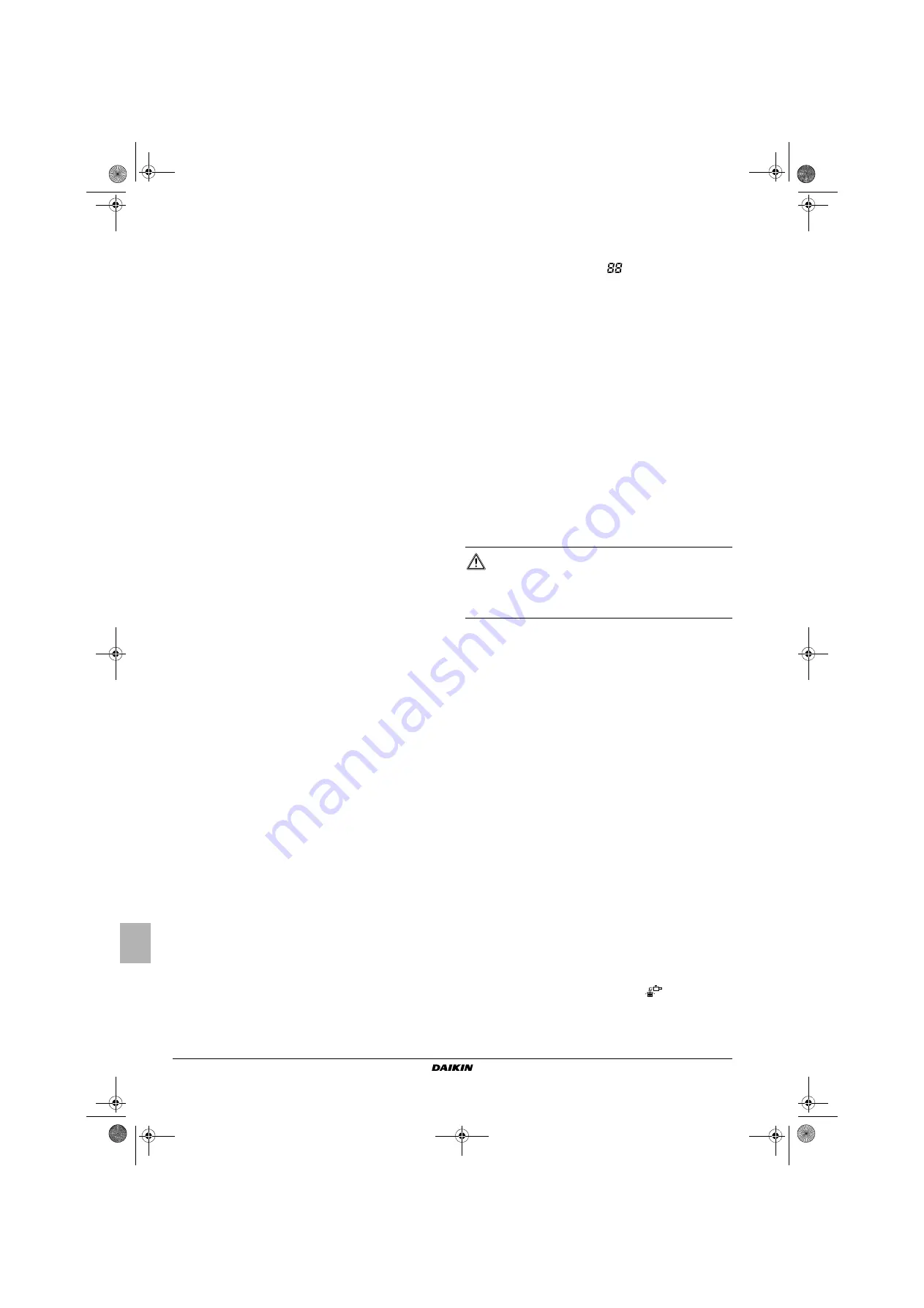
Installation and operation manual
52
10T7Y1B
VRV-W IV System Air Conditioner
4P347465-1A – 2013.04
Symptom 4: The fan strength does not correspond to the setting
The fan speed does not change even if the fan speed
adjustment button in pressed. During heating operation, when
the room temperature reaches the set temperature, the outdoor
unit goes off and the indoor unit changes to whisper fan speed.
This is to prevent cold air blowing directly on occupants of the
room. The fan speed will not change even when another indoor
unit is in heating operation, if the button is pressed.
Symptom 5: The fan direction does not correspond to the
setting
The fan direction does not correspond with the user interface
display. The fan direction does not swing. This is because the
unit is being controlled by the micro computer.
Symptom 6: White mist comes out of a unit
Indoor unit:
When humidity is high during cooling operation
If the interior of an indoor unit is extremely contaminated, the
temperature distribution inside a room becomes uneven. It is
necessary to clean the interior of the indoor unit. Ask your dealer
for details on cleaning the unit. This operation requires a
qualified service person.
Immediately after the cooling operation stops and if the room
temperature and humidity are low. This is because warm
refrigerant gas flows back into the indoor unit and generates
steam.
Symptom 7: The user interface display reads "
U4
" or "
U5
" and
stops, but then restarts after a few minutes
This is because the user interface is intercepting noise from
electric appliances other than the air conditioner. The noise
prevents communication between the units, causing them to
stop. Operation automatically restarts when the noise ceases.
Symptom 8: Noise of air conditioners
Symptom 8.1: Indoor unit
A "zeen" sound is heard immediately after the power supply is
turned on.
The electronic expansion valve inside an indoor unit starts
working and makes the noise. Its volume will reduce in about
one minute.
A continuous low "shah" sound is heard when the system is in
cooling operation or at a stop.
When the drain pump (optional accessories) is in operation, this
noise is heard.
A "pishi-pishi" squeaking sound is heard when the system stops
after heating operation.
Expansion and contraction of plastic parts caused by
temperature change make this noise.
A low "sah", "choro-choro" sound is heard while the indoor unit is
stopped.
When another indoor unit is in operation, this noise is heard. In
order to prevent oil and refrigerant from remaining in the system,
a small amount of refrigerant is kept flowing.
Symptom 8.2: Indoor unit, outdoor unit
A continuous low hissing sound is heard when the system is in
cooling or defrost operation. This is the sound of refrigerant gas
flowing through both indoor and outdoor units.
A hissing sound which is heard at the start or immediately after
stopping operation or defrost operation. This is the noise of
refrigerant caused by flow stop or flow change.
Symptom 8.3: Outdoor unit
When the tone of operating noise changes.
This noise is caused by the change of frequency.
Symptom 9: Dust comes out of the unit
When the unit is used for the first time in a long time.
This is because dust has gotten into the unit.
Symptom 10: The units can give off odours
The unit can absorb the smell of rooms, furniture, cigarettes,
etc., and then emit it again.
Symptom 11: The display shows "
"
This is the case immediately after the main power supply switch
is turned on and means that the user interface is in normal
condition. This continues for one minute.
Symptom 12: The compressor in the outdoor unit does not stop
after a short heating operation
This is to prevent refrigerant from remaining in the compressor.
The unit will stop after 5 to 10 minutes.
Symptom 13: The inside of an outdoor unit is warm even when
the unit has stopped
This is because the crankcase heater is warming the
compressor so that the compressor can start smoothly.
Symptom 14: Hot air can be felt when the indoor unit is stopped
Several different indoor units are being run on the same system.
When another unit is running, some refrigerant will still flow
through the unit.
10. Troubleshooting
If one of the following malfunctions occur, take the measures shown
below and contact your dealer.
The system must be repaired by a qualified service person:
If a safety device such as a fuse, a breaker or an earth leakage
breaker frequently actuates or the ON/OFF switch does not
properly work.
Measure: Turn off the main power switch.
If water leaks from the unit.
Measure: Stop the operation.
The operation switch does not work well.
Measure: Turn off the power.
If the user interface display indicates the unit number, the
operation lamp flashes and the malfunction code appears.
Measure: Notify your installer and report the malfunction code.
If the system does not properly operate except for the above
mentioned cases and none of the above mentioned malfunctions is
evident, investigate the system according to the following
procedures.
1
If the system does not operate at all:
Check that there is no power failure.
Wait until power is restored. If power failure occurs during
operation, the system automatically restarts immediately
after the power supply is recovered.
Check that no fuse has blown or breaker has worked.
Change the fuse or reset the breaker if necessary.
2
If the system goes into fan only operation, but as soon as it goes
into heating or cooling operation, the system stops:
Check that the air inlet or outlet of the indoor unit is not blocked
by obstacles. Remove any obstacle and make it well-ventilated.
Check that the water inlet or outlet of the outdoor unit is not
blocked.
Check if the user interface display shows
(time to clean the
air filter). (Refer to
"8. Maintenance" on page 51
and
"Maintenance" in the indoor unit manual.)
Check all valves in the water piping system. Open all valves.
Check if the water filter is blocked. Clean the strainer.
WARNING
Stop operation and shut off the power if anything
unusual occurs (burning smells etc.).
Leaving the unit running under such circumstances may
cause breakage, electric shock or fire. Contact your dealer.
4P347465-1A.book Page 52 Monday, August 5, 2013 2:26 PM