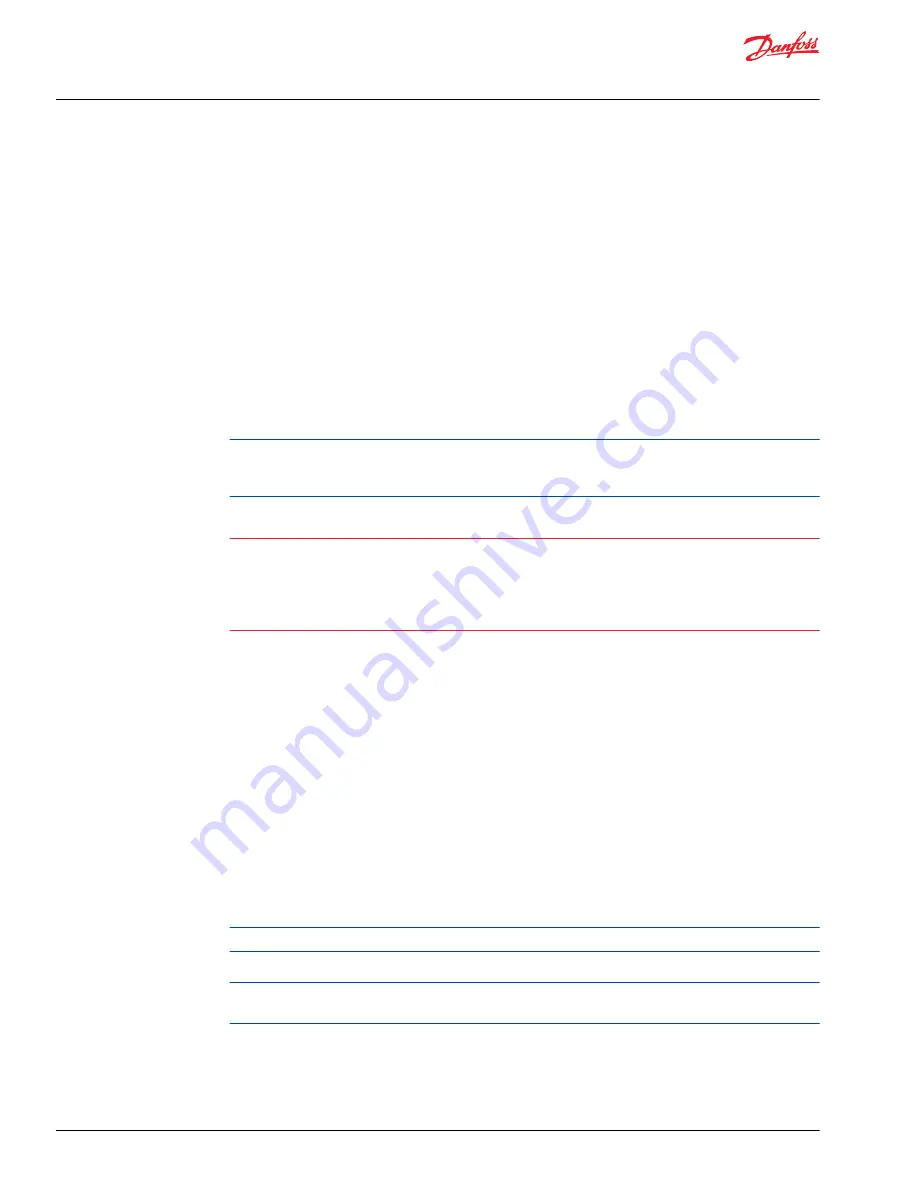
Input speed
Minimum speed is the lowest input speed recommended during engine idle condition. Operating below
minimum speed limits the pump’s ability to maintain adequate flow for lubrication and power
transmission.
Rated speed is the highest input speed recommended at full power condition. Operating at or below
this speed should yield satisfactory product life.
Maximum speed is the highest operating speed permitted. Exceeding maximum speed reduces product
life and can cause loss of hydrostatic power and braking capacity. Never exceed the maximum speed
limit under any operating conditions.
Operating conditions between Rated and Maximum speed should be restricted to less than full power
and to limited periods of time. For most drive systems, maximum unit speed occurs during downhill
braking or negative power conditions.
For more information consult
Pressure and speed limits, BLN-9884
, when determining speed limits for a
particular application.
During hydraulic braking and downhill conditions, the prime mover must be capable of providing
sufficient braking torque in order to avoid pump over speed. This is especially important to consider for
turbocharged and Tier 4 engines.
W
Warning
Unintended vehicle or machine movement hazard
Exceeding maximum speed may cause a loss of hydrostatic drive line power and braking capacity. You
must provide a braking system, redundant to the hydrostatic transmission, sufficient to stop and hold the
vehicle or machine in the event of hydrostatic drive power loss. The braking system must also be
sufficient to hold the machine in place when full power is applied.
System pressure
System pressure is the differential pressure between high pressure system ports. It is the dominant
operating variable affecting hydraulic unit life. High system pressure, which results from high load,
reduces expected life. Hydraulic unit life depends on the speed and normal operating, or weighted
average, pressure that can only be determined from a duty cycle analysis.
Application pressure is the high pressure relief or pressure limiter setting normally defined within the
order code of the pump. This is the applied system pressure at which the driveline generates the
maximum calculated pull or torque in the application.
Maximum working pressure is the highest recommended application pressure. Maximum working
pressure is not intended to be a continuous pressure. Propel systems with application pressures at, or
below, this pressure should yield satisfactory unit life given proper component sizing.
Maximum pressure is the highest allowable application pressure under any circumstance. Application
pressures above Maximum Working Pressure will only be considered with duty cycle analysis and factory
approval.
Pressure spikes are normal and must be considered when reviewing Maximum Working pressure.
Minimum low loop pressure must be maintained under all operating conditions to avoid cavitation.
All pressure limits are differential pressures referenced to low loop (charge) pressure. Subtract low loop
pressure from gauge readings to compute the differential.
Servo pressure
Servo pressure is the pressure in the Servosystem needed to position and hold the pump on stroke. It
depends on system pressure and speed. At minimum servo pressure the pump will run at reduced stroke
depending on speed and pressure.
Service Manual
H1 Pumps 069/078, 089/100, 115/130, 147/165, 210/250
Operating parameters
18 |
©
Danfoss | May 2018
520L0848 | AX00000087en-US0308