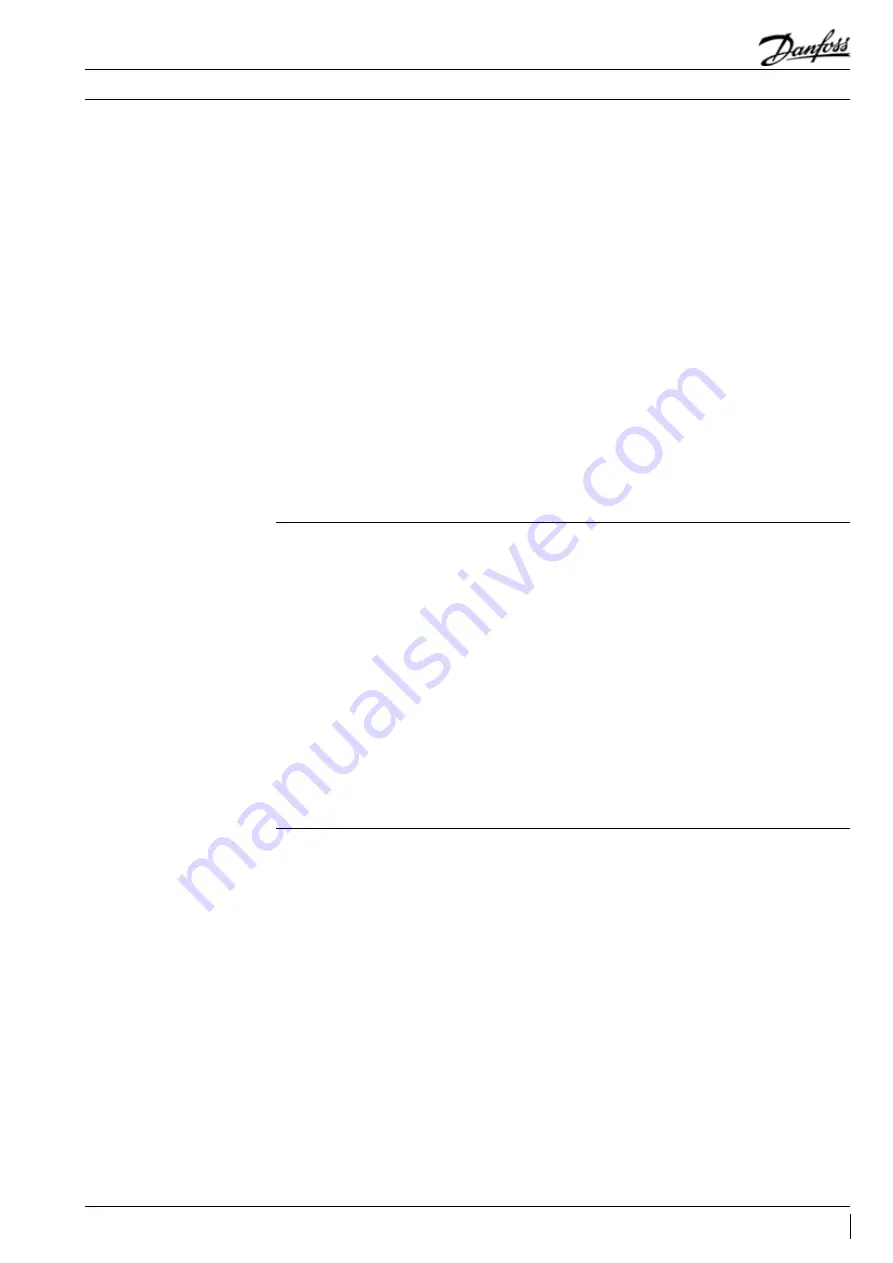
Sound and vibration management
Compressor sound radiation
For sound radiating from the compressor, the
emission path is airborne and the sound waves
are travelling directly from the machine in all
directions.
The Danfoss WSH scroll compressor is designed
to be quiet and the frequency of the sound
generated is pushed into the higher ranges,
which not only are easier to reduce but also do
not generate the penetrating power of lower-
frequency sound.
Use of sound-insulation materials on the inside of
unit panels is an effective means of substantially
reducing the sound being transmitted to the
outside. Ensure that no components capable
of transmitting sound/vibration within the unit
come into direct contact with any non-insulated
parts on the walls of the unit.
Due to the Danfoss scroll’s unique design of
a full-suction gas-cooled motor, compressor
body insulation across its entire operating
range is possible. Acoustic hoods are available
from Danfoss as accessories. They have been
developed to meet specific extra low noise
requirements. They incorporate sound proofing
materials and offer excellent high and low
frequency alternative.
These hoods are quick and easy to install and do
not increase the overall size of the compressors
to a great extend.
Refer to section “Running sound level” for sound
attenuation and code numbers.
Vibration isolation constitutes the primary
method for controlling structural vibration.
Danfoss WSH scroll compressors are designed to
produce minimal vibration during operations.
The use of rubber isolators on the compressor
base plate or on the frame of a manifolded unit
is very effective in reducing vibration being
transmitted from the compressor(s) to the unit.
Once the supplied rubber grommets have been
properly mounted, vibrations transmitted from
the compressor base plate to the unit are held
to a strict minimum. In addition, it is extremely
important that the frame supporting the
mounted compressor be of sufficient mass and
stiffness to help dampen any residual vibration
potentially transmitted to the frame. For further
information on mounting requirements, please
refer to the section on mounting assembly.
The tubing should be designed so as to both
reduce the transmission of vibrations to other
structures and withstand vibration without
incurring any damage. Tubing should also be
designed for three-dimensional flexibility. For
more information on piping design, please see
the section entitled “Essential piping design
recommendations”.
Gas pulsation
Mechanical vibrations
The Danfoss WSH scroll compressor has been
designed and tested to ensure that gas pulsation
has been optimized for the most commonly
encountered air conditioning pressure ratio. On
heat pump installations and other installations
where the pressure ratio lies beyond the
typical range, testing should be conducted
under all expected conditions and operating
configurations to ensure that minimum gas
pulsation is present. If an unacceptable level
is identified, a discharge muffler with the
appropriate resonant volume and mass should
be installed. This information can be obtained
from the component manufacturer.
31
FRCC.PC.028.A5.02
Application Guidelines