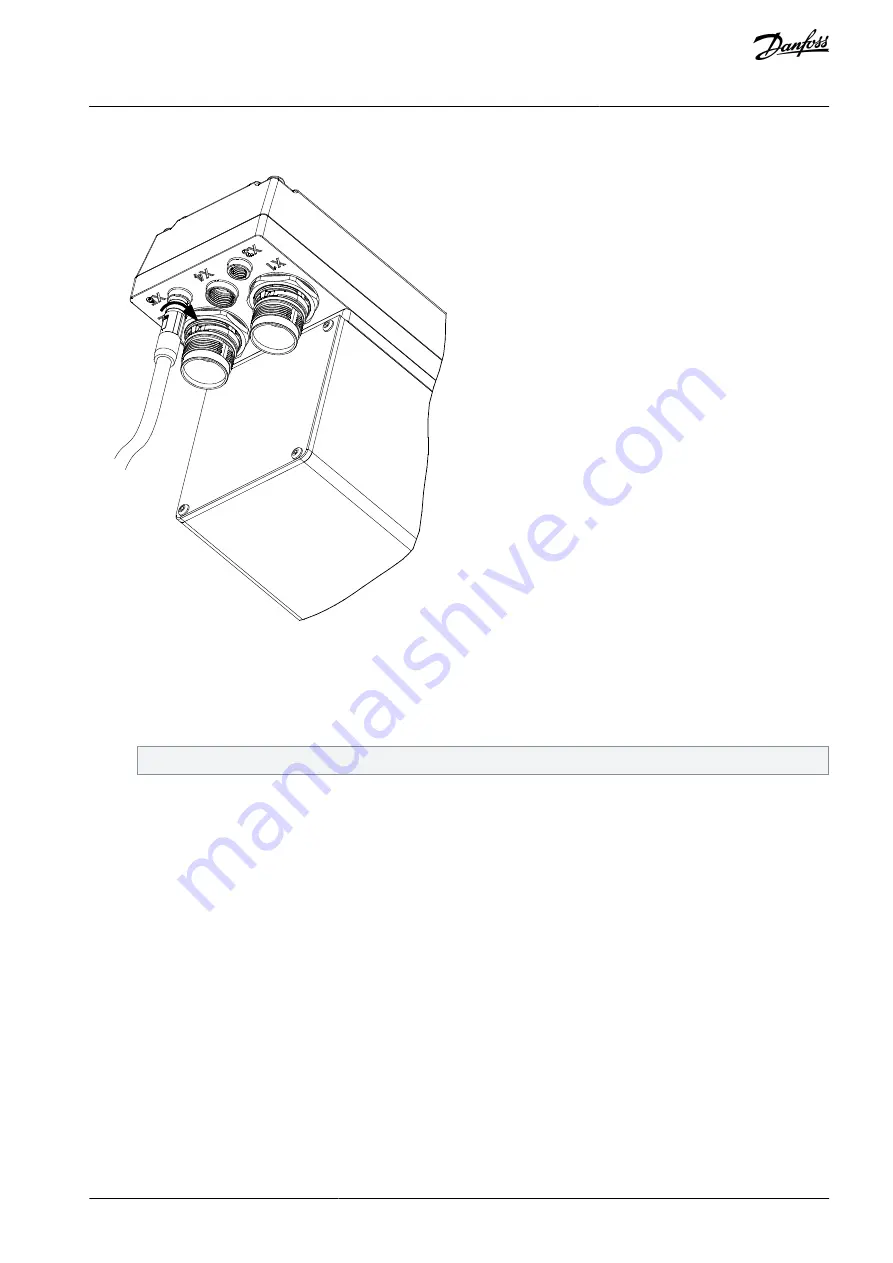
1.
2.
5.9.5.3 Connecting the LCP Cable to Port X5
e
3
0
b
e
6
6
9
.1
1
Illustration 40: Connecting the LCP Cable
Procedure
Align the connector on the LCP cable (not supplied) with the LCP connector marked X5 on the ISD 510/DSD 510 servo drive.
Press the connector towards the electronic housing of the servo drive and tighten the threaded ring of the connector by
turning it clockwise. The maximum tightening torque is 0.2 Nm.
The LCP cable can be ordered as an accessory.
AQ262449648484en-000101 / 175R1135 | 71
Danfoss A/S © 2020.08
Electrical Installation
VLT® Servo Drive System ISD 510/DSD 510
Operating Guide