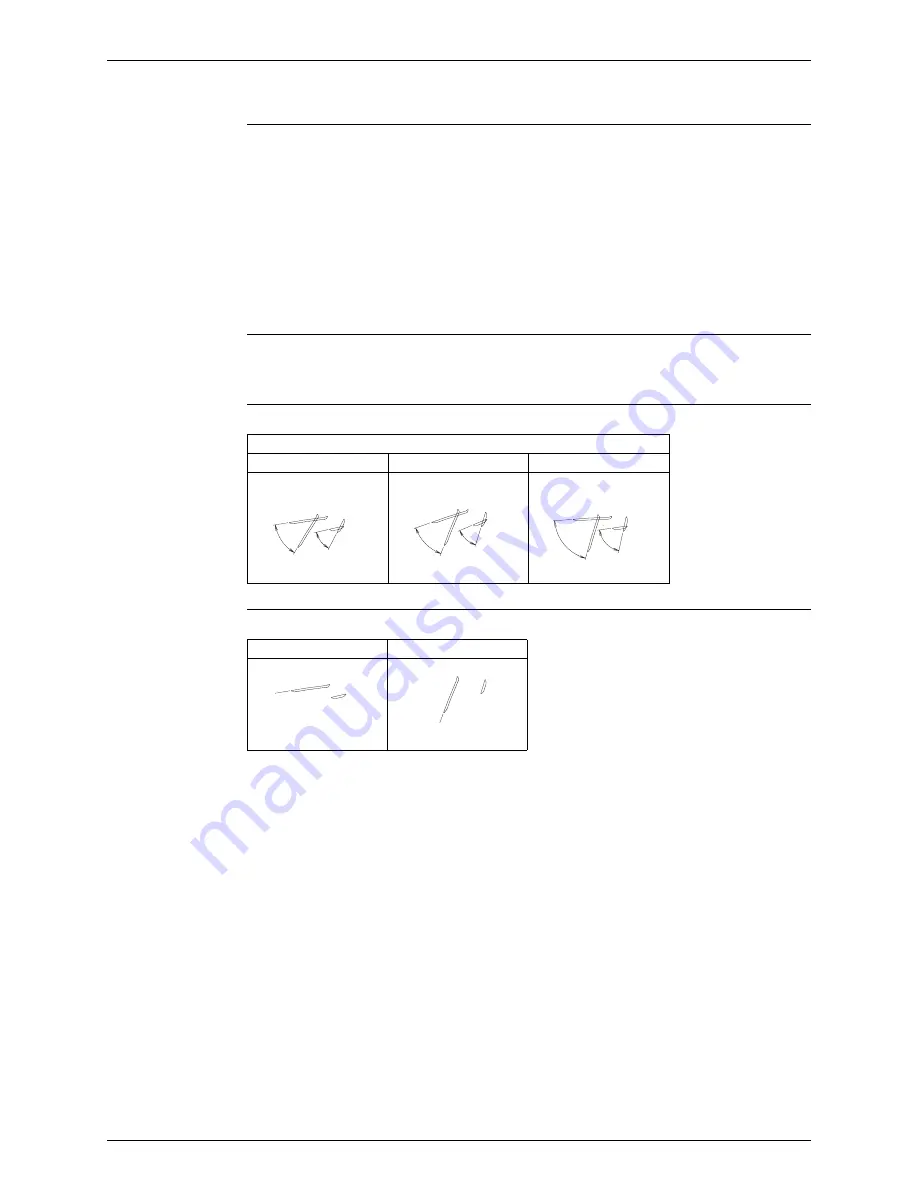
SiBE041012_A
Main Functions
Function and Control
22
1.4
Airflow Direction Control
Power-Airflow
Dual Flaps
The large flap sends a large volume of air downwards to the floor. The flap provides an optimum
control in cooling, dry, and heating mode.
Cooling / Dry Mode
During cooling or dry mode, the flap retracts into the indoor unit. Then, cool air can be blown far
and distributed all over the room.
Heating Mode
During heating mode, the large flap directs airflow downwards to spread the warm air to the
entire room.
Wide-Angle
Louvers
The louvers, made of elastic synthetic resin, provide a wide range of airflow that guarantees a
comfortable air distribution.
Auto-Swing
The following table explains the auto swing process for cooling, dry, heating, and fan :
COMFORT
AIRFLOW
Operation
The vertical swing flap is controlled not to blow the air directly on the person in the room.
Vertical Swing (up and down)
Cooling / Dry
Heating
Fan
(R11662)
10˚
15˚
60˚
65˚
(R11664)
20˚
70˚
25˚
75˚
(R11663)
5˚
10˚
80˚
75˚
Cooling
Heating
(R11665)
5˚
(R11666)
75˚