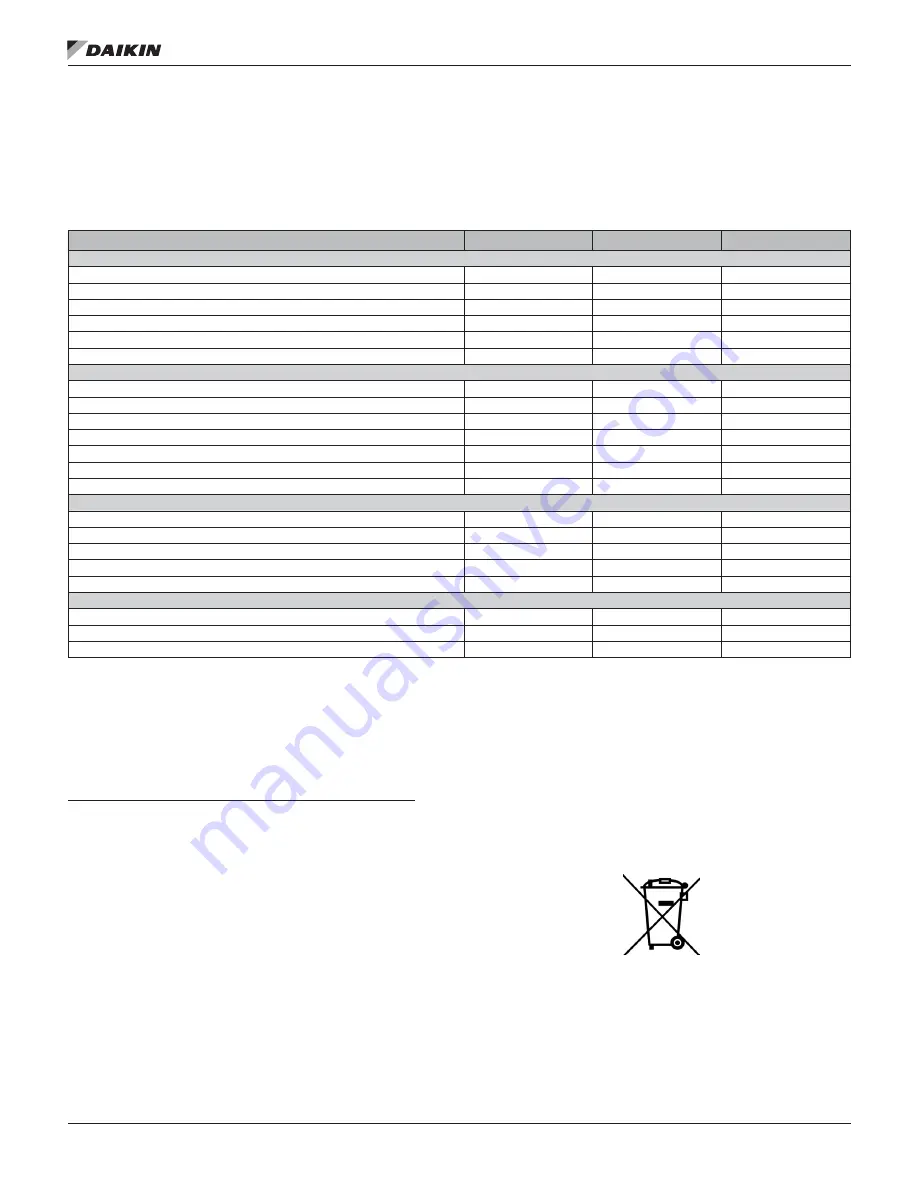
Periodic Obligatory Checks and Start Ups for Appliances under Pressure
The units are included in a Category II classification established by the European Directive PED 97/23/EC. For equipment
belonging to this category, some local regulations require a periodic inspection by an authorized agency . Check with your local
requirements .
Table 16: Routine Maintenance Program
List of Activities
Weekly
Monthly
1
Yearly
2
General
Reading of operating data
3
X
Visual inspection of machine for any damage and/or loosening
X
Verification of thermal insulation integrity
X
Clean and paint where necessary
X
Analysis of water
5
X
Check of flow switch operation
X
Electrical
Verification of control sequence
X
Verify contactor wear – Replace if necessary
X
Verify that all electrical terminals are tight – Tighten if necessary
X
Clean inside the electrical control board
X
Visual inspection of components for any signs of overheating
X
Verify operation of compressor and electrical resistance
X
Measure compressor motor insulation using a Megger Insulation Resistance Tester
X
Refrigeration circuit
Check for any refrigerant leakage
X
Verify refrigerant flow using the liquid sight glass – Sight glass full
X
Verify filter dryer pressure drop
X
Analyze compressor vibrations
X
Analyze compressor oil acidity
6
X
Condenser section
Clean condenser banks
4
X
Verify that fans are well tightened
X
Verify condenser bank fins – Comb if necessary
X
Notes:
1 . Monthly activities include all the weekly ones .
2 . The annual (or early season) activities include all weekly and monthly activities .
3 . Unit operating values should be read on a daily basis thus keeping high observation standards .
4 . In environments with a high concentration of air-borne particles, it may be necessary to clean the condenser bank more often .
5 . Check for any dissolved metals .
6. TAN (Total Acid Number): ≤ 0, 10 — No action
Between 0.10 and 0.19 — Replace anti-acid filters and recheck after 1,000 running hours. Continue to replace filters until the TAN is
lower than 0 .1 .
> 0, 19 — Replace oil, oil filter and filter dryer . Verify at regular intervals .
Important Information Regarding the Refrigerant Used
This product contains fluorinated greenhouse gases covered by the Kyoto
Protocol . Do not vent gases into the atmosphere .
Refrigerant type = R134A
GWP(1) value = 1300
(1) GWP
= Global Warming Potential
The refrigerant quantity necessary for standard operation is indicated on the unit
name plate .
Real refrigerant quantity charged in the unit is listed on a silver sticker inside the
electrical panel .
Periodical inspections for refrigerant leaks may be required depending on
European or local legislation .
Please contact your local dealer for more information .
Disposal
The unit is made of metal, plastic and electronic parts . All these parts must be
disposed of in accordance with the local regulations in terms of disposal .
Lead batteries must be collected and sent to specific refuse collection centers.
Oil must be collected and sent to specific refuse collection centers.
This manual is a technical aid and does not represent a binding offer. The content cannot be held as explicitly or implicitly guaranteed as complete, precise or reliable. All data and specifications
contained herein may be modified without notice. The data communicated at the moment of the order shall hold firm. The manufacturer shall assume no liability whatsoever for any direct or indirect
damage, in the widest sense of the term, ensuing from or connected with the use and/or interpretation of this manual . We reserve the right to make changes in design and construction at any time
without notice, thus the cover picture is not binding .
s
ysTem
m
aInTenanCe
www .DaikinApplied .com
41
IM 1032-2 • Self-Contained Air Conditioning Systems