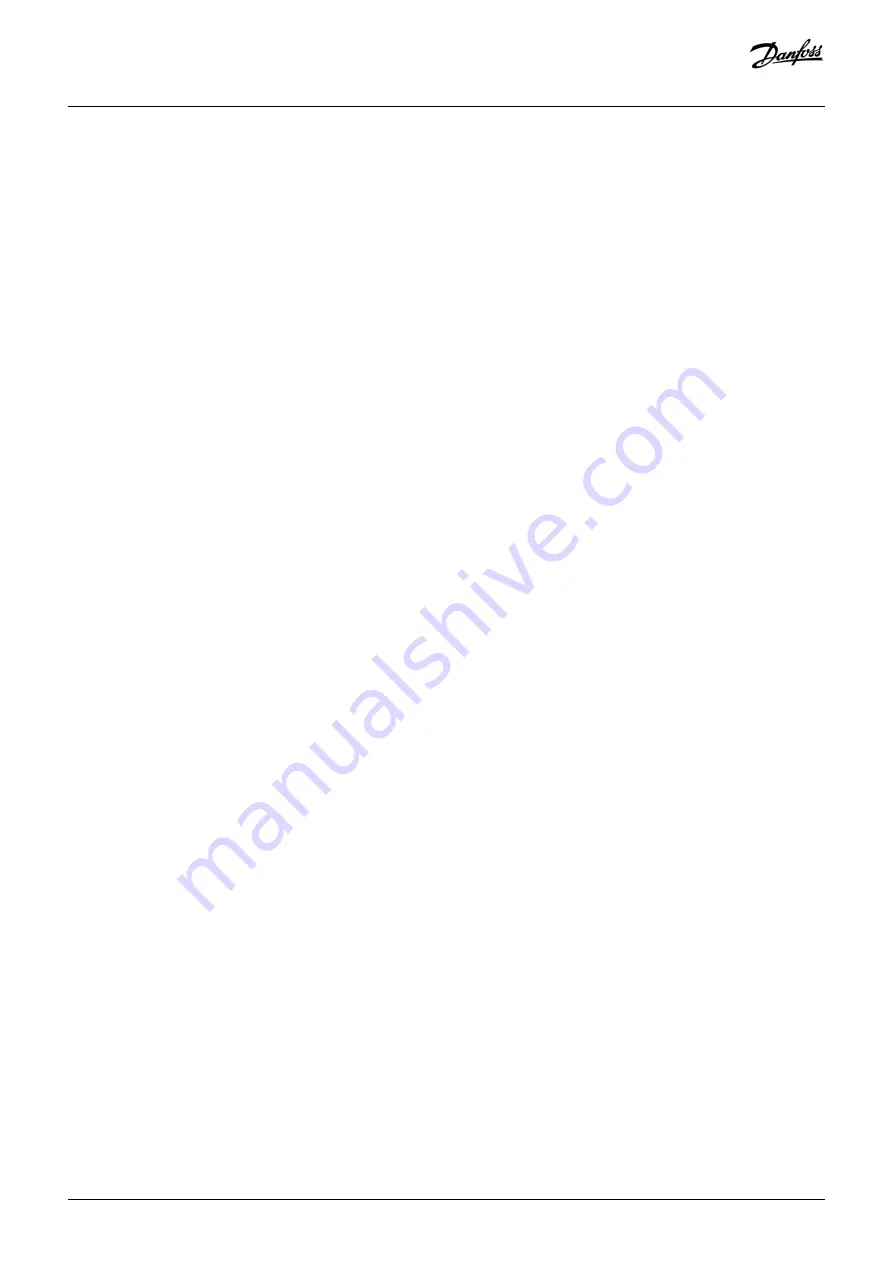
Troubleshooting
Check that OPTBC parameter “Resolver Poles” and possible Gear Ratio parameters in application match motor pole count.
12.10.111 Fault 43 - Encoder fault, Subcode S9 - Missed Start Angle
Cause
Encoder zero positioning identification run has not been made.
The encoder start angle is missing.
Troubleshooting
Make encoder identification run.
12.10.112 Fault 43 - Encoder fault, Subcode S10 - Sin/Cos encoder feedback is missing
Cause
Problem detected in encoder signals.
For the closed loop control, encoder modes "EnDat only" or "SSI only" (absolute channel only) are not allowed.
Troubleshooting
•
Do a check of the wiring, jumper settings, and encoder mode.
•
Change OPTBE “Operating mode” parameter is either "EnDat+SinCos", "SSI+SinCos" or "SinCos only", or avoid using closed loop
control.
12.10.113 Fault 43 - Encoder fault, Subcode S11 - Encoder angle is drifting
Cause
Error angle between the angle read from the absolute channel and the angle calculated from the incremental channels.
Troubleshooting
•
Check the encoder cable, cable shield, and grounding of the cable shield.
•
Check the mechanical mounting of the encoder and make sure that the encoder is not slipping.
•
Check the encoder parameters (for example, encoder ppr).
12.10.114 Fault 43 - Encoder fault, Subcode S12 - Dual speed supervision fault
Cause
Encoder speed supervision. The difference between the encoder speed and estimated speed is too large. Dual speed supervision:
Estimated speed and encoder speed difference is too high (0.05 x f
n
or minimum motor nominal slip frequency). See variable
EstimatedShaftFrequency.
Specifications
Operating Guide | VACON® NX Inverters FI4-FI8
AQ299433367205en-000101 / DPD00908
154 | Danfoss A/S © 2019.07
Summary of Contents for VACON NX FI6
Page 1: ...Operating Guide VACON NX Inverters FI4 FI8...
Page 2: ......