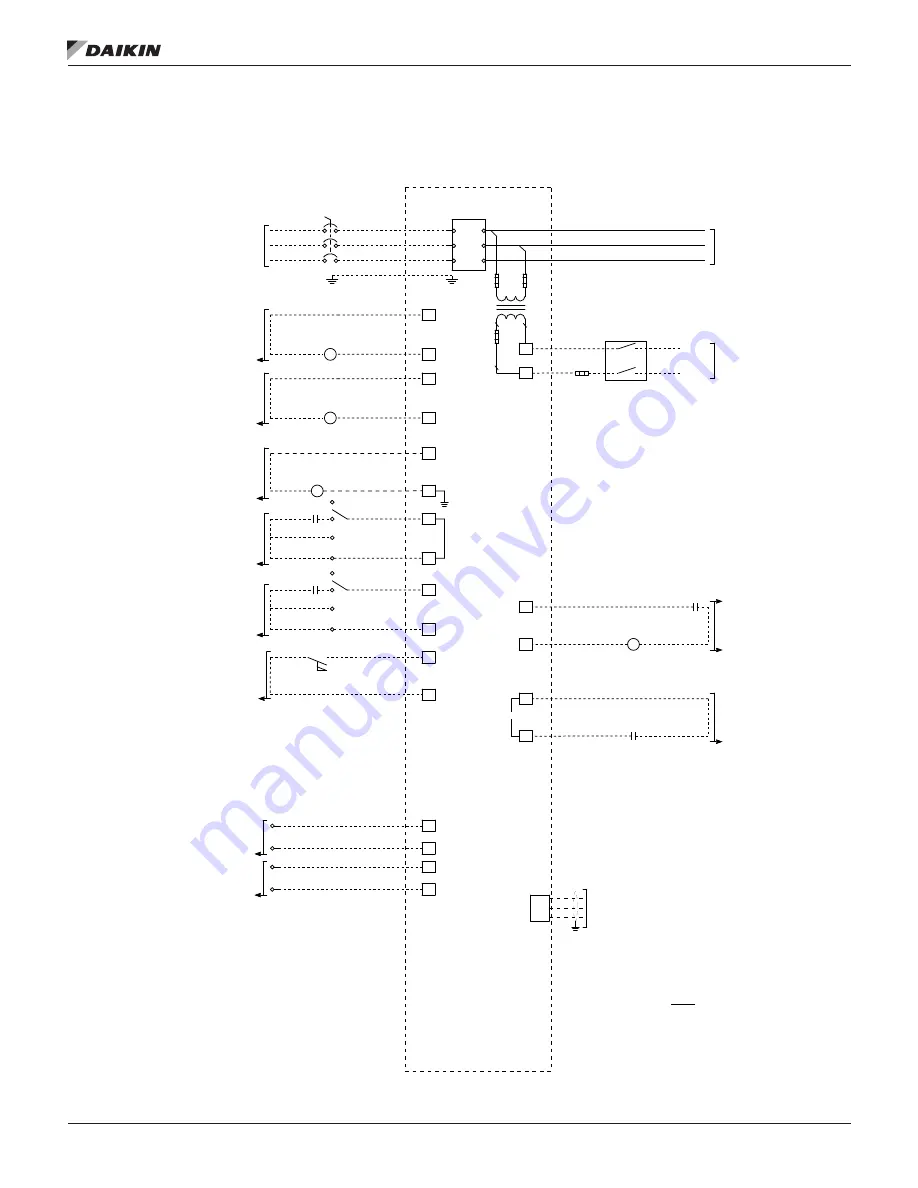
IOM 1206-13 • TRAILBLAZER
®
MODEL AGZ CHILLERS
48 www.DaikinApplied.com
Electrical Data
Figure 52: Typical Packaged Unit Field Wiring Diagram (Single-Point Connection)
NO
COM
BELL
4-20MA FOR
DEMAND LIMIT
(BY OTHERS)
4-20MA FOR
EVAP. - LWT RESET
(BY OTHERS)
DOUBLE SET POINT/MODE
SWITCH
(BY OTHERS)
**TIME CLOCK
OFF
MANUAL **
ON
AUTO
585
IF REMOTE STOP
CONTROL IS USED
REMOVE LEAD 585
FROM TERM
TB2-52 TO TB2-72
** TIME CLOCK
OFF
MANUAL **
ON
AUTO
71
TB2
70
TB2
69
TB2
68
TB2
TB1
22
TB1
1A
TO
COMPRESSOR(S)
AND FAN MOTORS
ALARM BELL
RELAY
120
VAC
T1
FU6
CONTROL
CIRCUIT
FUSE
SEE NOTE 2
FU4
REMOTE
STOP SWITCH
(BY OTHERS)
TB2
TB2
43
83
UNIT ALARM
120 VAC
TB1
TB1
TB2
TB2
TB2
TB2
54
52
34
74
72
32A
ALARM
BELL OPTION
3 PHASE
POWER
SOURCE
DISCONNECT SWITCH
OR
POWER BLOCK
CIRCUIT BREAKER
(BY OTHERS)
1
2
TB2
TB2
45
67
EXTERNAL
ALARM/
EVENT
DISCONNECT
(BY OTHERS)
N
120 VAC
OPTIONAL
FIELD SUPPLIED
CONTROL POWER
FU
15A for 1.5 KVA
30A for 3.0KVA
(BY OTHERS)
301A
301
299
ABR
555A
IF EXTERNAL
ALARM/EVENT
IS USED
REMOVE LEAD 555A
FROM TERM
TB2-45 TO TB2-67
N
24 VAC
FIELD WIRING DIAGRAM
WITH MICROTECH CONTROLLER
ALARM BELL RELAY
120VAC @ 1.0AMP MAX
EARTH
GROUND
ABR
24VAC @ 0.4AMP MAX.
**
**
FU5
Notes:
1.) ALL FIELD WIRING TO BE INSTALLED AS
NEC CLASS 1 WIRING SYSTEM WITH
CONDUCTOR RATED 600 VOLTS.
2.) IF FIELD SUPPLIED, CONTROL POWER USER
MUST REMOVE FU6, AND WIRE NUMBERS
299, 301A INSIDE CONTROL PANEL
3.) ** = USE 'DRY CONTACTS' ONLY. DO NOT
SUPPLY FIELD POWER TO THIS CIRCUIT
4.) DO NOT SUPPLY FIELD POWER TO
24VAC OR 120VAC CONTROL CIRCUITS.
CHWR2
PUMP NO.2 RELAY
(BY OTHERS)
120VAC @ 1.0AMP MAX
N
N
120 VAC
120 VAC
TB1
TB1
TB1
TB1
P2+
CHWR1
PUMP NO.1 RELAY
(BY OTHERS)
120VAC @ 1.0AMP MAX
35
31
33
(+)
(-)
REF
TO/FROM BAS
(CUSTOMER
CONNECTION)
CONNECT TO GROUND
AT ONE END ONLY.
TB2
44
61
TB2
DI2
M
Flow Switch Contacts
Use dry contacts only. DO NOT
supply Field Power to this circuit
NOTE: For Factory Supplied Thermal
Dispersion Flow Switch wiring,
see wiring instruction kit.
_
+
_
+
GND
T3
T2
T1
L3
L2
L1
PANEL
BACNET-MSTP
GND
To UC DI2