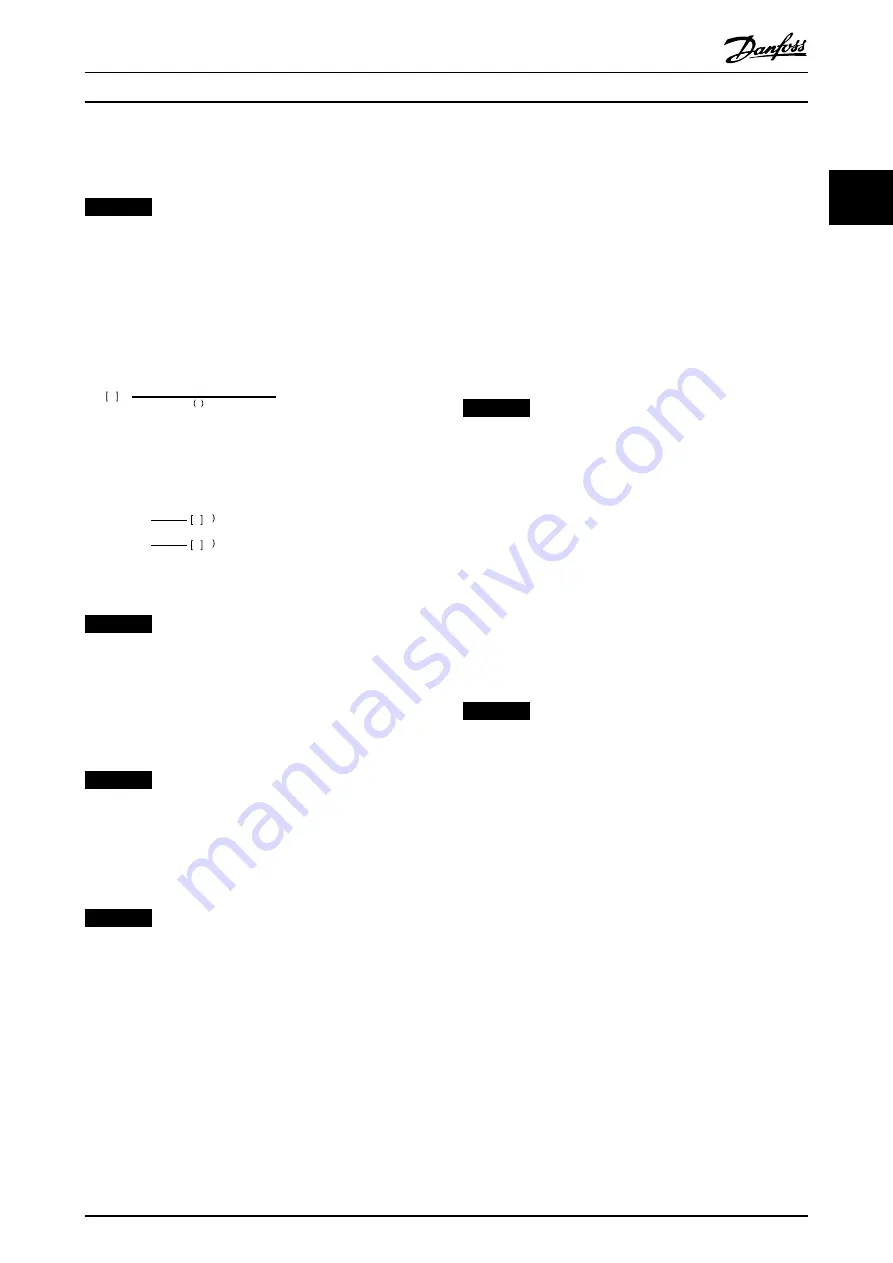
The threshold can be adjusted in
2-14 Brake voltage reduce
,
with 70 V range.
NOTICE
Make sure that the brake resistor can cope with a
voltage of 410 V or 820 V.
Danfoss recommends calculating the brake resistance R
rec
according to the formula below. The recommended brake
resistance guarantees that the frequency converter is able
to brake at the highest braking torque (M
br(%)
) of 160%.
R
rec
Ω =
Udc
2 x 100x 0.83
P
motor
x Mbr
%
xη
VLT
x η
motor
η
motor
is typically at 0.80 (
≤
75. kW); 0.85 (11–22 kW)
η
VLT
is typically at 0.97
For FC 360, R
rec
at 160% braking torque is written as:
480
V : Rrec = 396349
Pmotor Ω
1
480
V : Rrec = 397903
Pmotor Ω
2
1) For frequency converters ≤ 7.5 kW shaft output
2) For frequency converters 11–75 kW shaft output
NOTICE
The resistance of the brake resistor should not be higher
than the value recommended by Danfoss. If a brake
resistor with a higher ohmic value is selected, the 160%
braking torque may not be achieved because the
frequency converter might cut out for safety reasons.
The resistance should be bigger than R
min
.
NOTICE
If a short circuit in the brake transistor occurs, power
dissipation in the brake resistor is only prevented by
using a mains switch or contactor to disconnect the
mains for the frequency converter. (The contactor can be
controlled by the frequency converter).
NOTICE
Do not touch the brake resistor because it can get very
hot during braking. Place the brake resistor in a secure
environment to avoid fire risk.
2.9.4 Control with Brake Function
The brake is protected against short-circuiting of the brake
resistor, and the brake transistor is monitored to ensure
that short-circuiting of the transistor is detected. A relay/
digital output can be used for protecting the brake resistor
from overloading caused by a fault in the frequency
converter.
In addition, the brake enables readout of the momentary
power and the mean power for the latest 120 s. The brake
can also monitor the power energising and make sure it
does not exceed a limit selected in
2-12 Brake Power Limit
(kW)
.
NOTICE
Monitoring the brake power is not a safety function; a
thermal switch is required to prevent the brake power
from exceeding the limit. The brake resistor circuit is not
earth leakage protected.
Overvoltage control (OVC)
(exclusive brake resistor) can be
selected as an alternative brake function in
2-17 Over-
voltage Control
. This function is active for all units. The
function ensures that a trip can be avoided if the DC link
voltage increases. This is done by increasing the output
frequency to limit the voltage from the DC link. It is a
useful function, e.g. if the ramp-down time is too short to
avoid tripping of the frequency converter. In this situation,
the ramp-down time is extended.
NOTICE
OVC can be activated when running a PM motor (when
1-10 Motor Construction
is set to
[1] PM non salient SPM
).
Product Overview
Design Guide
MG06B402
Danfoss A/S © 09/2014 All rights reserved.
43
2
2