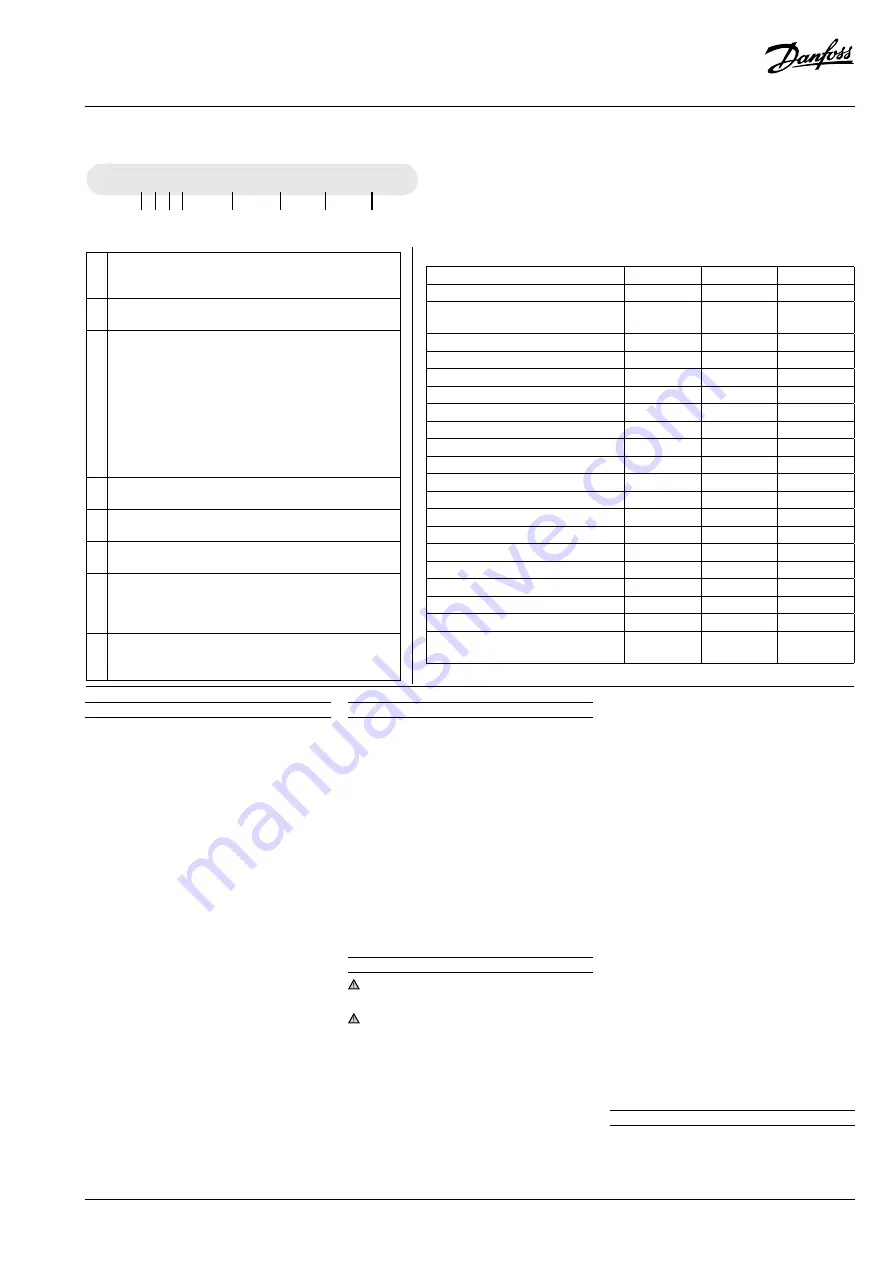
OP - MPXM 034 ML P00 G
1 2 3 4
5
6
7
8
1 Application
M = MBP
L = LBP
2 Package
Condensing unit family: P = Optyma™ Plus
3 Refrigerant
H = R404A/R507
G = R134a, R513A
Q = R452A, R404A/R507
X = R404A/R507, R134a, R407A, R407F, R448A, R513A
R449A,R452A
Y = R404A/R507, R449A
B = R448A/R449A/R404A/R452A (MBP)
P = R448A/R449A, R407A/F, R404A/R507
O = R448A/R449A/R404A/R452A (LBP)
4 Condenser
M = Microchannel heat condenser
5 Swept volume
Displacement in cm
3:
Example 034 = 34 cm
3
6 Compressor platform
ML= Fixed speed scroll MLZ
7 Version
P00: Optyma™ Plus
P02: Optyma™ Plus with Liquid Injection
P05: Optyma™ Plus with Supply monitoring relay
8 Voltage code
G = 230V/1-phase/50Hz compressor & fan
E = 400V/3-phase/50Hz compressor & 230V/1-phase fan
Optyma™
Plus
(P00)
(P02)
(P05)
IP level
IP54
IP54
IP54
Compressor technology
Scroll/
Reciprocating
Scroll
Scroll (3phase)
Control box (pre-wired E-panel)
yes
yes
yes
Microchannel condenser
yes
yes
yes
Fan speed controller*
yes
yes
yes
Main switch (circuit breaker)
yes
yes
yes
Supply monitoring relay
-
-
yes
Filter drier (flare connections)
yes
yes
yes
Sight glass
yes
yes
yes
Crankcase heater
yes
yes
yes
HP/LP adjustable pressostat
Electronic
Electronic
Electronic
Fail safe mini-pressostat
Mechanical
Mechanical
Mechanical
Access door(s)
yes
yes
yes
Acoustic insulation
yes
yes
yes
Condensing unit electronic controller
yes
yes
yes
Network connectivity
yes
yes
yes
Stack mounting
yes
yes
yes
Discharge gas thermostat
yes
yes
yes
HP/LP Alarm
yes
yes
yes
Liquid injection kit, phase loss/
sequence protection
-
yes
-
Version control
Designation system for the
Optyma
™ Plus range
* Inbuilt function within Condensing unit electronic controller
Instructions
118U3276G - AN18658643414604-001701 | 3
© Danfoss | Climate Solutions | 2022.02
1 – Introduction
These instructions pertain to Opty-
ma
™
Plus condensing units OP-MPYM,
OP-MPXM, OP-MPGM, OP-LPQM, OP-LPOM & OP-
MPBM used for refrigeration systems. They pro-
vide necessary information regarding safety and
proper usage of this product.
The condensing unit includes following:
• Microchannel heat exchanger
• Reciprocating or scroll compressor
• Receiver with stop valve
• Ball valves
• Sight glass
• High & low pressure switches
• Replaceable filter drier
• Electronic controller
• Main circuit breaker (Main switch with overload
protection)
• Fan and compressor capacitors
• Compressor contactor
• Supply monitoring relay**
• Robust weather proof housing
• Liquid injection controller (Module B Plus)*
• Electronic expansion valve (ETS6)*
*Only for P02 version,
**only for P05 models
2 – Handling and storage
• It is recommended not to open the packaging
before the unit is at the final place for installa-
tion.
• Handle the unit with care. The packaging al-
lows for the use of a forklift or pallet jack. Use
appropriate and safe lifting equipment..
• Store and transport the unit in an upright posi-
tion.
• Store the unit between -35°C and 50°C.
• Don’t expose the packaging to rain or corrosive
atmosphere.
• After unpacking, check that the unit is com-
plete and undamaged.
3 – Installation precautions
Never place the unit in a flammable atmos-
phere.
Place the unit in such a way that it is not bloc-
king or hindering walking areas, doors, windows
or similar.
• Ensure adequate space around the unit for air
circulation and to open doors. Refer to picture
1 for minimal values of distance to walls.
• Avoid installing the unit in locations which are
daily exposed to direct sunshine for longer pe-
riods.
• Avoid installing the unit in aggressive and dus-
ty environments.
• Ensure a foundation with horizontal surface
(less than 3° slope), strong and stable enough
to carry the entire unit weight and to eliminate
vibrations and interference.
• The unit ambient temperature may not exceed
50°C during off-cycle.
• Ensure that the power supply corresponds to
the unit characteristics (see nameplate).
• When installing units for HFC refrigerants, use
equipment specifically reserved for HFC refri-
gerants which was never used for CFC or HCFC
refrigerants.
• Use clean and dehydrated refrigeration-grade
copper tubes and silver alloy brazing material.
• Use clean and dehydrated system components.
• The suction piping connected to the compres-
sor must be flexible in 3 dimensions to dampen
vibrations. Furthermore piping has to be done
in such a way that oil return for the compres-
sor is ensured and the risk of liquid slug over in
compressor is eliminated.
4 – Installation
• The installation in which the condensing unit is
installed must comply to pressure Equipment
Directive (PED) 2014/68/EU. The condensing unit