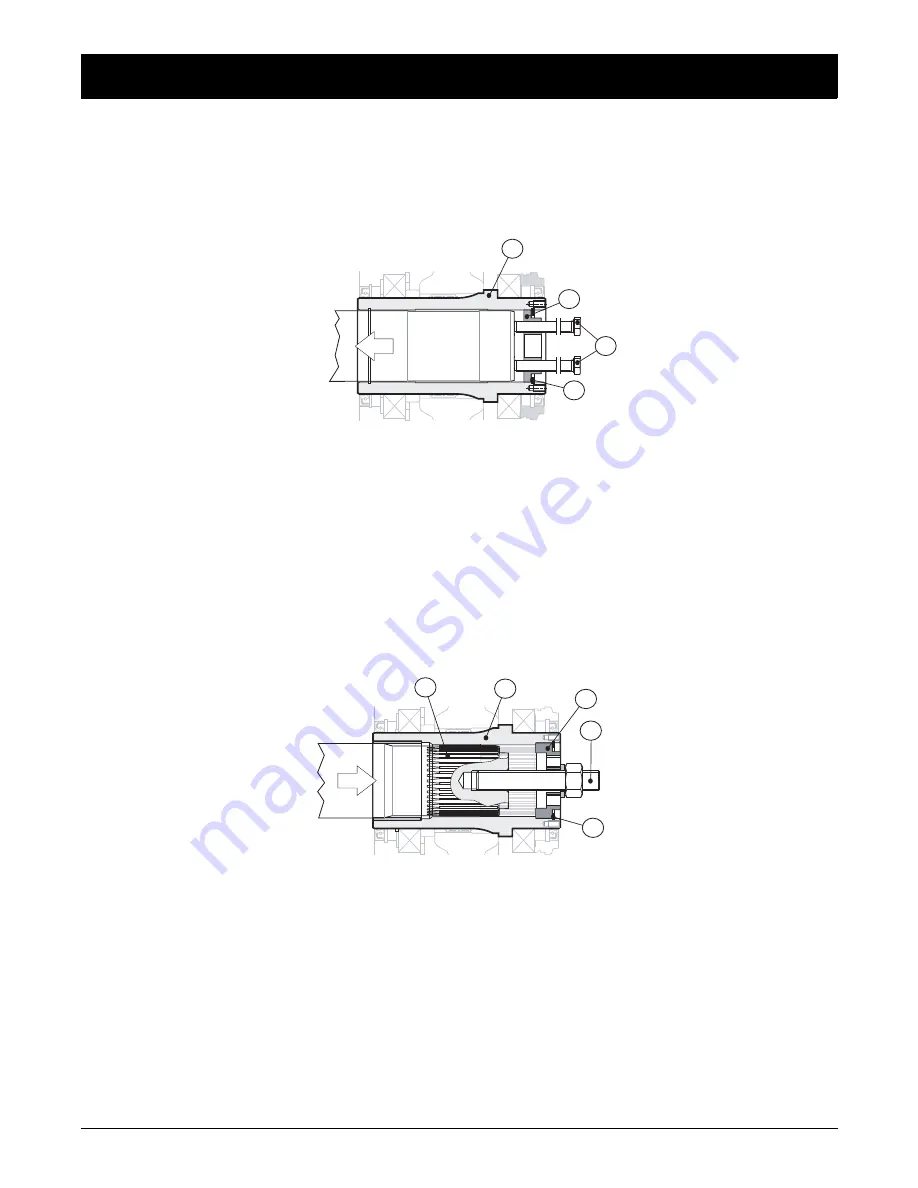
GEAR UNIT WITH “S” TYPE SHAFT
21
Dana Incorporated
IMM-0005EN Posiplan (MT-5215-0806)
Disassembly:
remove the anchor bolt (pos. 6) then the backplate(pos. 8) from their relative seats. Insert 2 bolts (pos. 7) into the two threaded
holes on the backplate (pos. 3) (pos. and screw them until they touch the machine shaft (pos. 1). Now give them alternately one
full turn each (see figure below).
GEAR UNIT WITH “S” TYPE SHAFT
Assembly:
align the axes of the gear unit female shaft (pos. 2) as much as possible with the machine male shaft (pos. 1), then bring the two
shafts together after aligning the connecting toothing. Slot them together without exerting too much pressure on each part.
To make sure the machine shaft rests tight against the backplate (pos. 3) to be subsequently fitted, use a threaded rod (pos. 4)
of an appropriate size.
Now insert the backplate (pos. 3) then the inner retaining ring (pos. 5) securing the backplate (pos. 3). Now when you tighten
the threaded rod nut, the machine shaft will abut with the backplate (see Fig.13).
Securing:
unscrew the threaded rod nut (pos. 4) and take it out of its seat. Replace the rod (pos. 4) with screw (pos. 6), torquing it down
fully to the torque value shown in "Values Table Torque Setting Bolts p. 32", using an intermediate threadlocker. Dana Incorpo-
rated recommends LOCTITE 601 (see Fig. 14).
Fig. 12
Fig. 13
2
5
3
7
5
1
2
3
4