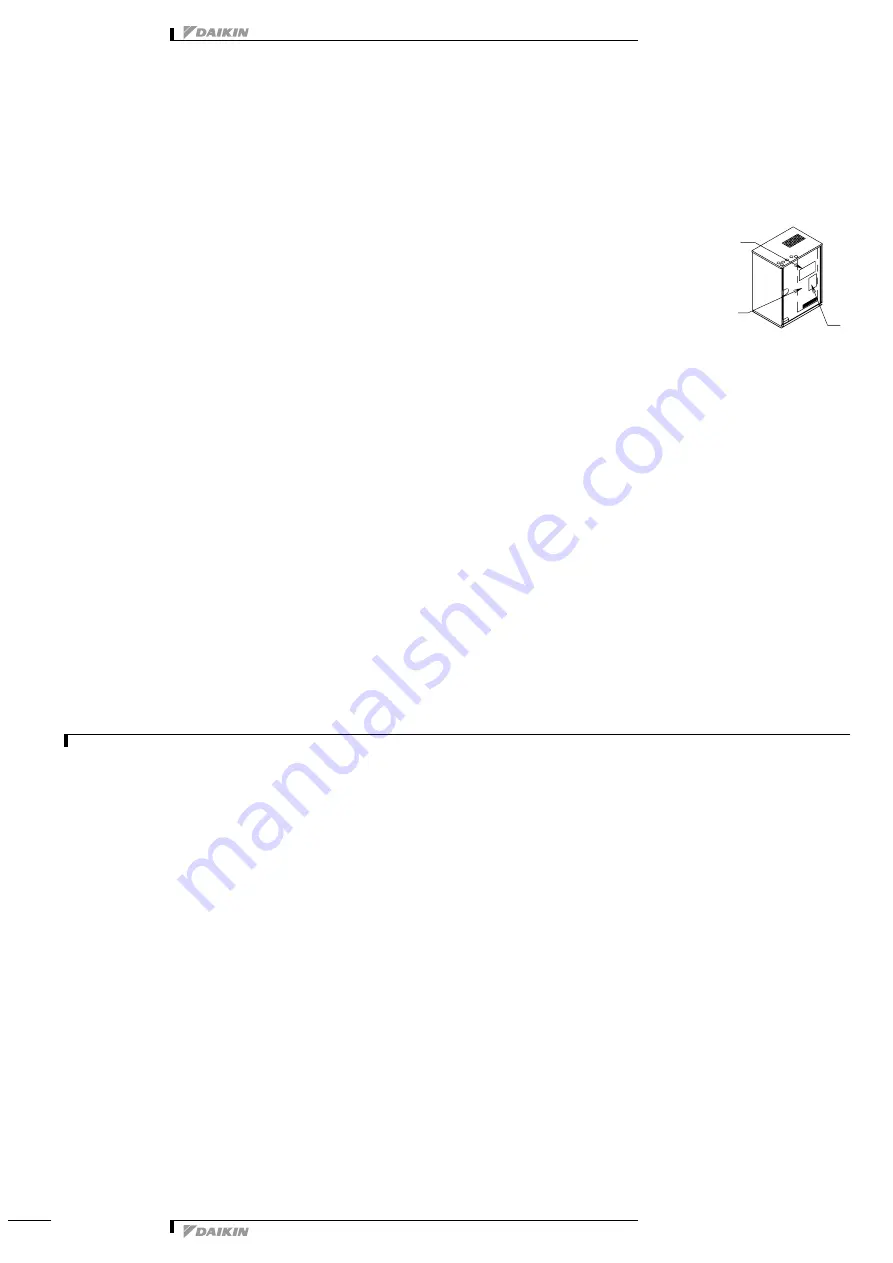
• Installation procedure
• VRV
®
Systems • Installation procedure
26
1
Installation of outdoor
1 - 8 Refrigerant piping
1 - 8 - 5
Air tight test and vacuum drying
The units were checked for leaks by the manufacturer.
Confirm that the valves are firmly closed before Air tight test or vacuum drying.
To prevent entry of any impurities and insure sufficient pressure resistance, always use the special tools dedicated for R410A.
•
Air tight test:
Make sure to use nitrogen gas.
(For the service port location, refer to the “Caution” label attached on the front panel [right] of the outside unit.)
(Refer to figure)
햲
[Service precautions] Label
햳
EL. COMPO. BOX cover
햴
[Caution] Label
Pressurize the liquid and gas pipes to 4.0MPa (40bar) (do not pressurize more than 4.0MPa (40bar)). If the pressure does
not drop within 24 hours, the system passes the test. If the pressure drops, check where the nitrogen leaks from.
•
Vacuum drying:
Use a vacuum pump which can evacuate to –100.7kPa (5Torr, –755mmHg).
1Evacuate the system from the liquid and gas pipes by using a vacuum pump for more than 2 hours and bring the system to –100.7kPa or less.
After keeping the system under that condition for more than 1 hour, check if the vacuum gauge rises or not. If it rises, the system may either
contain moisture inside or have leaks.
2Following should be executed if there is a possibility of moisture remaining inside the pipe (if piping work is carried out during the raining season
or over a long period of time rainwater may enter the pipe during work).
After evacuating the system for 2 hours, pressurize the system to 0.05MPa (vacuum break) with nitrogen gas and evacuate the system again
using the vacuum pump for 1 hour to –100.7kPa or less (vacuum drying). If the system cannot be evacuated to –100.7kPa within 2 hours,
repeat the operation of vacuum break and vacuum drying.
Then, after leaving the system in vacuum for 1 hour, confirm that the vacuum gauge does not rise.
1 - 8 - 6
Pipe insulation
After finishing the leak test and vacuum drying, the piping must be insulated. Take into account the following points:
•
Make sure to insulate the connection piping both liquid-side and gas-side and refrigerant branch kits entirely.
Not insulating them may cause leaking. (The gas piping can reach temperatures of 120°C. Be sure the insulation used can withstand such
temperatures.)
•
Reinforce the insulation on the refrigerant piping according to the installation environment. Condensation might form on the surface of the
insulation.
•
If there is a possibility that condensation on the shutoff valve might drip down into the indoor unit through gaps in the insulation and piping because
the outside unit is located higher than the indoor unit, etc., this must be prevented by caulking the connections, etc.
C
AUTION
Be sure to insulate connection piping, as touching them can cause burns.
1 - 8 - 7
Checking of device and installation conditions
Be sure to check the followings.
1
Make sure there is no faulty power wiring or loosing of a nut.
See “
10-8 Field wiring
”.
2
Make sure there is no faulty transmission wiring or loosing of a nut.
See “
10-8 Field wiring
”.
3
Make sure there is no faulty refrigerant piping.
See “
10-9 Refrigerant piping
”.
4
Make sure piping size is correct.
See “1
0-9-1 Selection of piping material
”.
5
Make sure insulation work is done.
See “
10-9-7 Pipe insulation
”.
6
Make sure insulation resistance of main power circuit is not deteriorated.
Using a megatester for 500V, check that the insulation resistance of 2M or more is attained by applying a voltage of 500V DC between power
terminals and earth. Never use the megatester for the transmission wiring (between outdoor and indoor unit, outdoor and COOL/HEAT selector
and etc.).
1
2
3