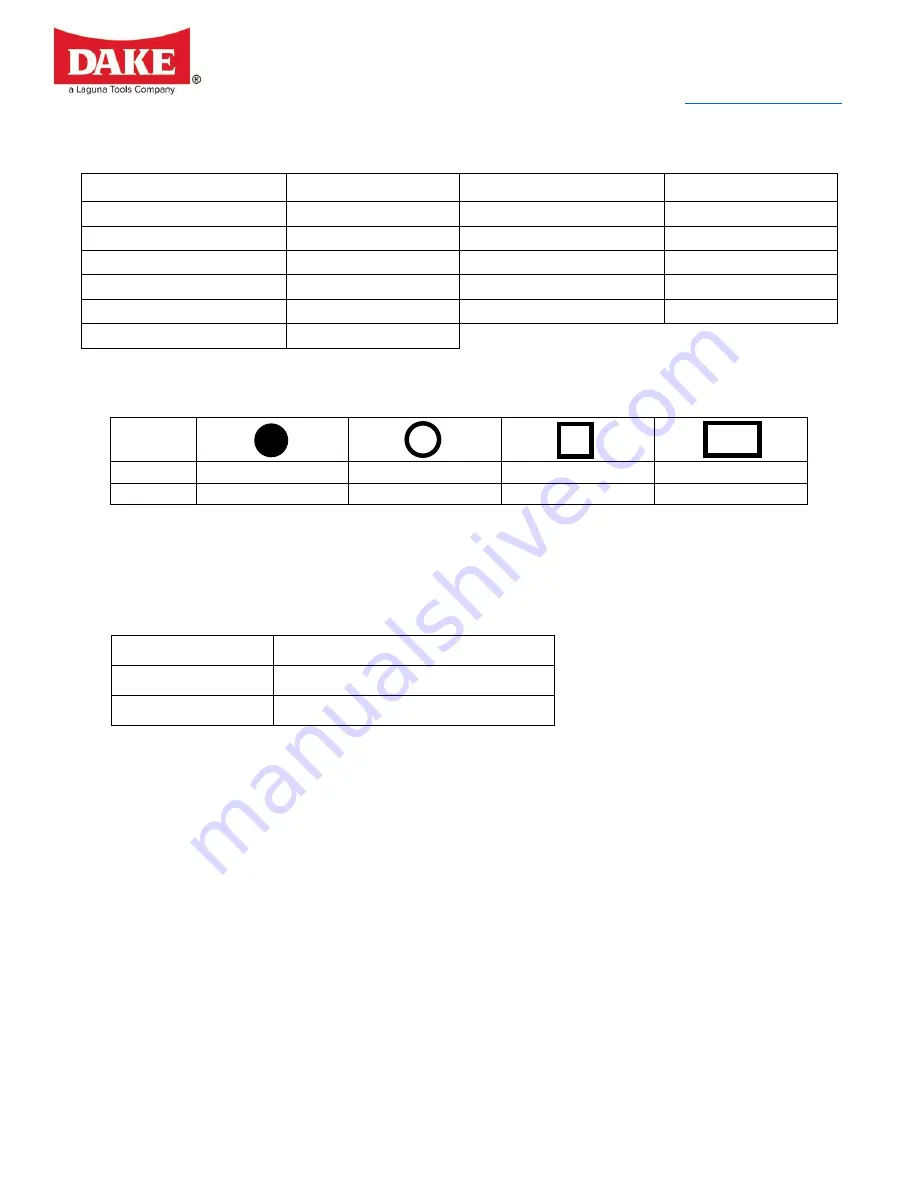
Dake Corporation
1809 Industrial Park Dr
Grand Haven, MI 49417
974355-2
5
REV112019
SPECIFICATIONS
Model
Technics 350 SA
Slotting
No
Number
974355-2
Maximum angle
60° left / 45° right
Voltage
220V/440V
Weight
890 lbs
Phase
3-Phase
Work Height
36-3/4”
Horsepower
3.5 max HP
Height
60”
Speeds
20-105 RPM
Base
33” x 50”
Max blade diameter
14”
CUTTING CAPACITY
90°
3-3/8”
4-3/4”
4-1/8”
6-1/4” x 3-1/2”
45°
3”
4”
3-3/8”
3-3/8” x 2-3/4”
In the space provided record the serial number and model number of the machine. If contacting
Dake this information must be provided to assist in identifying the specific machine.
Serial No.
Model No.
Date Purchased: