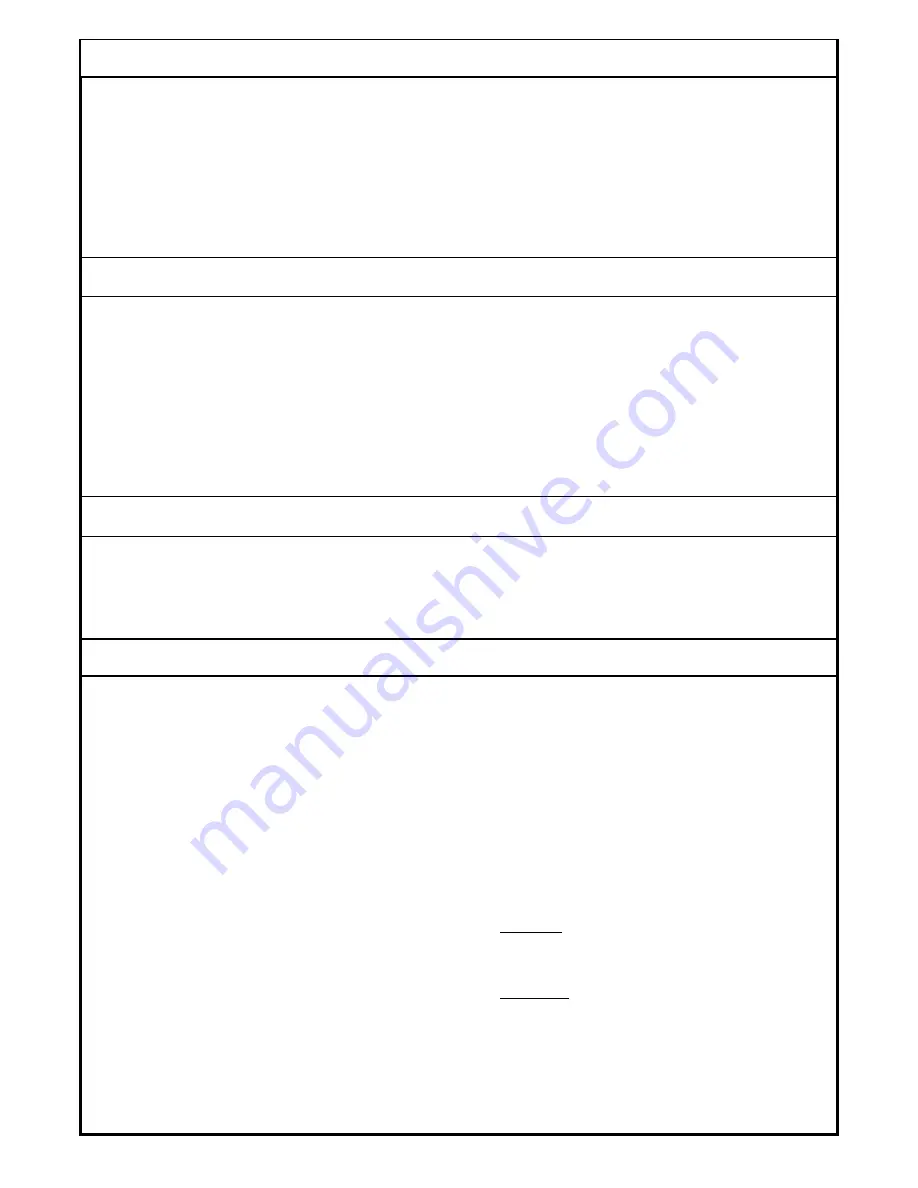
6
CORRECTIVE ACTION FOR UNINTENDED OPERATION
123456789012345678901234567890121234567890123456789012345678901212345678901234567890123456789
123456789012345678901234567890121234567890123456789012345678901212345678901234567890123456789
1 23456789012345678901234567890121234567890123456789012345678901212345678901234567890123456789
1 23456789012345678901234567890121234567890123456789012345678901212345678901234567890123456789
1 23456789012345678901234567890121234567890123456789012345678901212345678901234567890123456789
123456789012345678901234567890121234567890123456789012345678901212345678901234567890123456789
WARNING
Automatic controls produce actuator drive signals which may
not be anticipated by the persons near the controlled machine
element. Caution should be excercised and appropriate
warning labels affixed.
Road Sentry control failures can produce errors in machine
motion and in displayed information. Unintended motion can
result, which may cause erratic movements or no machine
movement. Unintended motion is a potentially unsafe
situation.
Unintended operation of the electrical control system can
result from failure of the controller, sensor or wiring. Unintended
operation can occur without any input from the operator or
can occur because the operator reacts to an incorrect message
from the displays. Unintended operation which is not corrected
may result in small errors or in continuous travel of controlled
cylinders.
1. Switch the console control to “manual.” This will stop
operation of the controller if the fault is in the sensor or
due to an incorrect input signal by the operator. This may
not correct controller faults and will not correct valve
wiring faults.
2. Turn off controller power. This will defeat controller or
sensor faults but not all wiring faults to the valves.
Ground switched valves would be particularly isolated
from this corrective action, as they are normally powered
separately from the controller.
3. Switch off the power supply to the valves. This will
prevent machine motion under all circumstances,
provided the power supply is switched close enough to
the battery to prevent any shorts to power.
THEORY OF OPERATION
The KGS console receives information from sensors mounted
on the machine and produces an electrical valve drive to
move positioning cylinders in a closed loop. Control logic is
determined by built-in software and by instructions received
from the operator’s use of switches. Continuous operating
information is provided to the operator with displays which
are continuously monitoring the sensor and controllers.
Information is communicated between the left side and the
right side via a CAN network.
CONSOLE INTERFACE PANEL
The console interface panel has eight switches and one or
two displays to allow information to be transmitted between
the operator and the machine. See the Operator Console
Panel Diagram. There are dedicated, labelled switches for
the frequently used functions. One display provides setting
information as well as special messages, and one display
provides continuous control status information. There is an
audible alarm to assist in setup and diagnostics. An optional
backlight is available. Displays and switches are further
described on following page.
SETTING/MESSAGE DISPLAY
The eight character alphanumeric display in the center
of the console is used for displaying the setpoint position,
actual position, sensitivity setting, display offset and
fault messages. Some messages are more than eight
characters in length and are displayed by scrolling the
message across the screen. See the Setting Message
Display Diagram.
STATUS DISPLAY
The upper left LED array displays an arrow indicating the
error between setpoint and actual machine position. A
full up arrow indicates 1 inch error below setpoint, a full
down arrow indicates 1 inch error above setpoint, and a
flat line indicates no error. There are also four gradations
between full on and off. See the Status Display Diagram.
GRADE/SLOPE SWITCH
Pressing the grade/slope switch selects the sensor to be
used for automatic control.
SETPOINT/ACTUAL SWITCH
Pressing the setpoint/actual switch selects the display of
either the setpoint machine position or actual position.
AUTO/MANUAL SWITCH
Pressing the auto/manual switch selects either auto or
manual control. In auto mode, the toggle switch changes
the setpoint.
For pavers: In manual control, the toggle switch functions
as a jog switch. For pavers, this does not affect the
setpoint; changing from manual mode to auto mode
returns the controller to its previous setpoint.
For planers: Auto mode is exited when the toggle is
activated and the toggle switch functions as a jog switch.
For planers, the setpoint is established at the new
machine position when “auto” is pressed.
UP/DOWN TOGGLE SWITCH
The toggle switch changes machine position in both
auto and manual mode. In auto mode, the up/down