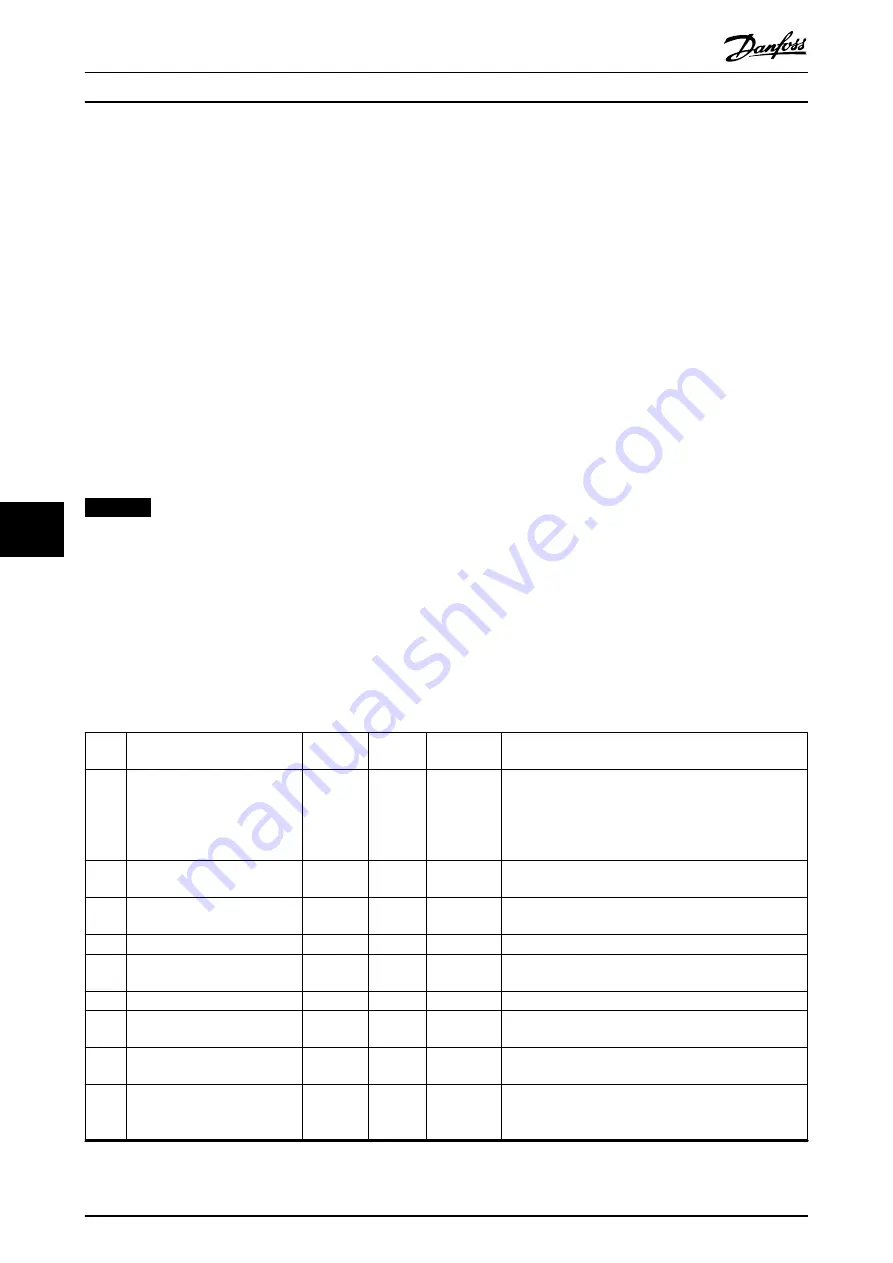
8.2.1 Warning/Alarm Messages
The LEDs on the LCP signal a warning or an alarm. A code
in the display is also shown.
A warning remains active until its cause is no longer
present. Under certain circumstances, operation of the
motor can still be continued. Warning messages are not
necessarily critical.
An alarm makes the frequency converter trip. Alarms must
be reset to restart operation once their cause has been
rectified.
3 ways of resetting alarms
•
By pressing [Reset].
•
Via a digital input with the reset function.
•
Via serial communication/optional fieldbus.
NOTICE
After a manual reset pressing [Reset], press [Auto On] to
restart the motor.
If an alarm cannot be reset, the reason could be that its
cause has not been rectified, or that the alarm is trip lock
(see also
).
Trip lock alarms offer extra protection, meaning that the
mains supply must be switched off before the alarm can
be reset. After being switched back on, the frequency
converter is no longer blocked and can be reset as
described once the cause has been rectified.
Alarms that are not trip lock can also be reset using the
automatic reset function in
parameter 14-20 Reset Mode
.
(Warning: Automatic wake-up is possible).
When a warning or alarm is marked against a code in
, either a warning occurs before an alarm, or it is
possible to specify whether a warning or an alarm shows
for a given fault.
For instance, this selection is possible in
parameter 1-90 Motor Thermal Protection
. After an alarm or
trip, the motor continues coasting, and the alarm and
warning flash. Once the problem has been rectified, only
the alarm continues flashing until the frequency converter
is reset.
8.2.2 Alarm and Warning List
An (X) marked in
indicates that the warning or alarm has occurred. A warning precedes an alarm.
Numb
er
Description
Warning
Alarm
Trip lock
Cause
2
Live zero error
X
X
–
Signal on terminal 53 or 54 is less than 50% of value set
in
parameter 6-10 Terminal 53 Low Voltage
,
parameter 6-12 Terminal 53 Low Current
,
parameter 6-20 Terminal 54 Low Voltage
, and
parameter 6-22 Terminal 54 Low Current
.
3
No motor
X
–
–
No motor has been connected to the output of the
frequency converter, or 1 motor phase is missing.
4
Mains phase loss
1)
X
X
X
Missing phase on supply side, or the voltage imbalance is
too high. Check the supply voltage.
7
DC overvoltage
1)
X
X
–
Intermediate circuit voltage exceeds limit.
8
DC undervoltage
1)
X
X
–
Intermediate circuit voltage drops below the voltage
warning low limit.
9
Inverter overloaded
X
X
–
More than 100% load for too long.
10
Motor ETR overtemperature
X
X
–
Motor is too hot due to more than 100% load for too
long.
11
Motor thermistor overtem-
perature
X
X
–
Thermistor or thermistor connection is disconnected.
12
Torque limit
X
X
–
Torque exceeds value set in either
parameter 4-16 Torque
Limit Motor Mode
or
parameter 4-17 Torque Limit Generator
Mode
.
Troubleshooting
PROFINET
52
Danfoss A/S © 04/2017 All rights reserved.
MG06G102
8
8
Summary of Contents for VLT AutomationDrive FC 360
Page 2: ......