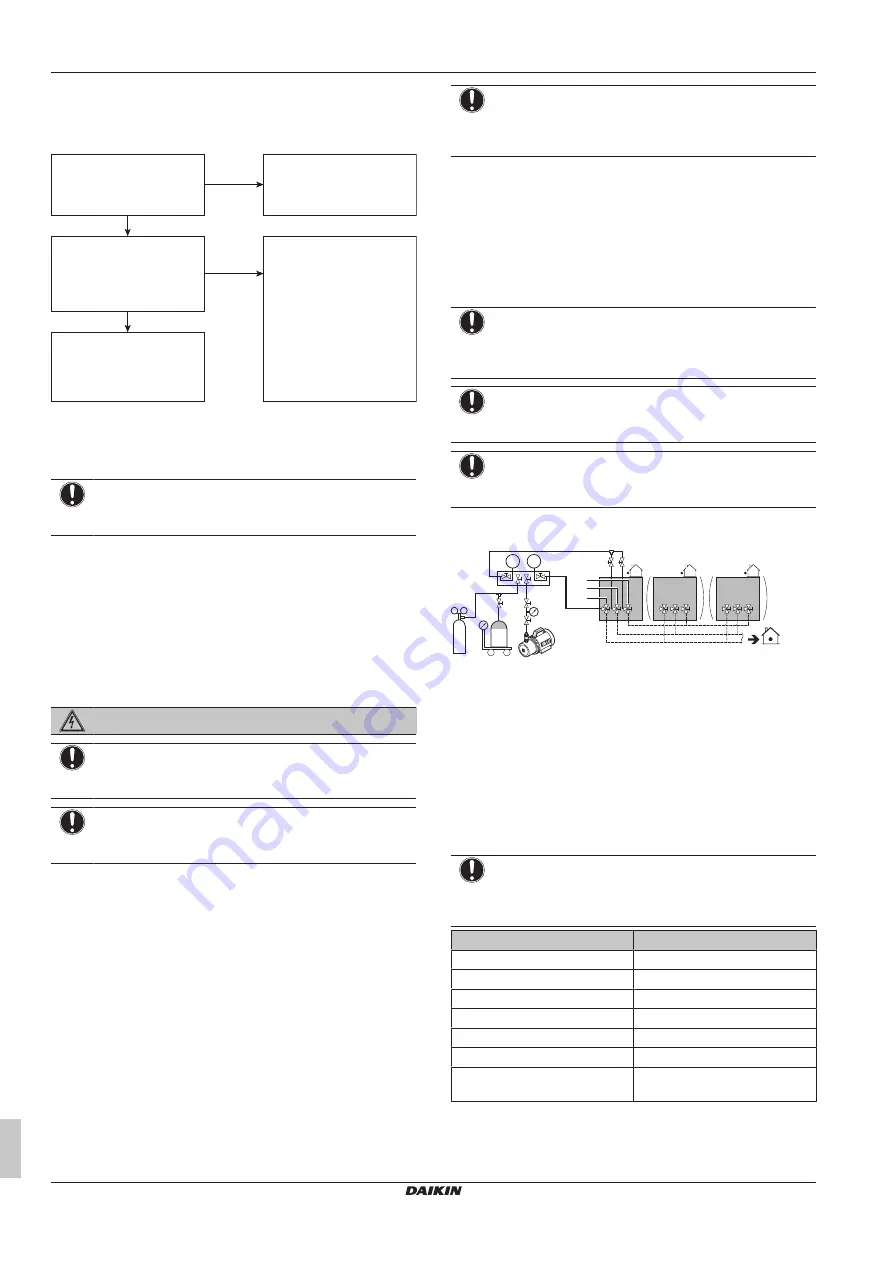
14 Piping installation
Installation and operation manual
24
RWEYQ8~14T9Y1B
VRV IV water-cooled system air conditioner
4P452190-1D – 2020.10
14.4
Checking the refrigerant piping
14.4.1
About checking the refrigerant piping
Refrigerant piping works are
finished?
The indoor units and/or
outdoor unit were already
powered ON?
Use procedure:
"Method 2: After power ON".
Finish piping work.
Use procedure:
"Method 1: Before power ON
(regular method)".
Yes
No
No
Yes
It is very important that all refrigerant piping work is done before the
units (outdoor or indoor) are powered on. When the units are
powered on, the expansion valves will initialise. This means that the
valves will close.
NOTICE
Leak test and vacuum drying of field piping and indoor
units is impossible when field expansion valves are closed.
Method 1: Before power ON
If the system has not yet been powered on, no special action is
required to perform the leak test and the vacuum drying.
Method 2: After power ON
If the system has already been powered on, activate setting [2‑21]
(refer to
"16.1.4 To access mode 1 or 2"
33]). This setting will
open field expansion valves to guarantee a refrigerant piping
pathway and make it possible to perform the leak test and the
vacuum drying.
DANGER: RISK OF ELECTROCUTION
NOTICE
Make sure that all indoor units connected to the outdoor
unit are powered on.
NOTICE
Wait to apply setting [2‑21] until the outdoor unit has
finished the initialisation.
Leak test and vacuum drying
Checking the refrigerant piping involves:
▪ Checking for any leakages in the refrigerant piping.
▪ Performing vacuum drying to remove all moisture, air or nitrogen
in the refrigerant piping.
If there is a possibility of moisture being present in the refrigerant
piping (for example, water may have entered the piping), first carry
out the vacuum drying procedure below until all moisture has been
removed.
All piping inside the unit has been factory tested for leaks.
Only field installed refrigerant piping needs to be checked.
Therefore, make sure that all the outdoor unit stop valves are firmly
closed before performing leak test or vacuum drying.
NOTICE
Make sure that all (field supplied) field piping valves are
OPEN (not outdoor unit stop valves!) before you start leak
test and vacuuming.
For more information on the state of the valves, refer to
"14.4.3 Checking refrigerant piping: Setup"
14.4.2
Checking refrigerant piping: General
guidelines
Connect the vacuum pump through a manifold to the service port of
all stop valves to increase efficiency (refer to
24]).
NOTICE
Use a 2-stage vacuum pump with a non-return valve or a
solenoid valve that can evacuate to a gauge pressure of
–100.7 kPa (–1.007 bar) (5 Torr absolute).
NOTICE
Make sure the pump oil does not flow oppositely into the
system while the pump is not working.
NOTICE
Do NOT purge the air with refrigerants. Use a vacuum
pump to evacuate the installation.
14.4.3
Checking refrigerant piping: Setup
p< p>
R410A
N2
C
(1)
D
b
c
e
a
g
h
f
d
A
B
a
Pressure reducing valve
b
Nitrogen
c
Weighing scales
d
Refrigerant R410A tank (siphon system)
e
Vacuum pump
f
Liquid line stop valve
g
Gas line stop valve
h
High pressure/low pressure gas line stop valve
A
Valve A
B
Valve B
C
Valve C
(1)
D
Valve D
(1)
Only for heat recovery system.
NOTICE
Do not connect the vacuum pump to the suction gas stop
valve if the unit is intended to run as a heat pump system.
This will increase the risk of unit failure.
Valve
State of valve
Valve A
Open
Valve B
Open
Valve C
Open
Valve D
Open
Liquid line stop valve
Close
Gas line stop valve
Close
High pressure/low pressure gas
line stop valve
Close
Summary of Contents for VRV IV RWEYQ-T9
Page 39: ......