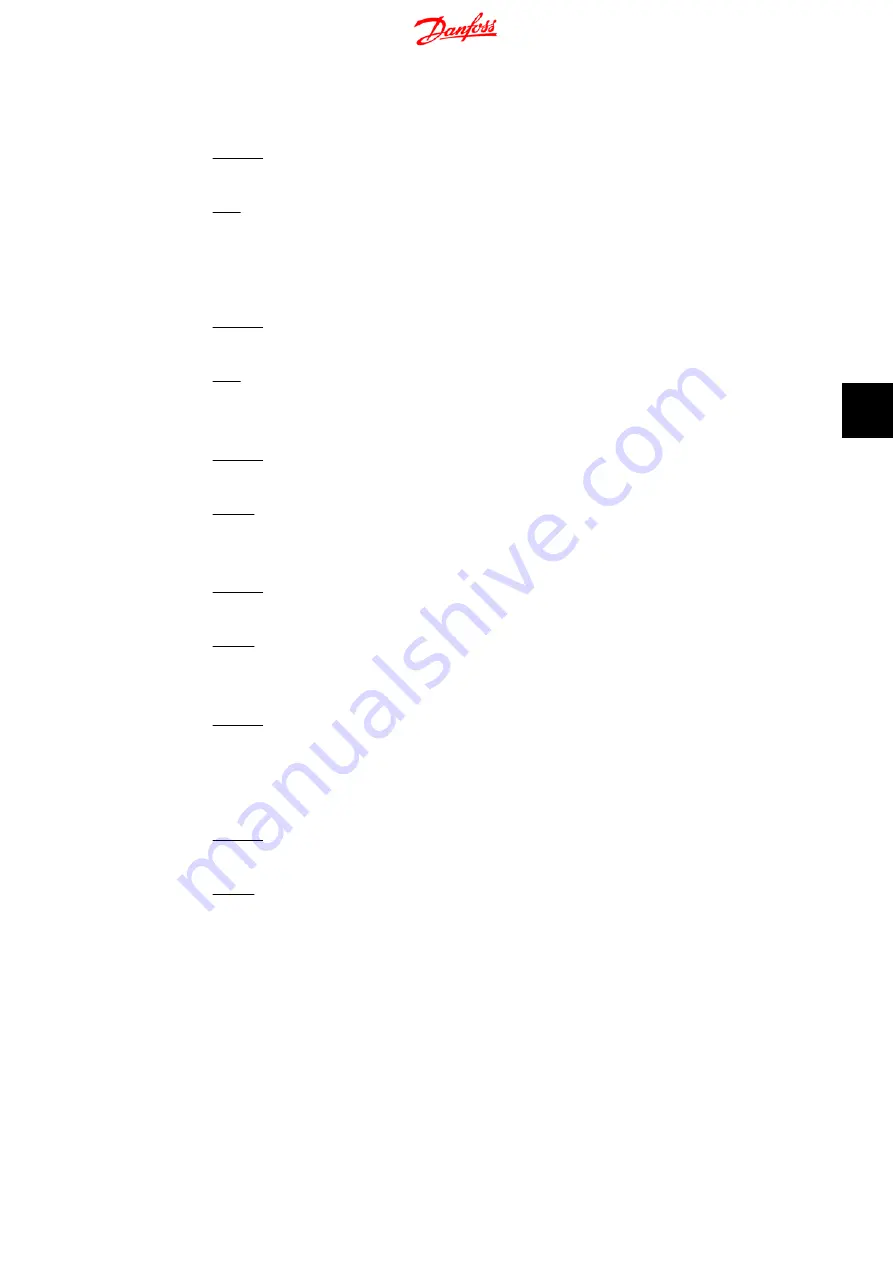
P19-93 - 4: Positive software limit ex-
ceeded
Meaning
A motor command will cause / has caused the software limit switch to be activated. The maximum
limit is specified in P744.
Note
Before the error can be cleared the application must be moved back from the limit. If “power
recovery” is enabled in P736, this can be done through an error reset and a negative jog (input
54).
P19-93 - 5: Negative software limit ex-
ceeded
Meaning
A motor command will cause / has caused the software limit switch to be activated. The minimum
limit is specified in P745.
Note
Before the error can be cleared the application must be moved back form the limit. If “power
recovery” is enabled in P736 this can be done through an error reset and a positive jog (input 53).
P19-93 - 6: VLT not running
Meaning
The motor was not magnetised in a situation where it should have been. The electromechanical
brake is immediately activated in this case regardless of the settings in P718 and P725.
Causes
While the motor was holding/driving the load, the drive either tripped, connection to terminal 27
was lost, or the
[STOP]
button was pressed on the LCP.
P19-93 - 7: Brake wear limit exceeded
Meaning
This error message is given if the drive has moved more than the allowed number of user units
specified in P735
while
the electronic brake was activated.
Causes
The mechanical brake is worn and should be replaced in the near future or the limit specified in
P735 is too low.
P19-93 - 8: Quick stop input activated
Meaning
The quick stop input has been activated. As a safety precaution of the electromechanical brake is
activated according to the setting of P725 and the drive is coasted regardless of the setting of
P715. Normal operation is resumed if the error is cleared.
P19-93 - 9: Controller (PID) tracking er-
ror too big
Meaning
The difference between the desired set-point position and the actual position read via the encoder
feedback has exceeded the limit specified in P726.
Causes
Several reasons may exist:
1.
The encoder is not properly connected. Check the encoder connection.
2.
The encoder is counting positive in the wrong direction. Switch A and B channels if nec-
essary.
3.
The PID controller settings are not properly optimised. Follow the instructions for opti-
mising.
4.
The limit specified in P726 may be too low.
MCO351 Positioning Controller
6. Troubleshooting
MG.33.R1.02 - VLT
®
is a registered Danfoss trademark
43
6