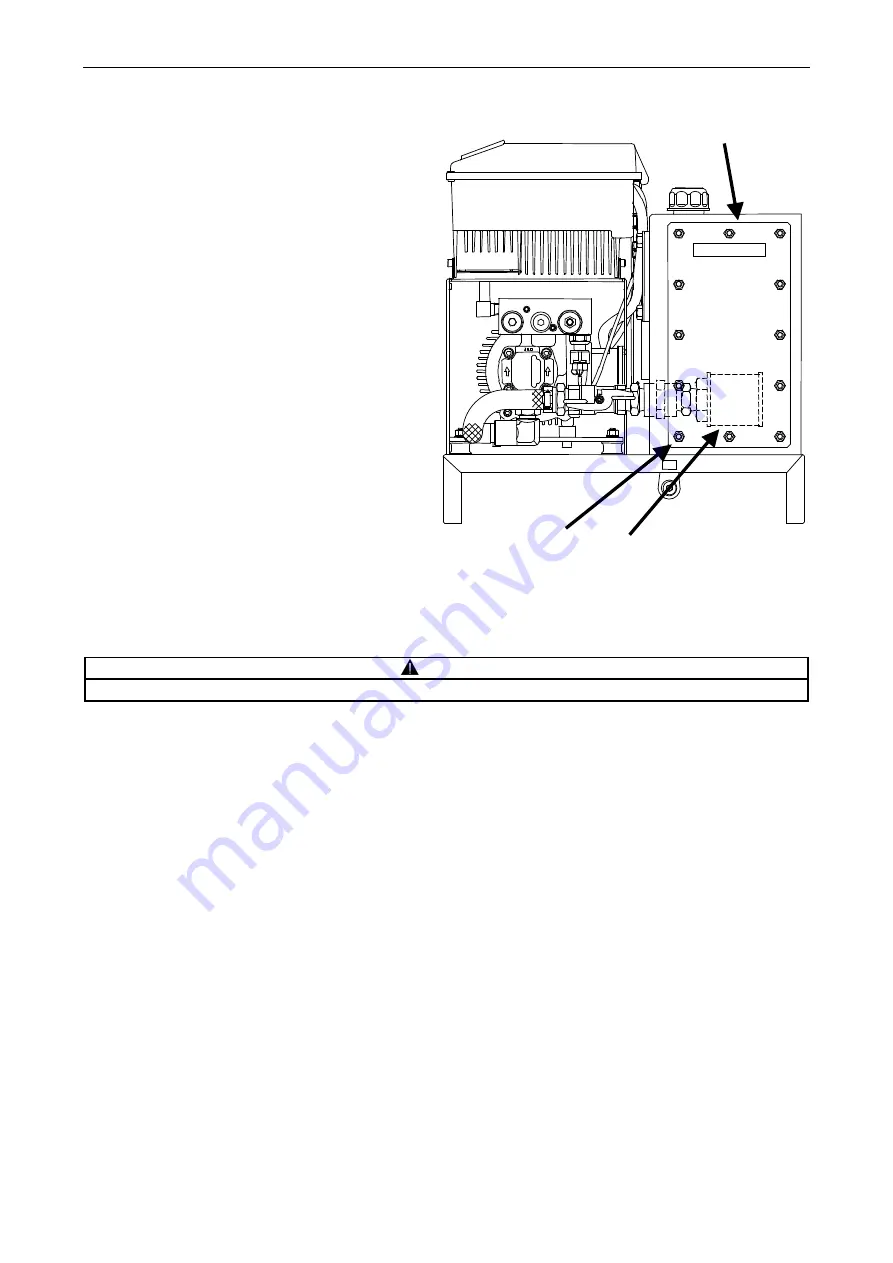
SE-04753
[Operation Manual]
40/49
DAIKIN INDUSTRIES, LTD.
Suction strainer maintenance procedure
1.
Removing procedure
[1] After draining hydraulic oil completely,
remove the nuts (M8: 12 pieces) from the
cleaning door cover, and remove the
cover from the cleaning door.
[2] You can see the suction strainer. Loosen
the strainer, and remove it.
(Hexagon nut, Width across flats: 41 mm)
2.
Cleaning procedure
Blow air onto the filter to blow off dust
accumulated on/adhering to the filter.
Remove dust from inside of the strainer
cylinder.
3.
Reassembling the strainer
After cleaning is completed, reassemble
the suction strainer. Follow the removing
procedure in reverse.
After reassembling is completed, conduct
the test run procedure described on p. 24
to make sure that the hydraulic unit
normally operates.
WARNING
During air blow, wear protective goggles to prevent accumulated substances or dust from touching your eyes.
Suction strainer
Nut
Cleaning door cover
Cleaning door tightening
precaution nameplate