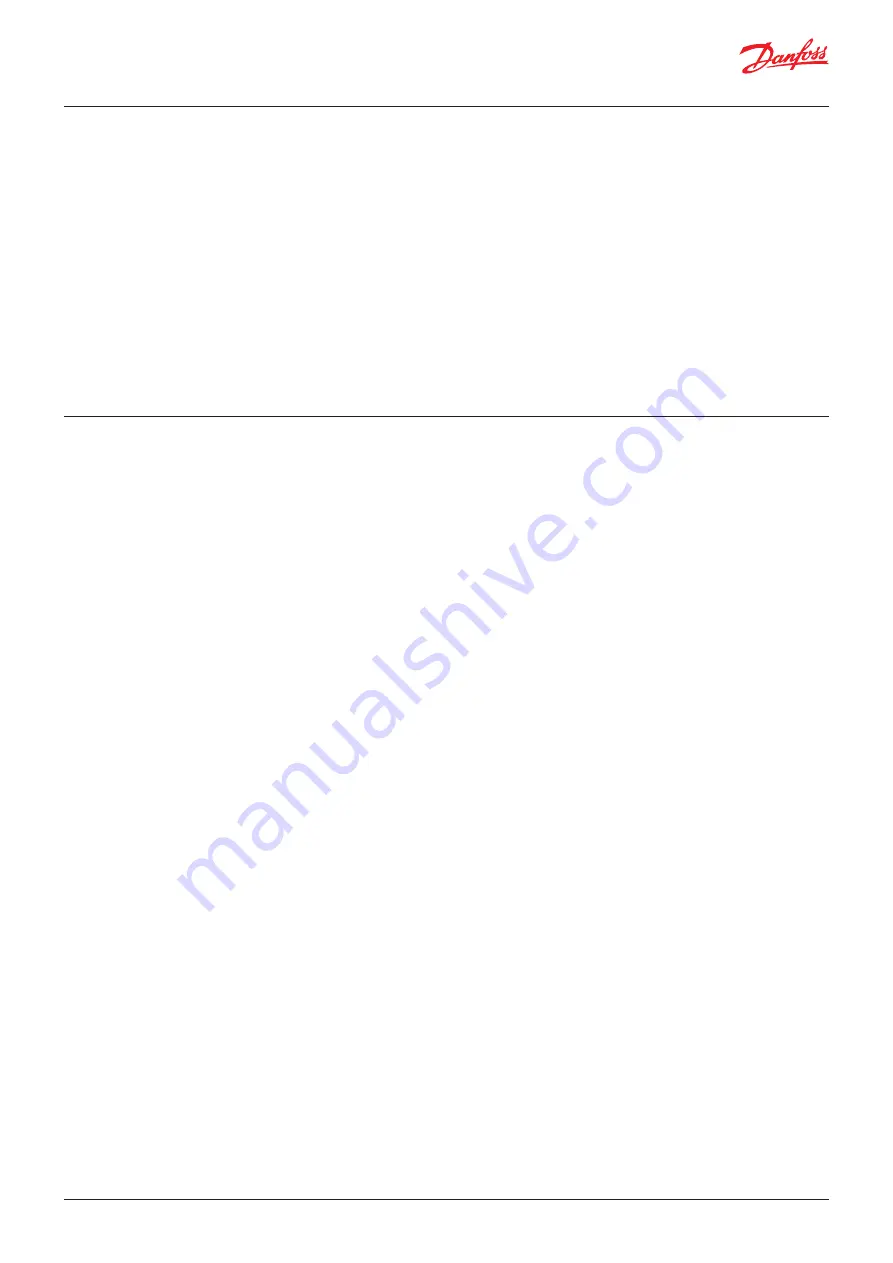
User Guide
|
Plate Type Heat Exchangers, Single plate & Semi-welded - Installation, Commissioning and Maintenance
© Danfoss | DCS (ms) | 2019.07
BC172686461130en-000201 | 19
Troubleshooting
(Continued)
Gasket failures are generally a result of
• Material aging/degradation
• Excessive exposure to ozone
• High or low operating temperature - outside
specified material limits
• Exposure to pressure surges
• Attack by chemicals from cleaning, refrigerants
or oils
• Physical damage from incorrect assembly work
• Misaligned plates (check the hanging system
at the top of the plate for distortion)
Decrease in performance is generally a result of
• Plate surfaces require cleaning or de-scaling
• Pumps or associated controls failing
• Plate channels blocked
• Liquid flows not as specified
• Associated chiller / cooling tower / boiler under
sized or dirty
• Cooling fluid temperature to the plate heat
exchanger is higher than the design
temperature
• Heating fluid temperature to the plate heat
exchanger is lower than the design temperature
• Refrigerant trap broken or jammed – unit
becomes filled with condensate
• Plate package has been assembled incorrectly
• Plate heat exchanger is running with co-current
flow, instead of counter-current. (Check
direction of pump flows)
• Air trap has developed in the plate package or
piping work
Ordering parts
When ordering spare parts it is important to
provide correct data for:
• Project and order number
• Plate heat exchanger type and manufacturing
number (see name plate)
• Required parts
When ordering separate plates it is important
that the correct plate code index and type of
plate is given.
When ordering separate gaskets it is important
to indicate the correct gasket material.
When ordering tie bolts, the existing bolts
should be measured in order to get spare bolts
with the same dimensions.
Modifications to the heat exchanger
Please note that a plate heat exchanger is specific
designed and built for the operating parameters
(pressures, temperatures, capacity and type of
fluids) initial provided by the customer.
If the plate heat exchanger needs to operate at a
different capacity this can be achieved by adding
or removing plates/cassettes.
Modification of the plate heat exchanger to
match other parameters may also be considered.
Consult Danfoss for redesign and/or approval of
any change to operating parameters.
After approval by Danfoss a new name plate will
be issued.
You may only commission a plate heat exchanger
under modified conditions after written approval
by Danfoss.
After sales service