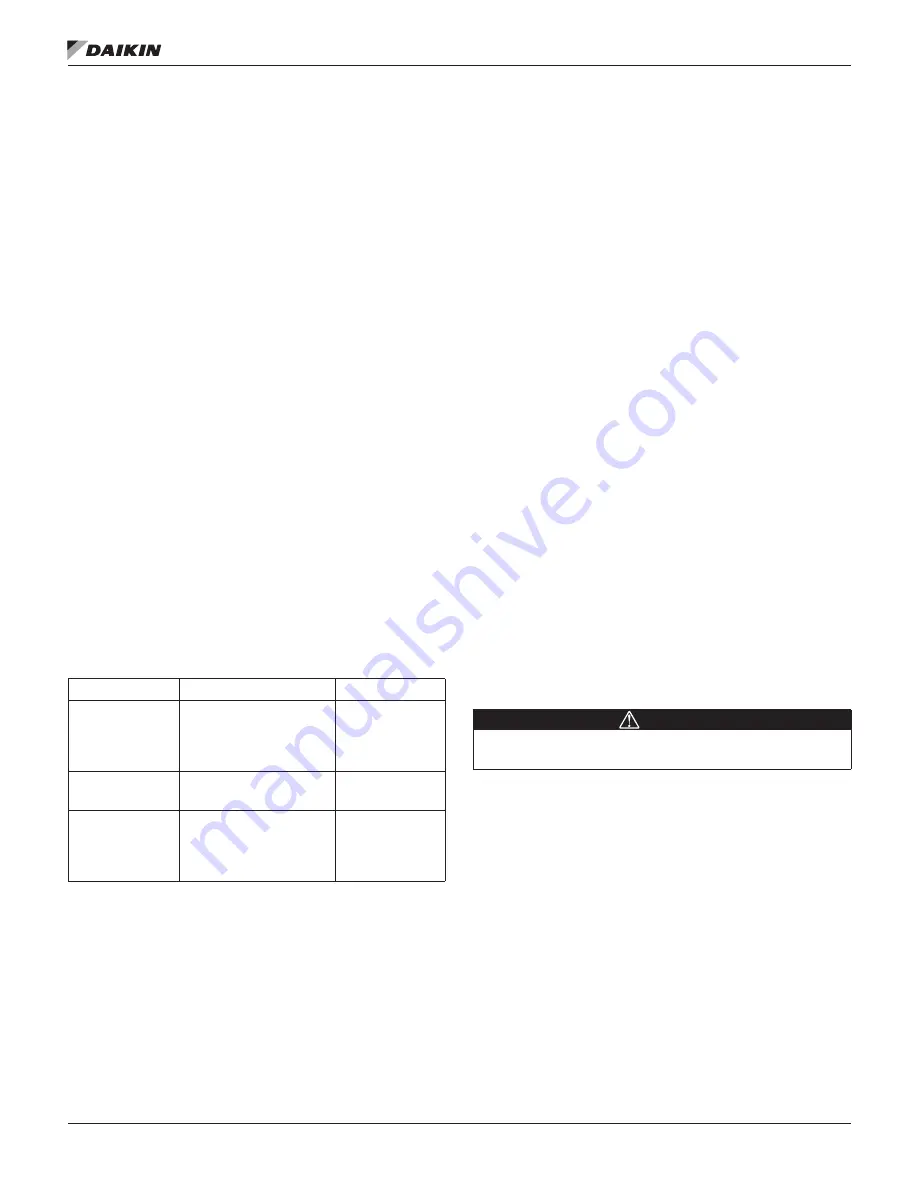
Unit Maintenance
www.DaikinApplied.com 109
IOM 1206-13 • TRAILBLAZER
®
MODEL AGZ CHILLERS
Periodic Clean Water Rinse
A monthly clean water rinse is recommended for coils that are
applied in coastal or industrial environments to help to remove
chlorides, dirt and debris. An elevated water temperature (not
to exceed 130ºF) will reduce surface tension, increasing the
ability to remove chlorides and dirt. Pressure washer PSI must
not exceed 900 psig and the nozzle should remain at least 1
foot from the coil to avoid damaging fin edges.
Routine Quarterly Cleaning of Epoxy Coated
Coil Surfaces
Quarterly cleaning is essential to extend the life of an epoxy
coated coil and is required to maintain warranty coverage.
Coil cleaning shall be part of the unit’s regularly scheduled
maintenance procedures. Failure to clean epoxy coated coils
will void the warranty and may result in reduced efficiency and
durability in the environment.
For routine quarterly cleaning, first clean the coil with an
approved coil cleaner (see approved products list in
).
After cleaning the coils with the approved cleaning agent, use
the approved chloride remover to remove soluble salts and
revitalize the unit.
Recommended Coil Cleaner
The following cleaning agent, assuming it is used in
accordance with the manufacturer’s directions on the container
for proper mixing and cleaning, has been approved for use on
epoxy coated coils to remove mold, mildew, dust, soot, greasy
residue, lint and other particulate:
Table 88: Epoxy Coated Coil Recommended Cleaning
Agents
Cleaning Agent
Reseller
Part Number
Enviro-Coil
Concentrate
Hydro-Balance Corp
P.O. Box 730
Prosper, TX 75078
800-527-5166
H-EC01
Enviro-Coil
Concentrate
Home Depot
H-EC01
Chloride
Remover
Chlor*Rid Int’l, Inc.
P.O. Box 908
Chandler, AZ 85244
800-422-3217
Chlor*Rid DTS
CHLOR*RID DTS™ should be used to remove soluble salts
from epoxy coated coils, but the directions must be followed
closely. This product is not intended for use as a degreaser.
Any grease or oil film should first be removed with the
approved cleaning agent.
1. Remove Barrier - Soluble salts adhere themselves
to the substrate. For the effective use of this product,
the product must be able to come in contact with the
salts. These salts may be beneath any soils, grease or
dirt; therefore, these barriers must be removed prior to
application of this product. As in all surface preparation,
the best work yields the best results.
2. Apply CHLOR*RID DTS - Apply CHLOR*RID DTS
directly onto the substrate. Sufficient product must be
applied uniformly across the substrate to thoroughly
wet out surface with no areas missed. This may
be accomplished by use of a pump-up sprayer or
conventional spray gun. The method does not matter, as
long as the entire area to be cleaned is wetted. After the
substrate has been thoroughly wetted, the salts will be
soluble and is now only necessary to rinse them off.
3. Rinse - It is highly recommended that a hose be used
as a pressure washer will damage the fins. The water to
be used for the rinse is recommended to be of potable
quality, though a lesser quality of water may be used if a
small amount of CHLOR*RID DTS is added. Check with
CHLOR*RID International, Inc. for recommendations on
lesser quality rinse water.
Harsh Chemical and Acid Cleaners
Harsh chemicals, household bleach or acid cleaners should
not be used to clean outdoor or indoor epoxy coated coils.
These cleaners can be very difficult to rinse out of the coil and
can accelerate corrosion and attack the epoxy coating. If there
is dirt below the surface of the coil, use the recommended coil
cleaners as described above.
High Velocity Water or Compressed Air
High velocity water from a pressure washer or compressed air
should only be used at a very low pressure to prevent fin and/
or coil damages. The force of the water or air jet may bend the
fin edges and increase airside pressure drop. Reduced unit
performance or nuisance unit shutdowns may occur.
DANGER
Electric shock hazard. Turn off all power before continuing
with following service.
Evaporator
On AGZ-E models 030 through 241, the evaporator is a
compact, high efficiency, dual circuit, brazed plate-to-plate type
heat exchanger consisting of parallel stainless steel plates.
The evaporator is protected with an electric resistance heater
and insulated with 3/4” (19mm) thick closed-cell polyurethane
insulation. This combination provides freeze protection down
to -20°F (-29°C) ambient air temperature. The water side
working pressure of the brazed plate type of evaporator is 653
psig (4502 kPa). Evaporators are designed and constructed
according to, and listed by, Underwriters Laboratories (UL).
Other than cleaning and testing, no service work should be
required on the evaporator.