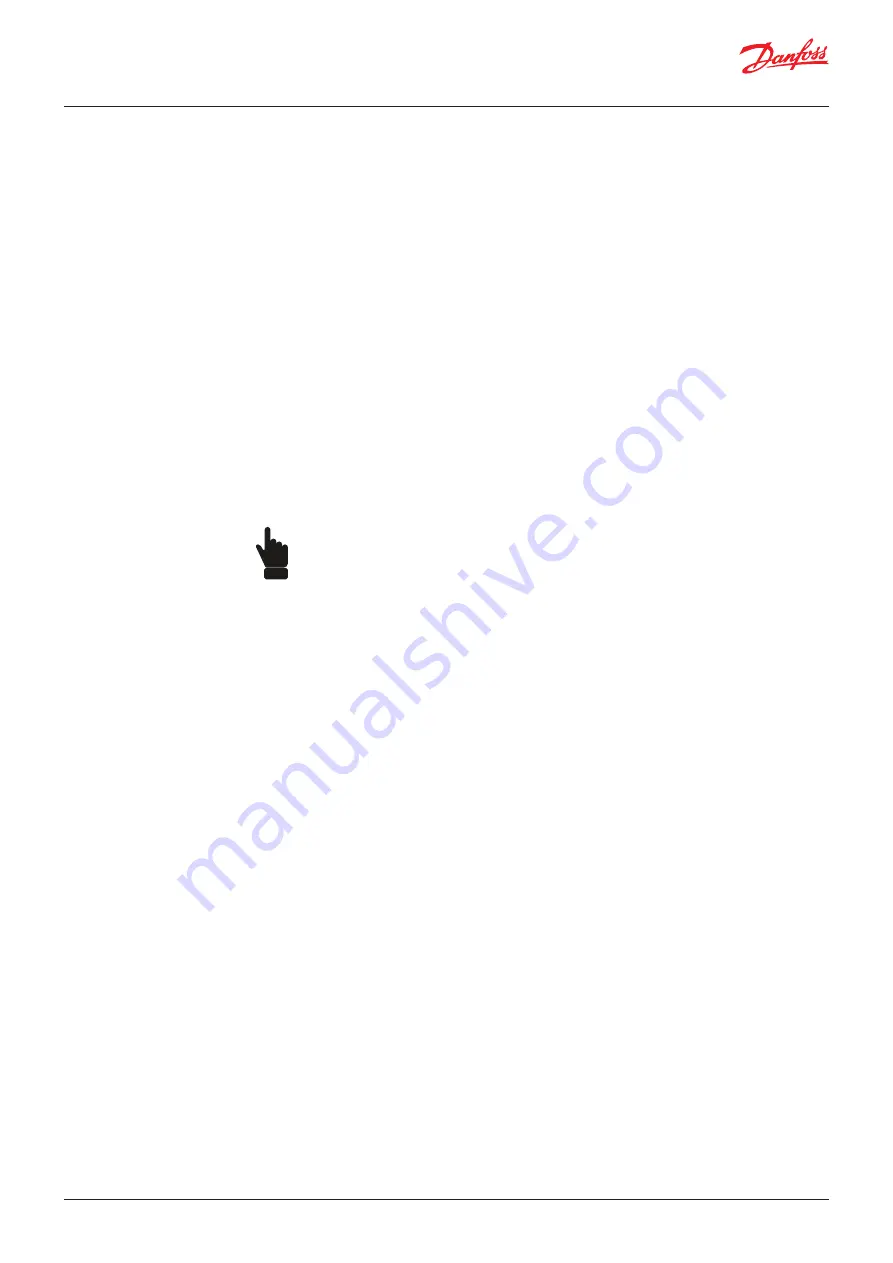
User Guide
|
Plate Type Heat Exchangers, Single plate & Semi-welded - Installation, Commissioning and Maintenance
10 | BC172686461130en-000201
© Danfoss | DCS (ms) | 2019.07
Piping system
Filtration
If the fluid in the plate heat exchanger
contains particles larger than Ø0.5mm an inline
filter should be fitted.
Installing the pipe connections
Most plate heat exchangers are intended for
counter-current flow directions, but some
specific applications require co-current flow.
Refer to name-plate for information on each
specific plate heat exchanger.
Danfoss plate type heat exchangers are
provided with various connection types
depending on size, application and
conditions.
Single plate
heat exchangers come with
threaded pipe connections or studded
flanges ready for counter/blind flanges.
Semi-welded
heat exchangers come with
factory installed welding flanges. The
refrigerant side is hermetically closed by blind
plates and pressurized with nitrogen.
Before connecting any piping to the
plate heat exchanger make sure to
clean and flush the piping system
thoroughly for any foreign objects.
When connecting the piping system to
the plate heat exchanger make sure
that the piping system does not subject
the plate heat exchanger to stress or
strain.
Make sure that the piping system,
connected to the plate heat exchanger,
is secured against pressure peaks/
surges and temperature shocks!
When doing any welding in the flange/
valve/piping system make earthing to
the piping opposite of the plate heat
exchanger. Never use the heat
exchanger for earthing as plates and
gaskets might be severely damaged.
When fitting threaded pipe to the
threaded plate heat exchanger
connection make sure that the
connection do not rotate during
tightening as this might damage
internal ring gaskets. A secure
counter-hold is needed.
For studded flange connection, insert
the gaskets before bolting the blind
flanges to the end plate. Tighten the
bolts evenly - do not over-tighten as
this might damage bolts/threads.
Note:
• Identify actual flow inlets/outlets on the name
plate before commencing piping work
• Heavy piping should be supported. This will
prevent heavy forces on the plate heat
exchanger
• To be able to open/close and dismantle the
plate heat exchanger shut off valves should
be installed in all connections
• Remove flanges from the plate heat exchanger
before connecting to the valve/piping system.
• Nitrogen pressurized refrigerant side must be
depressurized through the small valve in the
blind plate before removing the flanges
• Always install flexible connections on the
follower to prevent vibrations on the plate heat
exchanger. The flexible connections also help
prevent expansion of the pipes, which could
be caused by temperature influence
• Flexible connections must be fitted
perpendicular to the header/follower
• Install vents on both sides of the plate heat
exchanger
• The vents should be fitted on the highest point
in the direction of the media flow
• The installation must be fitted with safety
valves according to current pressure vessel
regulations