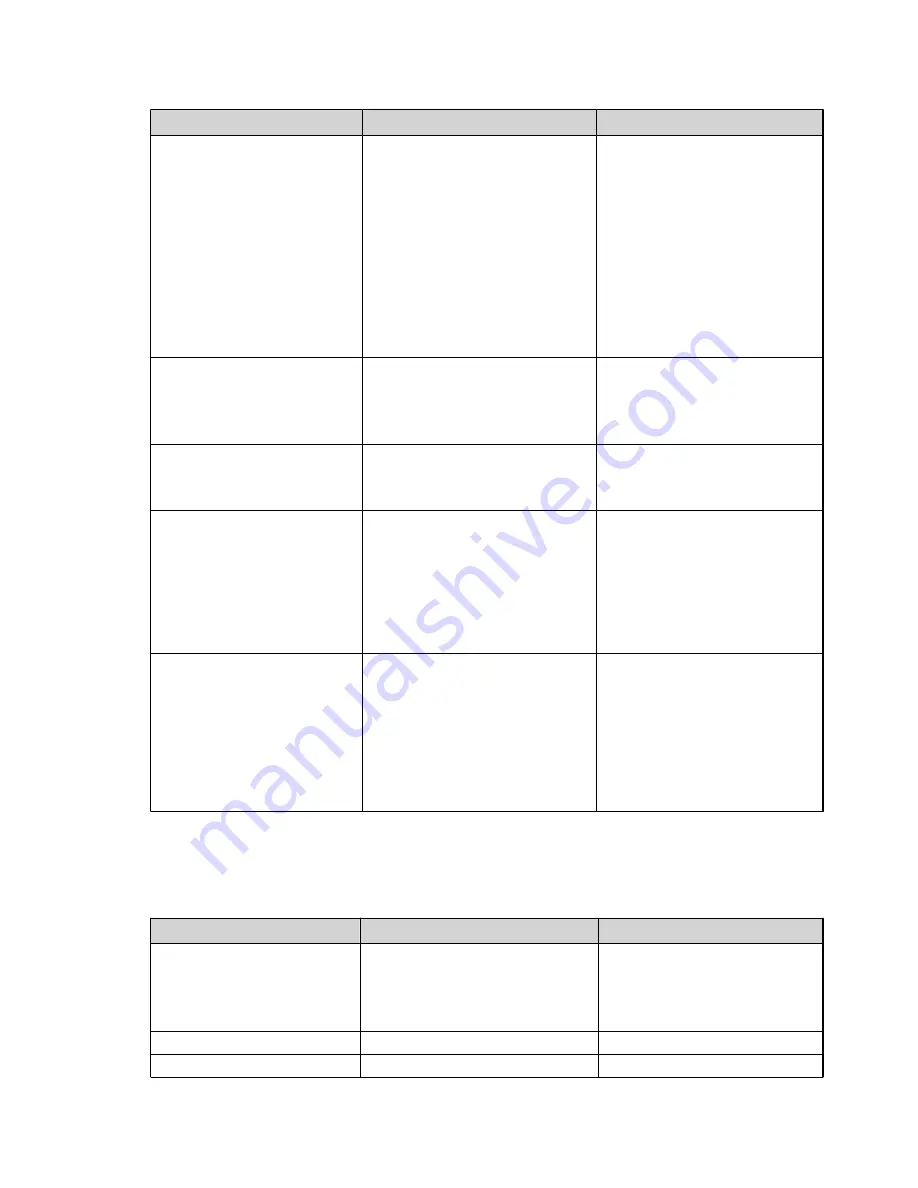
Table 23.
Problem – Operating pressure switch open alternatively high hot gas temperature
Cause
Troubleshooting
Remedy
1. Operating pressure switch, func-
tion.
1.
Switch off the main switch for the
heat pump, wait until the com-
pressor has been stationary for at
least 15 minutes.
2.
Disconnect the two cables on the
pressure switch, using a buzzer
check if the pressure switch is
closed.
If the pressure switch is closed, bridge
the pressure switch cables temporarily
and switch on the voltage to the heat
pump again. If there is an indication 0
(zero) in the display this means that the
pressure switch is fault-free and the
problem is in the wiring or in the circuit
board.
If the pressure switch is open, try care-
fully tapping the head of the pressure
switch with a screwdriver and use a buz-
zer test to see if it has closed again.
Replace the pressure switch if it appears
to jam repeatedly.
2. Sensor fault.
Check what the sensor shows. Is it a plau-
sible/actual value?
Measure the resistance of the sensor,
check against the ohm table in Measure-
ment points.
If the sensor is defective, replace it.
3. Hot gas temperature too high.
Check the set value on PRESS. PIPE in the
heat pump’s control computer (factory
setting 140
℃
)
The square symbol appears when the
delivery pipe temperature is as high or
greater than the set value for DELIVERY
PIPE.
4. Overheating too high.
Using manometer apparatus and ther-
mometer check what the overheating
reading of the unit is.
Also check that bulb and capillary tube are
undamaged and that the bulb is correctly
installed.
If the overheating reading does not cor-
respond with the instructions for the
specific refrigerant, adjust the expansion
valve until the correct value is obtained.
See separate instructions for cooling
techniques.
If overheating cannot be adjusted with
the expansion valve or if the capillary
tube/bulb is damaged, replace it.
5. Lack of refrigerant, not enough
refrigerant in the system.
Using manometer apparatus and ther-
mometer, check that the unit’s overheat-
ing is correct for the specific refrigerant.
Follow the correct procedure (depend-
ing on type of refrigerant) to add the cor-
rect amount of refrigerant.
If there appears to be a leak in the refrig-
erant circuit, carry out leak tracing and
any necessary corrective action. If leak
tracer is not available, brush soap water
on the suspected leak and look for bub-
bles. Also check for oil as this can come
out from the refrigerant circuit.
10.4.2
Leakage
Table 24.
Problem – Leak fluid side
Cause
Troubleshooting
Remedy
1. Insufficiently tightened connec-
tions.
Locate the leak.
•
Tighten the connection and check
that it is sealed.
•
If it is still not sealed, replace the
entire connection and support
sleeve (only at soft pipes).
2. Cracked nut or connection.
Locate the leak.
Replace nut or connection.
3. Defective gasket or O-ring.
Locate the leak.
Replace the gasket or O-ring.
Service instructions VMGFC302 – 45
Summary of Contents for DHP-A
Page 4: ......
Page 86: ...VMGFC302...