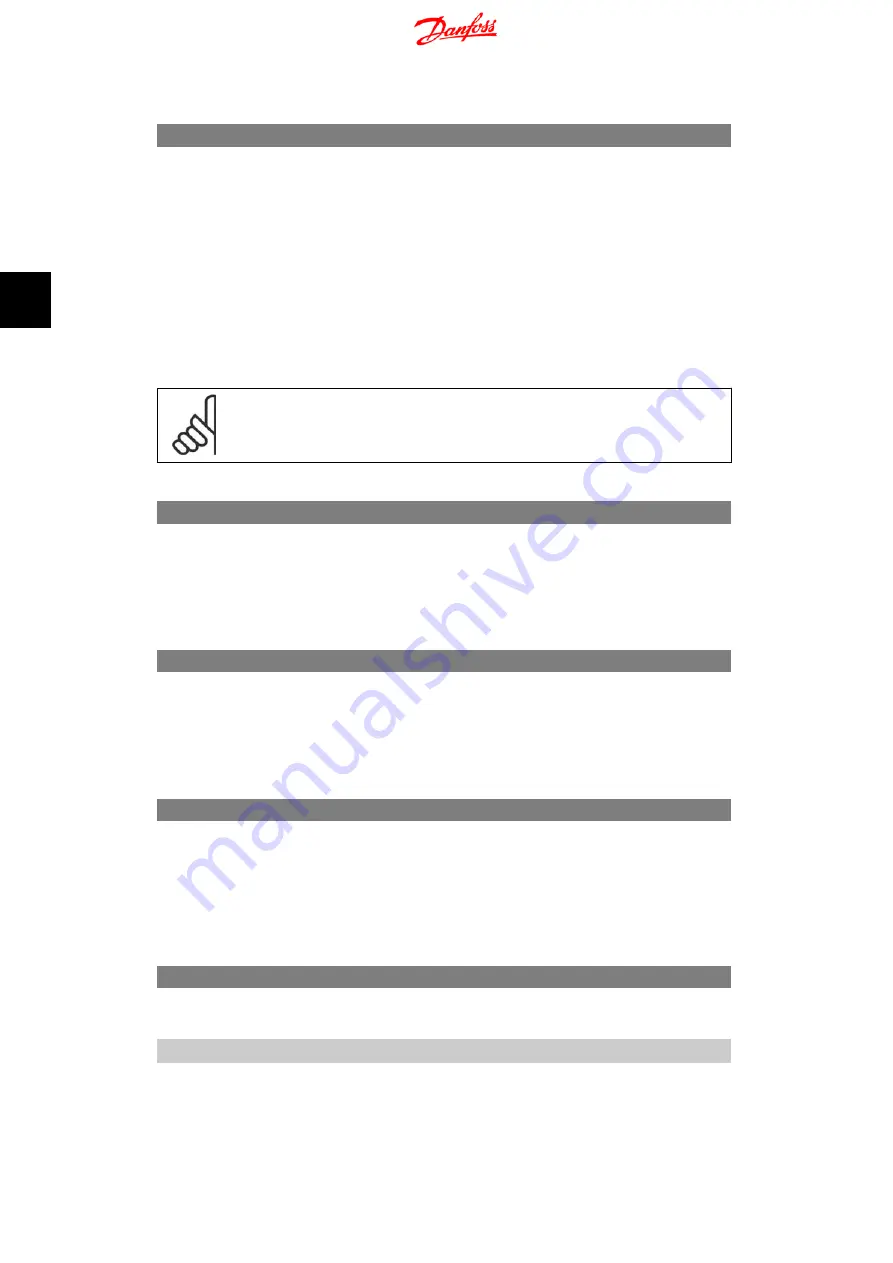
32-67 Maximum tolerated PID error
Range:
Function:
20,000
qc
*
[1...1,073,741,823
qc]
The PID track error is defined as the difference between the
internal controller set-point and the actual position. The better
tuning of the PID controller (par. 32-60 to 32-66) the lesser the
PID track error.
At every sample time the current track error is compared with
the setting of par. 32-67. It is defined as an error situation (“PID
track error too big” - par. 19-93 = 9) if the track error is bigger
than the setting of par. 32-67. After tuning the PID controller
optimally this parameter should be set to a value approx. 50 %
larger than the maximum observed value of par. 34-56.
NB!
The unit is quad-counts (QC) not user units (UU).
32-69 PID sample interval
Range:
Function:
1 ms
*
[1...1000 ms]
The sampling frequency of the controller can be adjusted in this
parameter. Normally, the fastest possible setting (1 ms) is pref-
erable, but in cases with low resolution of the feedback signal it
is a good idea to set this parameter at a slightly higher value.
32-80 Maximum allowed velocity
Range:
Function:
1,500
ERPM
1
*
[1 … 100,000 ERPM] When performing a FFVEL autocalculation, the maximum ve-
locity allowed is calculated on the basis of par. 303, par.19-14,
par. 19-15 and the result is presented in this parameter.
32-81 Quick ramp time
Range:
Function:
1,000
ms
*
[50...3600000 ms]
The quick ramp time is defined as the time to ramp down from
the maximum velocity to standstill. The quick ramp time is used
when the quick stop function is activated or an error has occur-
red.
32-82 Ramp type
Option:
Function:
[0]
*
Linear
This parameter MUST be set to 0 for the Positioning Controller.
[1]
*
S-Ramp
4. Programming
MCO351 Positioning Controller
30
MG.33.R1.02 - VLT
®
is a registered Danfoss trademark
4