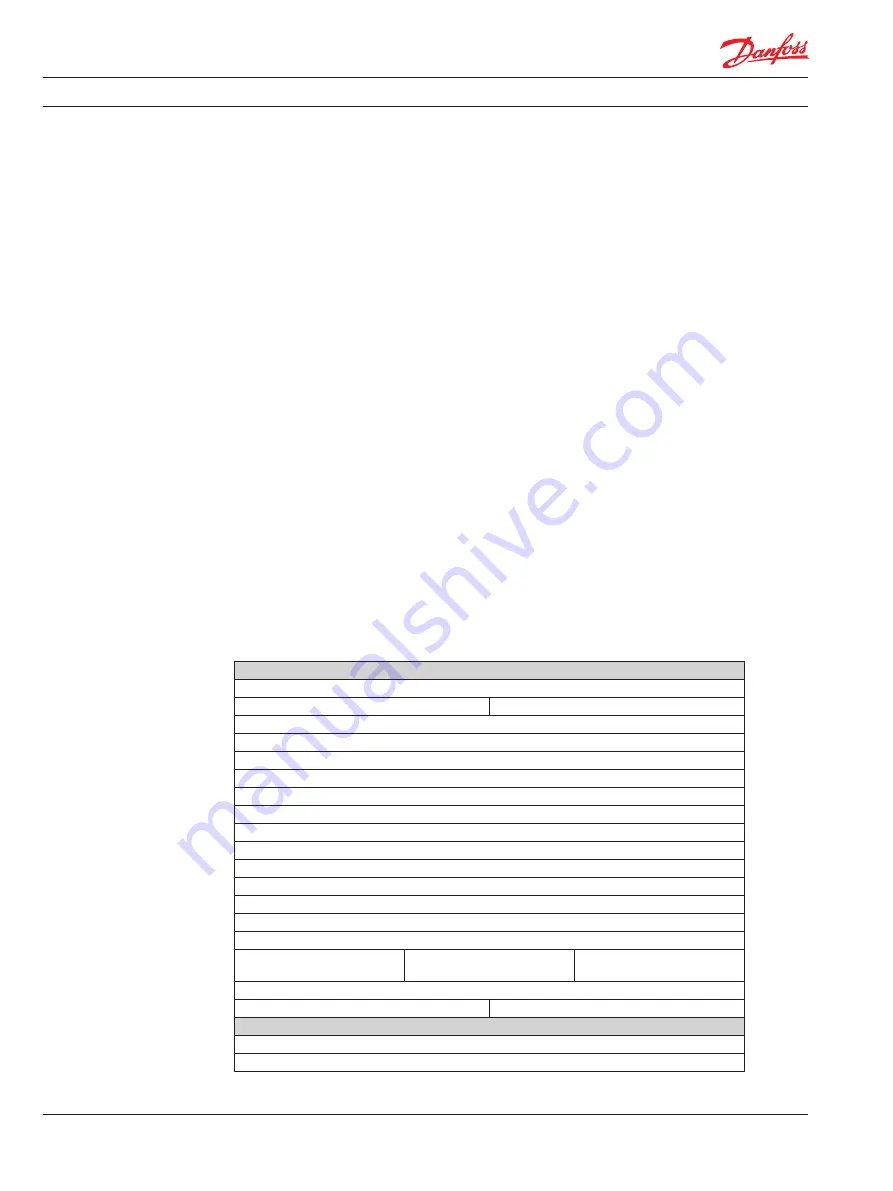
Technical Information
KPP PPU
11029257
• Rev BB • July 2013
4
Description
Features
Product Overview
Technical Data
Electrical and Environmental Data
Electrical
Supply voltage (two ranges)
Regulated 4.5 to 8.5 Vdc
Battery 7 to 32 Vdc
Maximum operating current
20 mA at 1 Hz and 5 Vdc supply
Required current
12 mA at 5 Vdc (no load)
Output voltage in high state
Supply voltage minus 0.5 Vdc minimum (no load)
Output voltage in low state
0.5 Vdc, maximum (no load)
Maximum frequency
15 kHz
Load
15 kΩ to both ground and supply
Peak transient voltage
80 Vdc for 2 milliseconds,
4.5 to 8.5 Vdc models
300 Vdc for 2 milliseconds,
7 to 32 Vdc models
200 Vdc for 100 milliseconds,
7 to 32 Vdc models
Peak reverse voltage
-15 Vdc continuous, 4.5 to 8.5 Vdc models
-32 Vdc continuous, 7 to 32 Vdc models
Environmental
Operating and storage temperature
-40° to 110° C [-40° to 230° F]
The KPP pulse pickup accepts a supply voltage and, in response to the speed of a permanently
magnetized speed ring on the motor’s cylinder block or shaft, outputs a digital pulse signal. The
output changes its high/low state as the north and south poles of the speed ring pass by the sensor’s
face. Because the output is digital, the KPP is ideal for low-speed measurement.
The KPP is designed for rugged outdoor, mobile, or heavy industrial speed-sensing applications that
do not allow contact with the rotating shaft. It is custom-designed for Sauer-Danfoss pumps and
motors.
y
Choice of directional or non-directional devices
y
Choice of Delphi/Packard Weather-Pack®, Turck Eurofast® or Deutsch® connectors
y
Rugged housing designed to withstand extreme environments
y
You can order pre-mounted in Sauer-Danfoss pumps and motors
y
You can use with digital or analog controllers
y
Suitable for zero speed measurements