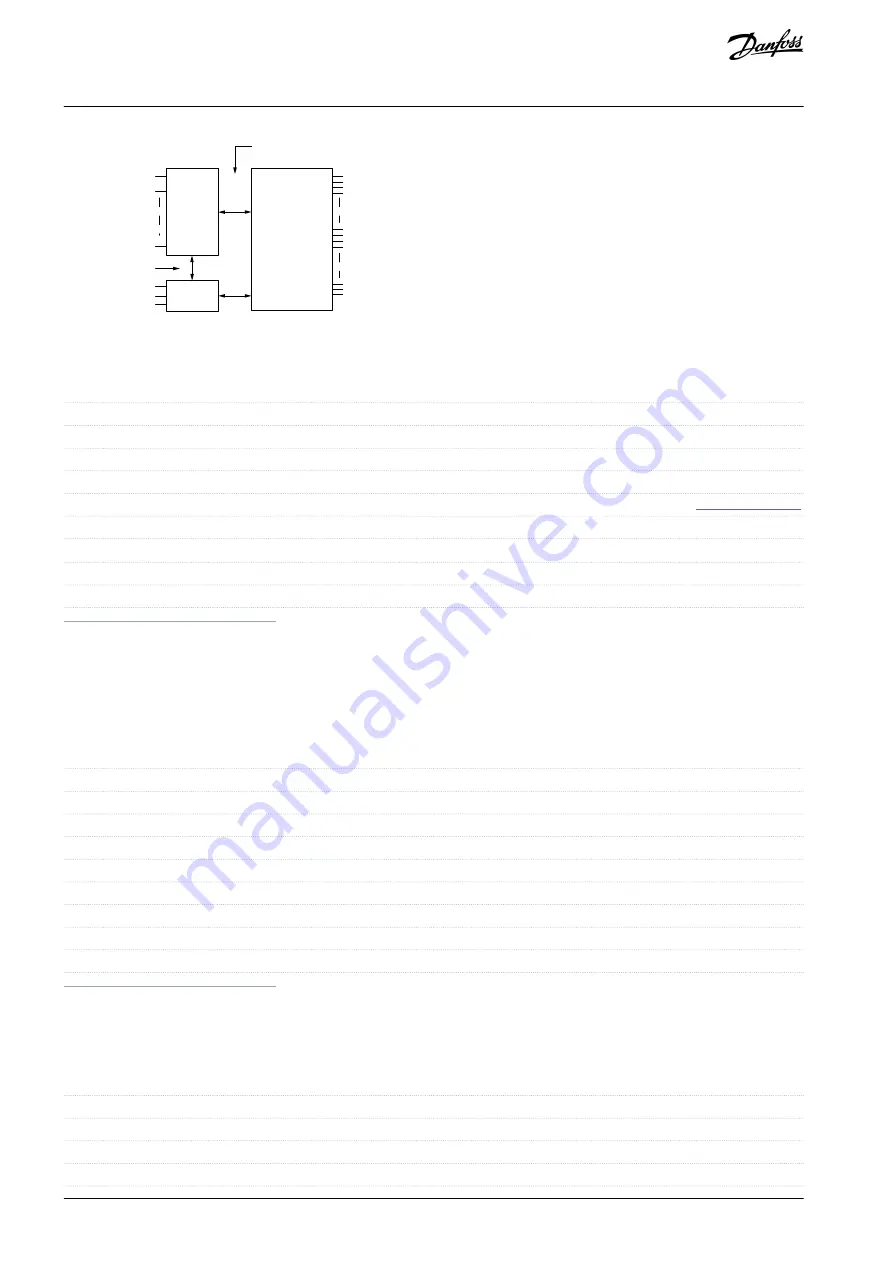
Mains
Functional
isolation
PELV isolation
Motor
DC-bus
High
voltage
Control
+24 V
RS485
18
37
e
3
0
b
a
1
1
7
.1
1
Illustration 12: PELV Isolation
5.3.4 Pulse/Encoder Inputs
Programmable pulse/encoder inputs
2/1
Terminal number pulse/encoder
29, 33
(1)
/32
(2)
, 33
(2)
Maximum frequency at terminals 29, 32, 33
110 kHz (Push-pull driven)
Maximum frequency at terminals 29, 32, 33
5 kHz (Open collector)
Maximum frequency at terminals 29, 32, 33
4 Hz
Voltage level
Maximum voltage on input
28 V DC
Input resistance, R
i
Approximately 4 kΩ
Pulse input accuracy (0.1–1 kHz)
Maximum error: 0.1% of full scale
Encoder input accuracy (1–11 kHz)
Maximum error: 0.05% of full scale
1
Pulse inputs are 29 and 33.
2
Encoder inputs: 32=A, 33=B.
The pulse and encoder inputs (terminals 29, 32, 33) are galvanically isolated from the supply voltage (PELV) and other high-voltage
terminals.
5.3.5 Digital Outputs
Programmable digital/pulse outputs
2
Terminal number
27, 29
(1)
Voltage level at digital/frequency output
0–24 V
Maximum output current (sink or source)
40 mA
Maximum load at frequency output
1 kΩ
Maximum capacitive load at frequency output
10 nF
Minimum output frequency at frequency output
0 Hz
Maximum output frequency at frequency output
32 kHz
Accuracy of frequency output
Maximum error: 0.1% of full scale
Resolution of frequency outputs
12 bit
1
Terminals 27 and 29 can also be programmed as input.
The digital output is galvanically isolated from the supply voltage (PELV) and other high-voltage terminals.
5.3.6 Analog Output
Number of programmable outputs
1
Terminal number
42
Current range at analog output
0/4 to 20 mA
Maximum load GND - analog output less than
500 Ω
Accuracy on analog output
Maximum error: 0.5% of full scale
AN354546796134en-000201 / 130R0954
32 | Danfoss A/S © 2021.05
Specifications
VLT®AutomationDrive EZ FC 321
Installation Guide