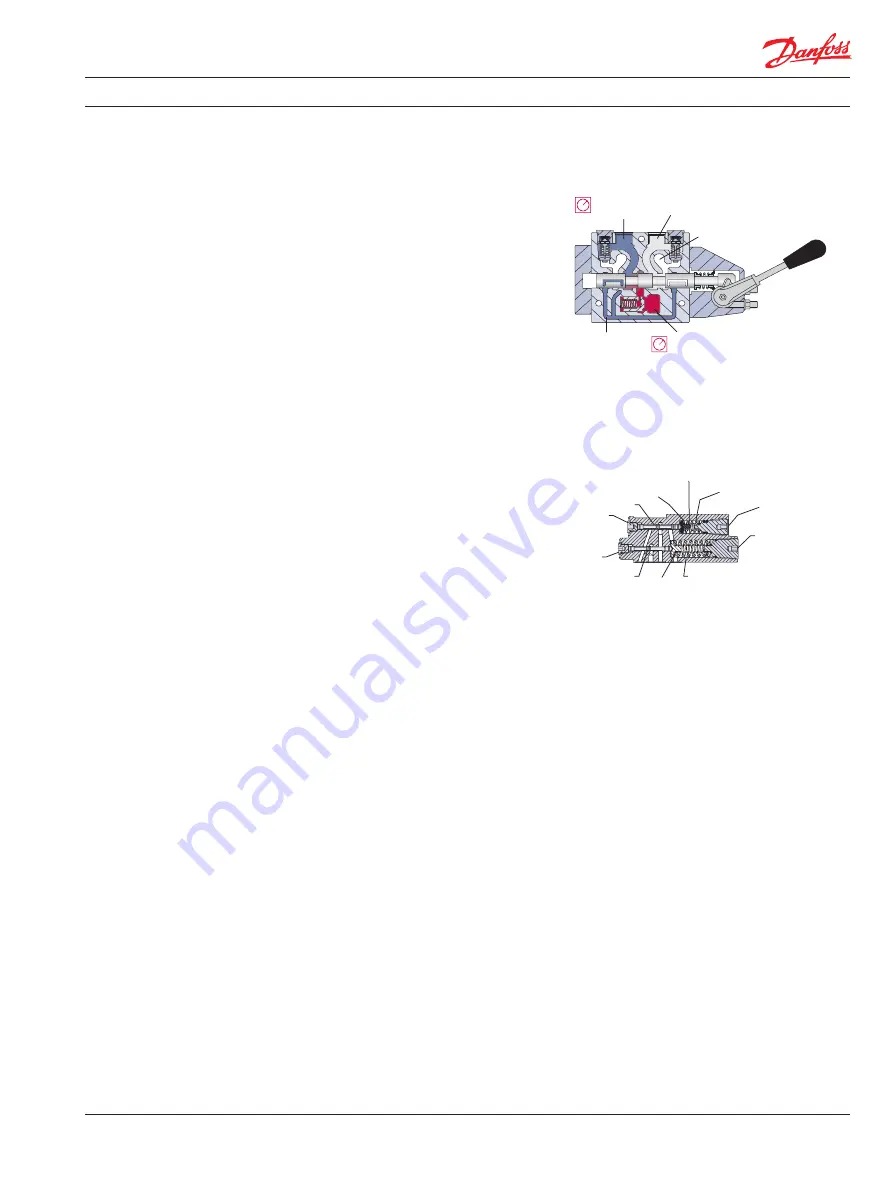
Service Manual
Series 45 J Frame Open Circuit Axial Piston Pumps
520L0607
• Rev AI • Sep 2013
13
Features (continued)
Control Options
(continued)
LS control
The LS control design matches pump flow with
system demand. The LS control senses the flow
demand of the system as a pressure drop across
the
E
xternal
C
ontrol
V
alve (ECV). As the ECV
opens and closes, the pressure delta across the
valve changes. When opening, the delta
decreases. When closing, the delta increases. The
LS control then increases or decreases pump
flow to the system until the pressure delta
becomes equal to the LS setting as defined by
the LS adjusting plug (7) and spring (8).
L oad
pressur e
L oad sense
pressur e
System
pressur e
T ank
Retur n
pressur e
P101 665E
Typical load-sensing control valve
Pressure drop across external control valve defines
system demand
The LS control consists of two spool valves that
connect the servo piston either to pump case or
system pressure. The PC spool (6) controls the
pressure-compensating function of the control
as previously described. The LS spool (9) controls
the load-sensing function. The PC spool has
priority over the LS spool.
Through internal porting, system pressure
(upstream of ECV) is applied to the non-spring
end of the LS spool, and through hydraulic line
connected at port X, LS pressure (downstream of
ECV) is applied to the spring end. This
arrangement allows the LS spool to act on the
delta between system pressure and LS pressure.
The LS spring sets the threshold of operation (LS
setting).
Because the swashplate is biased to maximum angle, the pump attempts to deliver full flow to the
hydraulic system. When the flow being delivered exceeds demand, the pressure delta across the ECV
is great enough to overcome spring force and shift the LS spool porting system pressure to the servo
piston. The pump de-strokes reducing flow until the delta across the ECV becomes equal to the LS
setting. When flow being delivered is less than demand, the delta across the ECV drops below the LS
setting and the LS spring shifts the spool connecting the servo piston to pump case. The pump
strokes increasing flow until the delta across the ECV becomes equal to the LS setting.
When the external control valve is placed in neutral, it connects the LS signal line to drain. With no LS
pressure acting on the non-spring end of the LS spool, the pump adjusts stroke to whatever position
necessary to maintain system pressure at the LS setting. The pump is now in standby mode.
Because of the series arrangement of the LS and PC spools, the PC spool will override the LS spool. If
at any time system pressure reaches the PC setting, the PC spool will shift blocking the passage that
connects the LS spool with the servo piston and porting system pressure to the servo piston causing
the pump to destroke.
LS spool shifts to port system pressure to servo
piston
Cross-section LS control
Spool
Spring
guide
Spring
LS adjusting
plug
LS spring
PC adjusting
plug
Plug
Plug
Spool
Spring
guide
Spring
(PC heavy)
P104 051