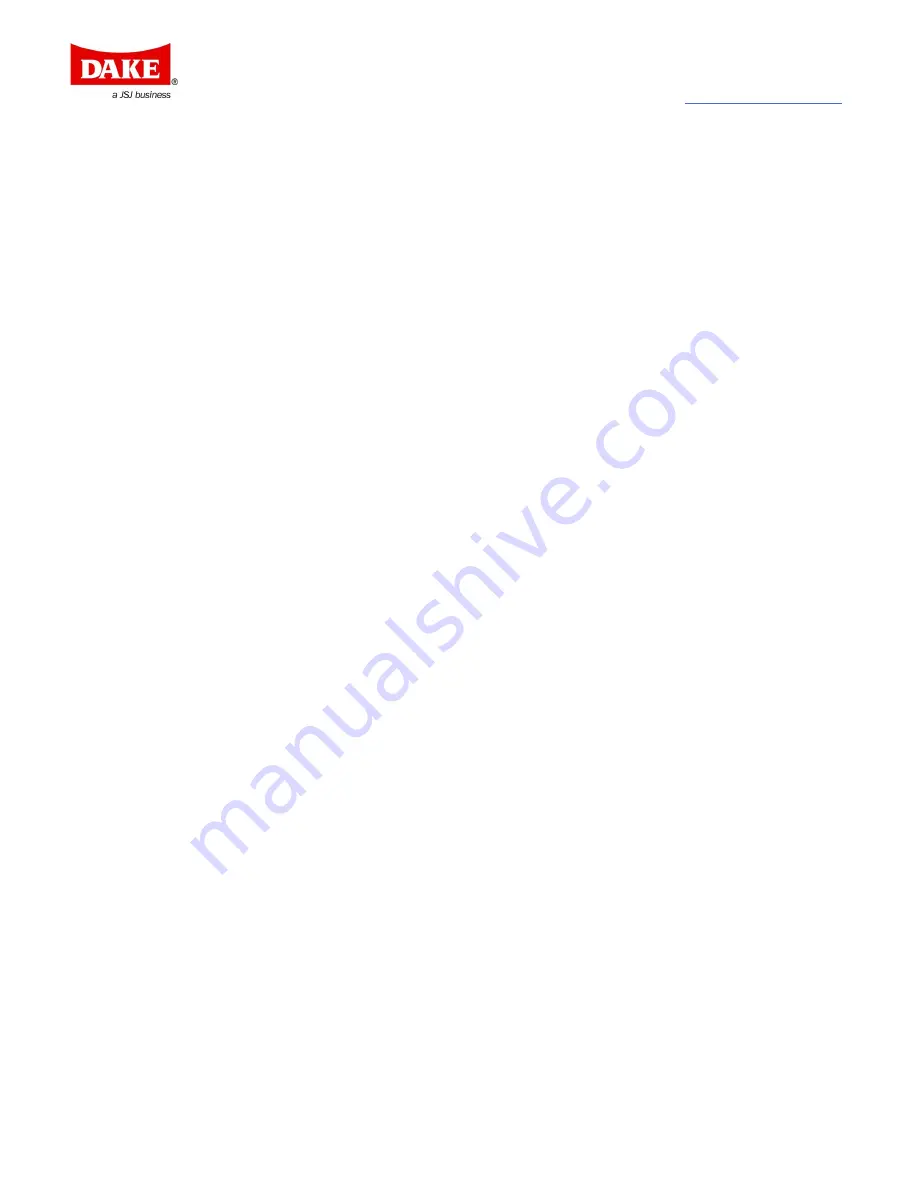
Dake Corporation
724 Robbins Road
Grand Haven, MI 49417
www.dakecorp.com
3
REV012019
RETURN & REFUND POLICY
Thank you for purchasing from Dake! If you are not entirely satisfied with your purchase, we are
here to help.
Returns
All Dake manufactured / distributed machines, parts and couplings include a 30-day return
option. These policies are valid from the date of final shipment to the end user.
To be eligible for a return, the item must be unused and in the same condition as received.
All requested warranty claims must be communicated to the distributor or representative
responsible for the sale. Once communication has been initiated, Dake Customer Service must
be contacted for approval:
Phone: (800) 937-3253
Email: [email protected]
Once the return request has been approved by Customer Service, a representative will supply a
Return Material Authorization (RMA) number. The returned item must have the provided RMA
number clearly marked on the outside packaging. Any item received without an RMA number
clearly visible on the packaging will not be processed.
An RMA number can only be provided by the Dake Customer Service team and must be
obtained prior to the return shipment.
Refunds
Once the item has been received and inspected for damages, a representative will notify the
requestor referencing the provided RMA number.
If the return is approved, a refund will be issued to the original method of payment, less a 20%
restocking fee. The restocking fee may be waived if an order is placed at the time of return with
like-value merchandise.
Transportation costs are the responsibility of the end user and will not be credited upon return
approval.
Any item that is returned after the initial 30 days or has excessive/obvious use will not be
considered for a full refund.